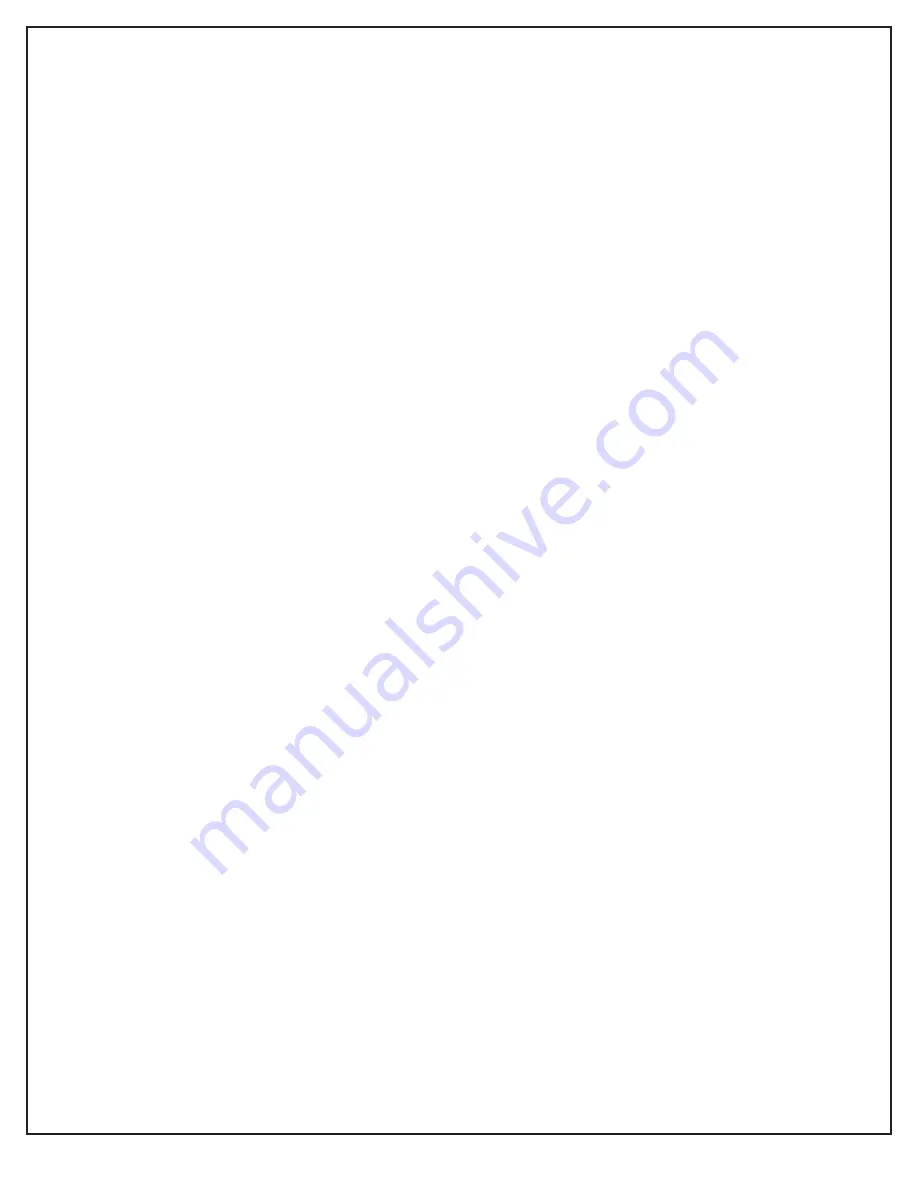
6
Presto Lifts
PPS2200-101AS,125AS,150AS Manual
4. Electrical cables and wiring harness
5. Loose or missing parts
6. Nameplates, precautionary and instructional markings and/or labeling
7. Guarding system
8.
Items specified by the manufacturer
Problem or Malfunctions
- Any problems or malfunctions that affect the safety of operations shall
be repaired prior to the use of the machine.
Before Operations -
The operator shall:
1. Read and understand the manufacturer’s operating instruction(s) and user’s safety rules or
have them explained
2. Understand all labels, warnings, and instructions displayed on the machine or have them
explained.
Workplace Inspections
- Before the machine is used and during use, the operator shall check
the area in which the machine is to be used for possible hazards such as, but not limited to:
1.
Bumps, floor obstructions and uneven surfaces
2. Overhead obstructions and electrical hazards
3. Presence of unauthorized persons
4. Other possible unsafe conditions as noted in the operating manual.
Operator Warnings and Instructions
- The operator shall ensure the operation of the machine
is in compliance with the following:
1.
Guarding system
- Guarding shall be installed and positioned, and access gates or
openings shall be secured per the manufacturer’s instructions (If applicable).
2.
Distribution of load
- The load and its distribution on the platform shall be in accordance
with the manufacturer’s rated capacity for that specific configuration.
3.
Maintaining overhead clearance
- The operator shall ensure that adequate clearance is
maintained from overhead obstructions and energized electrical conductors and parts.
4.
Point of Operation
- The operator shall not place any part of their body under the platform.
5.
Precaution for moving equipment
- When other moving equipment or vehicles are
present, special precautions shall be taken to comply with the safety standards established
for the workplace.
6.
Reporting problems or malfunctions
- The operator shall immediately report to a
supervisor any problem(s) or malfunction(s) that become evident during operation. The
operator shall ensure all problems and malfunctions that affect the safety of operations are
repaired prior to continued use.
7.
Capacity limitation
- Rated capacity shall not be exceeded when loads are transferred to
the load enclosure.
8.
Work area
- The operator shall ensure the area surrounding the machine is clear of
personnel and equipment before lowering the load enclosure.
9.
Securing the machine
- The operator shall comply with the means and procedures
provided to protect against use by an unauthorized person(s).
Summary of Contents for PowerStak PPS2200-101AS
Page 23: ...23 Presto Lifts PPS2200 101AS 125AS 150AS Manual 12 Carriage Assembly...
Page 24: ...24 Presto Lifts PPS2200 101AS 125AS 150AS Manual 13 Mast Assembly...
Page 27: ...27 Presto Lifts PPS2200 101AS 125AS 150AS Manual 16 Hydraulic Schematic...
Page 29: ...29 Presto Lifts PPS2200 101AS 125AS 150AS Manual 18 Electrical Schematic...