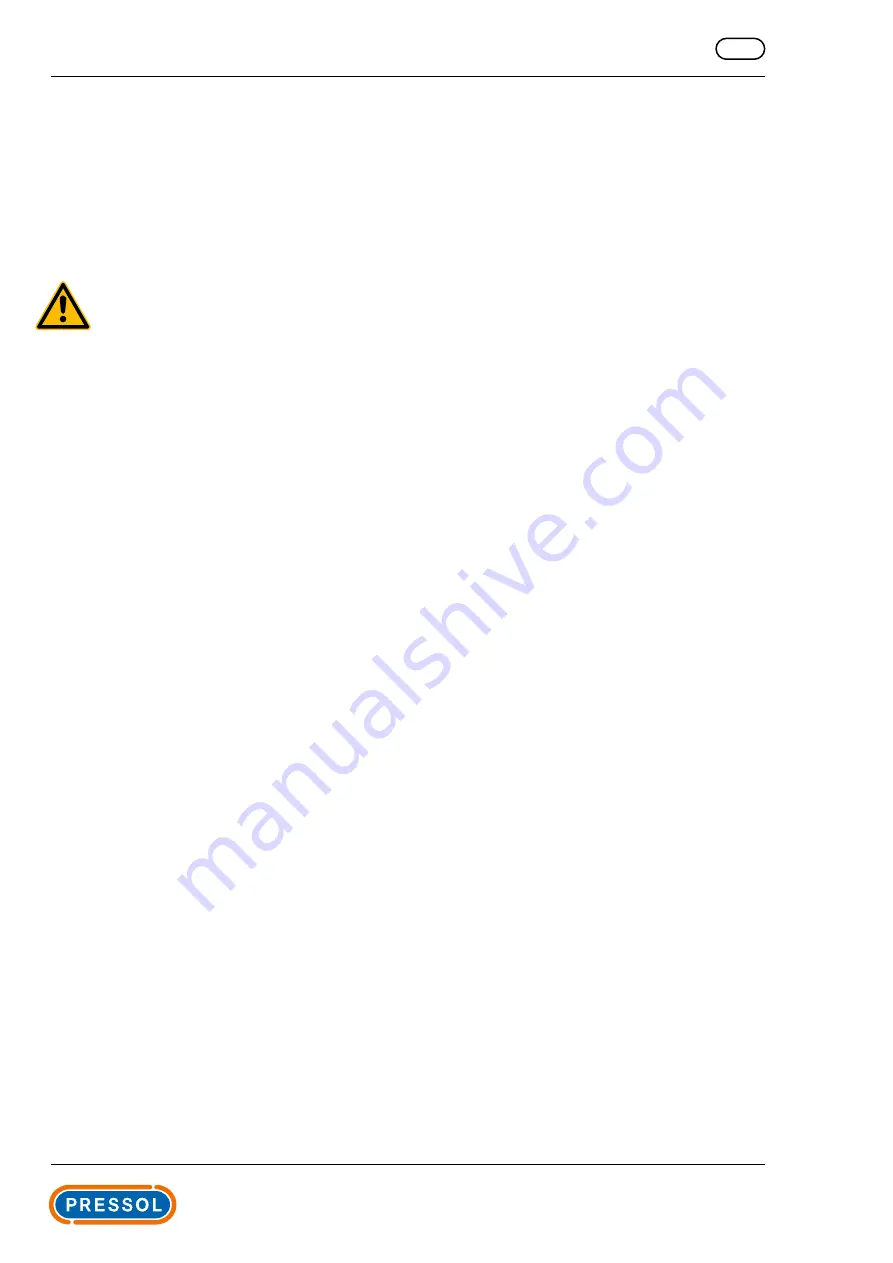
21
center. You must empty the internal circuits from the product first and wash and treat them.
CAUTION: Pumps containing aluminium parts or components coming into contact with the product
cannot be used to pump III-trichloroethane, methylene chloride or solvents based on other halogena-
ted hydrocarbons: DANGER OF AN EXPLOSION CAUSED BY A CHEMICAL REACTION.
CAUTION: The pumps cannot pump Acetylene, Hydrogen, Carbon disulfide.
CAUTION: The components of the pneumatic exchanger, including the shaft are made from materials
that are not specifically resistant to chemical products. If the diaphragm should break, replace these
elements completely if they have come into contact with the product.
CAUTION: The air-driven motor of the pump is self-lubricating and will not require any greasing. There-
fore avoid using lubricated and non-dried air.
WARNING:
• Ascertain that no anomalous noise appears during service. If it is the case, stop the pump immedi-
ately. WARNING: ascertain that the fluid at the delivery side does not contain gas. Otherwise stop the
pump immediately.
• The Diaphragm (in contact with the product or the external ones) are highly subject to wear. Their
duration is strongly affected by the conditions of use and by chemical and physical stress. Fields tests
carried out on thousands of pumps with a head value from 0° to 18° C have shown that normal service
life exceeds one hundred million cycles. However, in places at risk of explosion, the diaphragm must be
disassembled and checked every 5 million cycles and replaced every 20 million cycles.
• Periodic controls must be performed to ensure that there is no powder and/or deposits on the exter-
nal and internal surfaces of the pump and, if necessary, they must be cleaned with a damp cloth.
• Removal of the silencer and the air supply fitting must be done when free from powder. Before rest-
arting the pump, ensure that no powder has entered the pneumatic distributor.
• Always protect the site and the persons operating it from accidental failure by installing a protection
guard to hold and collect any product leakage. Danger of serious injuries and damage to health and/or
objects.
Only use original spare parts to replace worn parts.
Failure to comply with the above may give rise to risks for the operator, the technicians, the
persons, the pump and/or the environment that cannot be ascribed to the manufacturer.
However five general elements are important:
A- all operations must be carried out by skilled personnel or monitored by qualified personnel as ap-
propriate to the specific case
B- put in place all necessary safety measures for personnel (when the pump is installed in places
frequented more than occasionally) against splashes of leaking fluid due to accidental breakage and
always during the conveying of possible fluid leakage towards collection tanks
C- wear acid-resistant clothing and protection whenever operating on the pump
D- make sure that the Intake and delivery valves are correctly closed during the disassembly
E- make sure that there is no power supply to the pneumatic circuit during the disassembly
Please note that it is very important to assemble systems with well-arranged, clearly identifiable and
suitably equipped pipes with shut-off valves and compartments and passages which allow operators
who must carry out inspections to confortably and effectively do so (as the pressure developed by the
pump might cause failures to the system if its construction is defective or worn).
Operating Instructions Diaphragm Pumps
GB