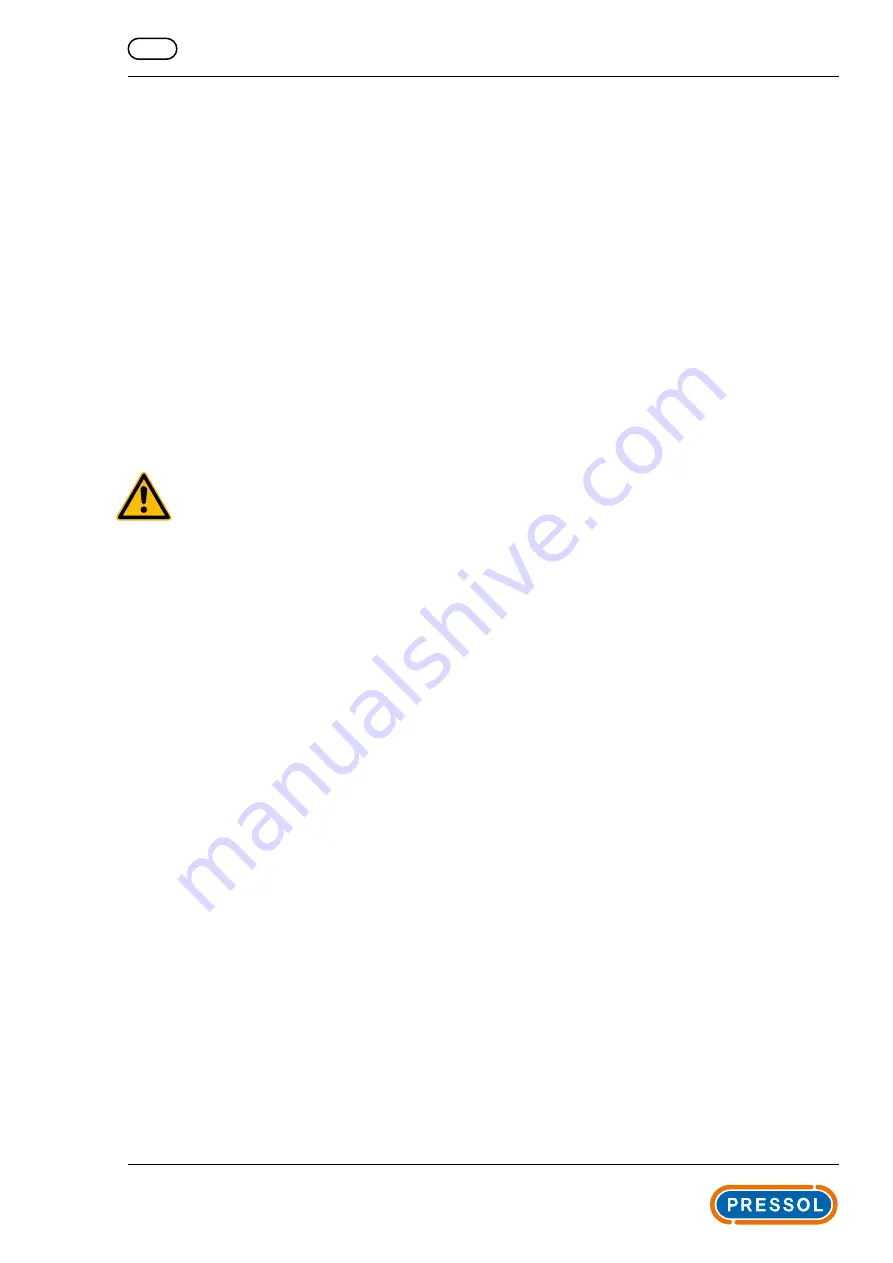
16
• Ensure drainage of fluids which may come out of the pump.
• Fasten the pump using all the available locking holes, the support points must be levelled.
• Arrange for enough room around the pump for the movements of an operator.
• Arrange for free space above the pump for lifting it.
• Inform about the presence of aggressive fluids with suitable colored labels in accordance with the
related standard.
• Do not install the pump (built with thermoplastic material) near heat sources.
• Do not install the pump in places with risk of falling objects or fluids.
• Do not install the pump close to fixed workplaces or visited areas.
• Install additional protection shield, for the pump or for the persons as appropriate. If the diaphragm
breaks the fluid may enter into the pneumatic circuit and come out from the pump discharge port.
• Install a spare equivalent pump connected in parallel.
• The pump must always be electrically earthed.
• If the pump is made from conductive materials and is suitable for flammable products, each pump
casing must be equipped with a suitable ear thing cable: DANGER OF EXPLOSION AND/OR FIRE.
WARNING:
• The pumps must always be grounded irrespective of any other body to which it is connected. Lack of
grounding or incorrect grounding will void the safety requiremenents and protection against the
risk of explosion.
• The pump during operation is under PRESSURE, check appropriately for hazardous conditions.
6.4 START UP
• Check the correct execution of what is indicated in the INSTALLATION paragraph.
• Check that the intake and delivery pipes of the hydraulic circuit are correctly connected.
• Open the intake and delivery valves of the pump hydraulic pump circuit.
• Open the 3-way valve of the air circuit.
• Set the requested operation point requested for the pump: properly adjust the air pressure delivery
rate, with which the pump is supplied. With pressure values under 2 bar the pump may stall, with
pressure values above 7 bar it is possible that breakdowns and/or yields may occur with consequent
spillage of the pumped fluid.
• For pumps with split manifold, the two pumped fluids must have the same viscosity value, very
different viscosity values may lead to stall problems and/or Diaphragm breaking.
• Check that there are no anomalous vibrations or noise due to a too elastic support structure, unsui
table fastening or cavitation.
• Stop the pump correctly after 2 hours of operation and check the tightening of all the bolts on the
pump.
GB
Operating Instructions Diaphragm Pumps