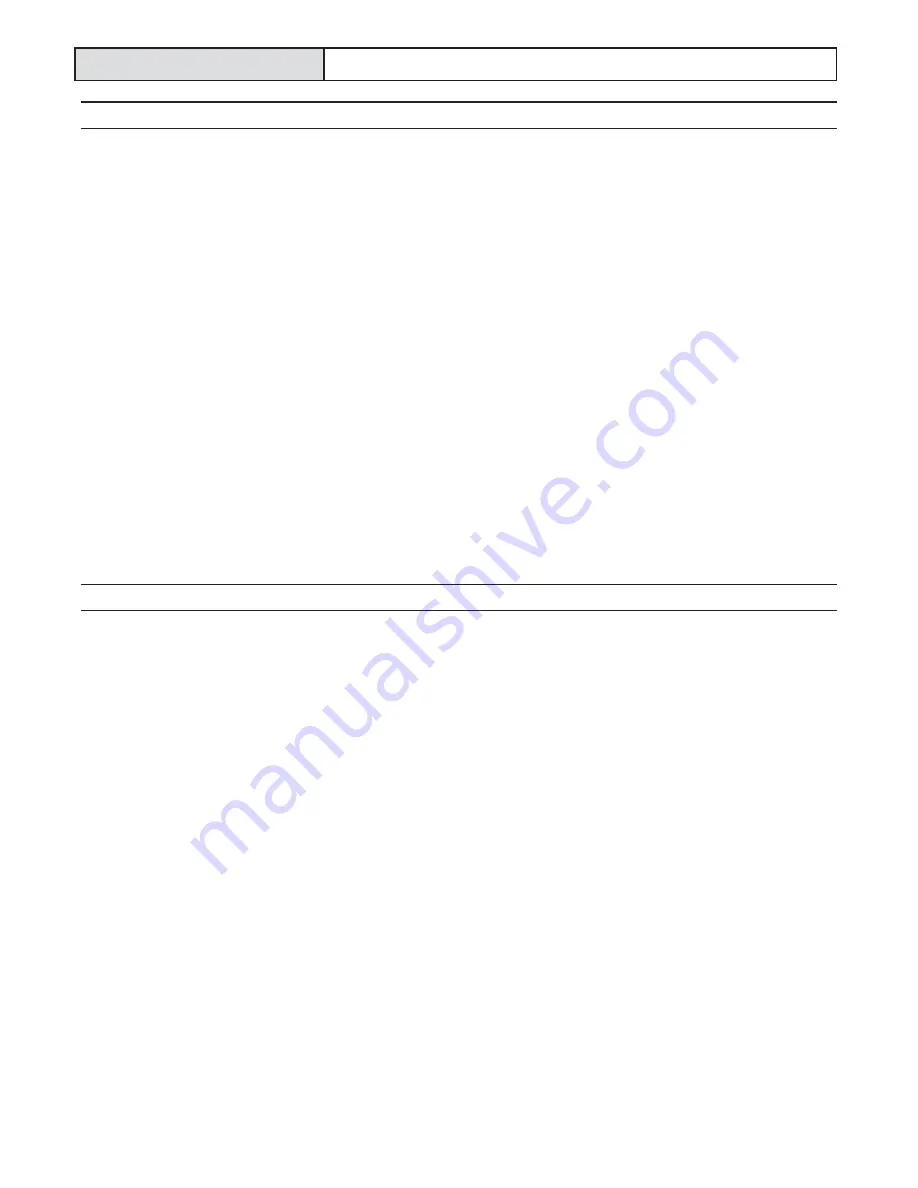
STI-2807 | STI-2817LP
Operating Manual
34
9.11
Importance of Concrete Densifiers
Whether an unsealed concrete surface is polished or unpolished, that surface will deteriorate
if a densifier is not used. Concrete densifiers offer protection to a concrete floor by a chemical
process in which the densifier reacts with the Calcium Hydroxide (Free Lime) present in all
cured concrete.
During hydration, the process by which cement dries, the compound Calcium Hydroxide is
formed. This compound is a weak by-product of hydration and contributes nothing to the
abrasion resistance or overall strength of the concrete. This weak material can be very easily
abraded from the surface of the concrete which leads to small voids as the particles are
pulled out.
Over time, these voids collapse which make them larger and lead to dulling of the concrete
surface or in extreme cases de-lamination. The chemical densifier fills the voids with crystal
growth created by its reaction with the Calcium Hydroxide and essentially ‘glues’ the cement
particles together.
The result is a surface that exhibits increased abrasion resistance which prevents dusting,
de-lamination or loss of shine if polished. We think it’s important to mention densifiers
here, because if a densifier is omitted from a polishing process, that surface will NOT be
permanent.
9.12
Choosing the Right Diamond Tool for the Application
Using the correct diamond tooling for a specific application is the most important part of
ensuring productivity and an acceptable cost per square foot (lifespan) for the specific tool.
With that said, predicting which tool to use is probably the most difficult thing to do because
concrete surfaces are so variable from one pour to the next and depending on the surface
strength or the strength and composition of topical materials (thin-set, patch, adhesive, etc.)
the variation from one material to the next can cause the diamond tooling to be affected in
any number of ways.
Thin-Set covered concrete: 10S Diamond – 16 Grit
•
Patch covered concrete: 10S Diamond – 16 or 30 Grit depending on hardness
•
Adhesive covered concrete: 3SEG – 16/20 or 30/40 Grit
•
Epoxy Coatings (un-sanded): 3SEG – 16/20 or 30/40
•
Sanded Epoxy Coatings: 10S Diamond – 16 or 30 Grit depending on finish desired
•
Hard Concrete: 10S Diamond – 30 Grit with the use of water
•
Note: There are many different conditions that will be encountered when preparing a
concrete slab, the above is a general list of those conditions. There is no substitute for
experience and observation when it comes to determining exactly which diamond design will
work in a given application.