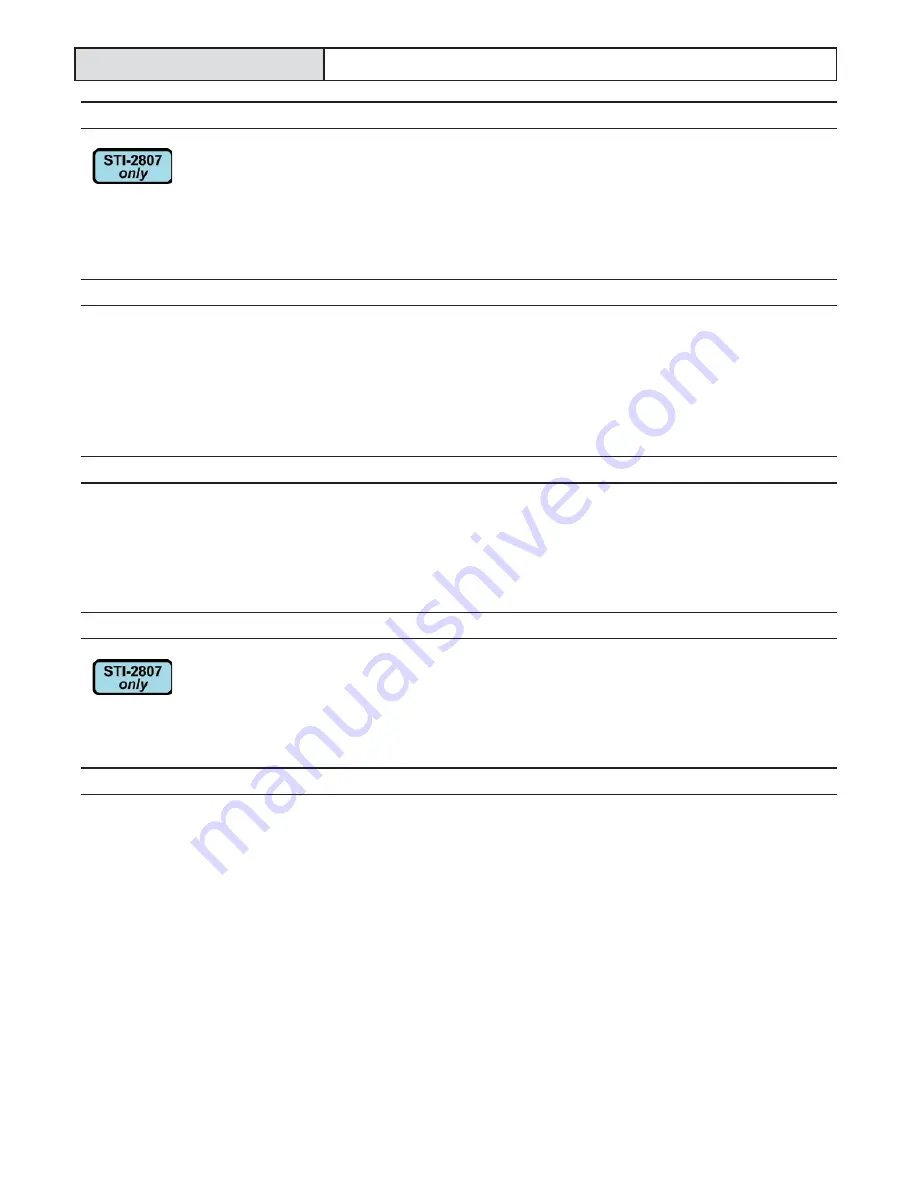
STI-2807 | STI-2817LP
Operating Manual
18
3.8 Electric
Motor
The power plant of the Prep/Master
®
STI-2807 grinder is the electric motor. The
motor is responsible for turning the gears which turn the abrasive tools on the
floor. The motor is controlled exclusively by the Variable Speed Drive which inputs
specific power to generate a given RPM.
3.9 Cutting
Area
The area inside the stainless steel shroud and directly beneath the gear deck is the cutting
area. This is the area in which the tools turn to produce the grinding action. It is also the area
that keeps the dust from grinding contained and subsequently evacuated through the dust
collection ports.
3.10
Couplers & Tool Plates / Stone Holders
The grinder is outfitted with couplers and tool plates OR stone holders. The couplers attach
to the tool plates and provide flex for smooth operation of the diamond tools. The tool plate/
stone holder holds the tools in place for the grinding application.
3.11
Variable Speed Drive
The variable speed drive is responsible for monitoring incoming power as well as
changing the electronic frequency to allow the motor to run at different speeds.
This unit is a closed panel that is intended to be operated only with the keypad.
3.12 Tool
Change
In order to change the tools, the operator must first ensure that the grinder is switched off
and disconnected from the electrical source. The operator should then place all the saddle
weights provided in the weight holders on either side of the variable speed drive.* Then push
machine down by the handle in a controlled manner until the grinder is resting on the top
casters. The operator then loosens the attachment hardware holding the abrasive tools in
place and re-installs with preferred abrasive tool.
* Machine must only be tilted back on firm, level surface. There is danger of machine falling if
all weights are not used and surface is not level.