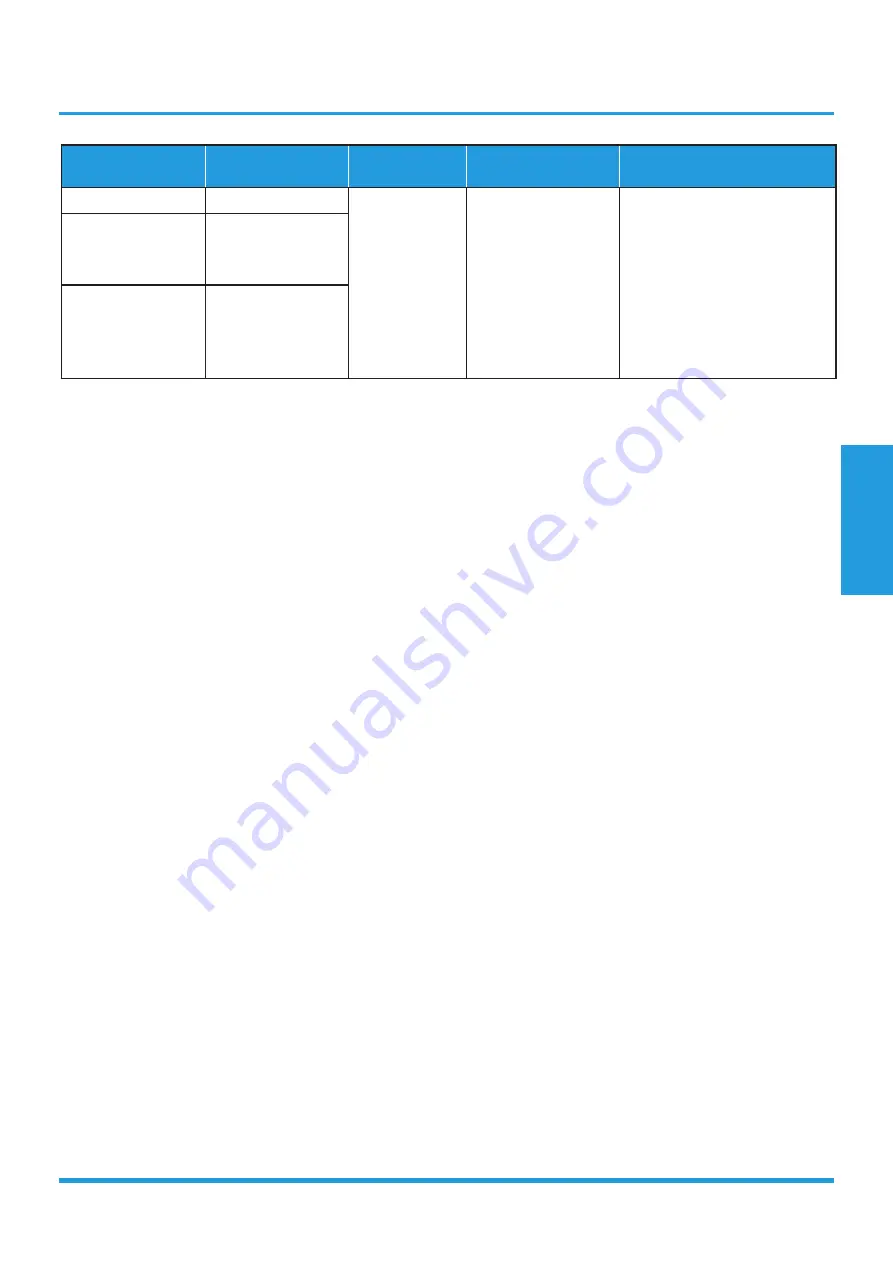
Pr
oduct Featur
es
Page 11
Displayed code
Explanation
Displayed
value
Meaning
Additional Notes
T1
Room temperature
-14—70
-14—70
1. All displayed temperatures
use actual values.
2. All temperatures are
displayed in °C regardless
of remote used.
3. If the actual value exceeds
the range, it will display
the maximum value or
minimum value.
T2
Indoor coil
temperature
T3
Outdoor coil
temperature