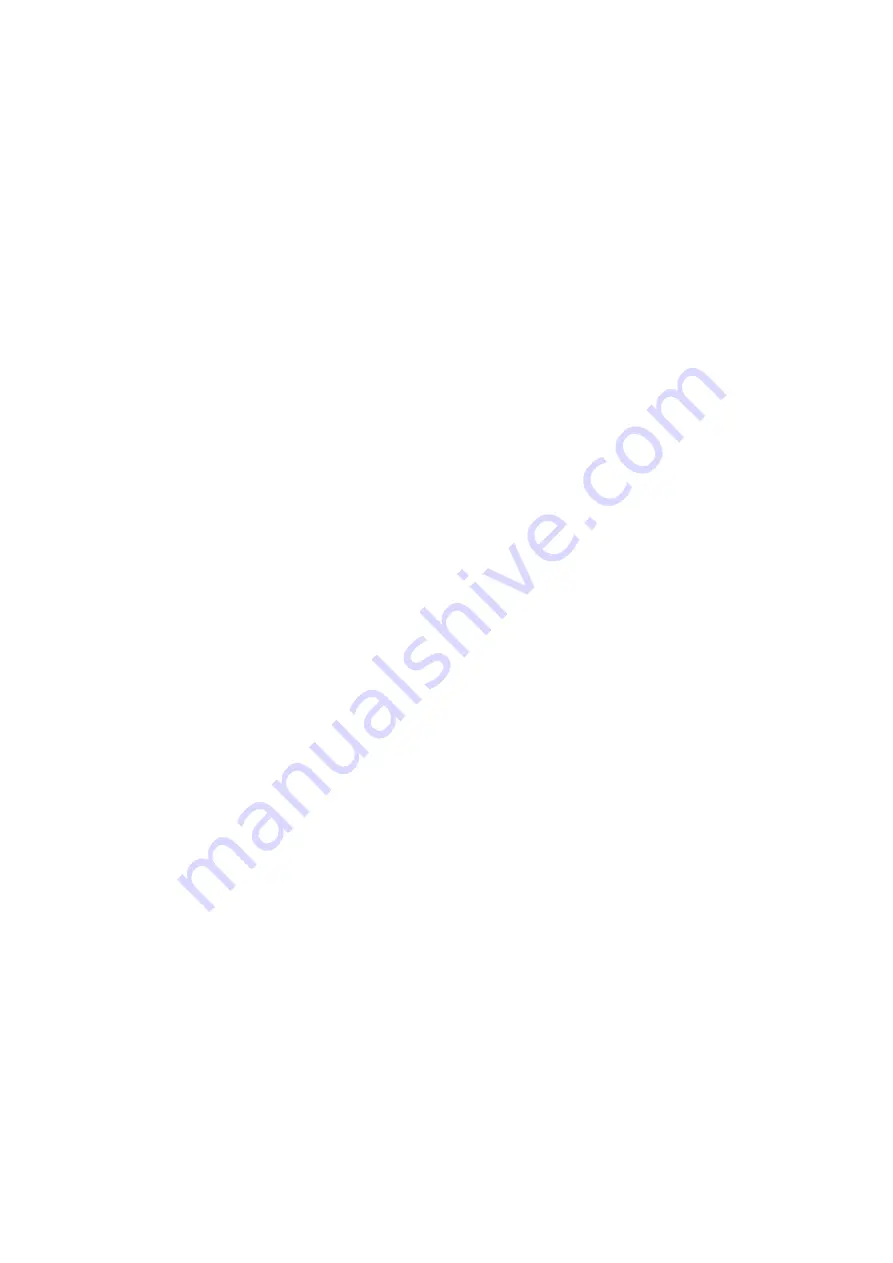
22
Check tracks for correct tensioning and damage.
Check condition of cutters. Make sure that all cutter retaining bolts are tight and that there is
no debris that may break loose when the cutter is started.
Make sure wheel is tight, there is no wobble and it turns freely.
Check and clean air filter and remove any debris from within the engine covers .
Apply
one
pump of grease to the hub at the grease point at the centre of the wheel
(per
week of use)
25 HOUR FIRST SERVICE (To be repeated every 25 hours)
Perform all the daily checks.
Check pulley alignment.
Check exhaust bolts are tight
Check engine mounts making sure nuts are tight.
Check round machine make sure nothing is working loose.
Check tracks for correct tensioning and damage.
Refer to engine manual for cleaning of air cooling system.
Check and adjust if necessary belt tightness from layshaft to cutter head.
50 HOUR FIRST SERVICE.
Repeat 25 hour service.
Change engine oil and filter
Change fuel filters
Change hydraulic oil and filter
Check fuel pipes and clamp bands.
100 HOUR FIRST SERVICE.
Repeat standard 50 hour service. (inc 25 hour service)
Check battery electrolyte level-Refer to COSHH safe batteries – supplied.
Change oil in track drive gearbox.
Grease undercarriage widening pins and slides.
EVERY 100 HOUR STANDARD SERVICE.
(To be repeated every 100 hours of use.)
50 Hour standard service. (inc 25 hour service).
Check battery electrolyte level-Refer to COSHH safe batteries – supplied.
Grease undercarriage widening pins and slides.