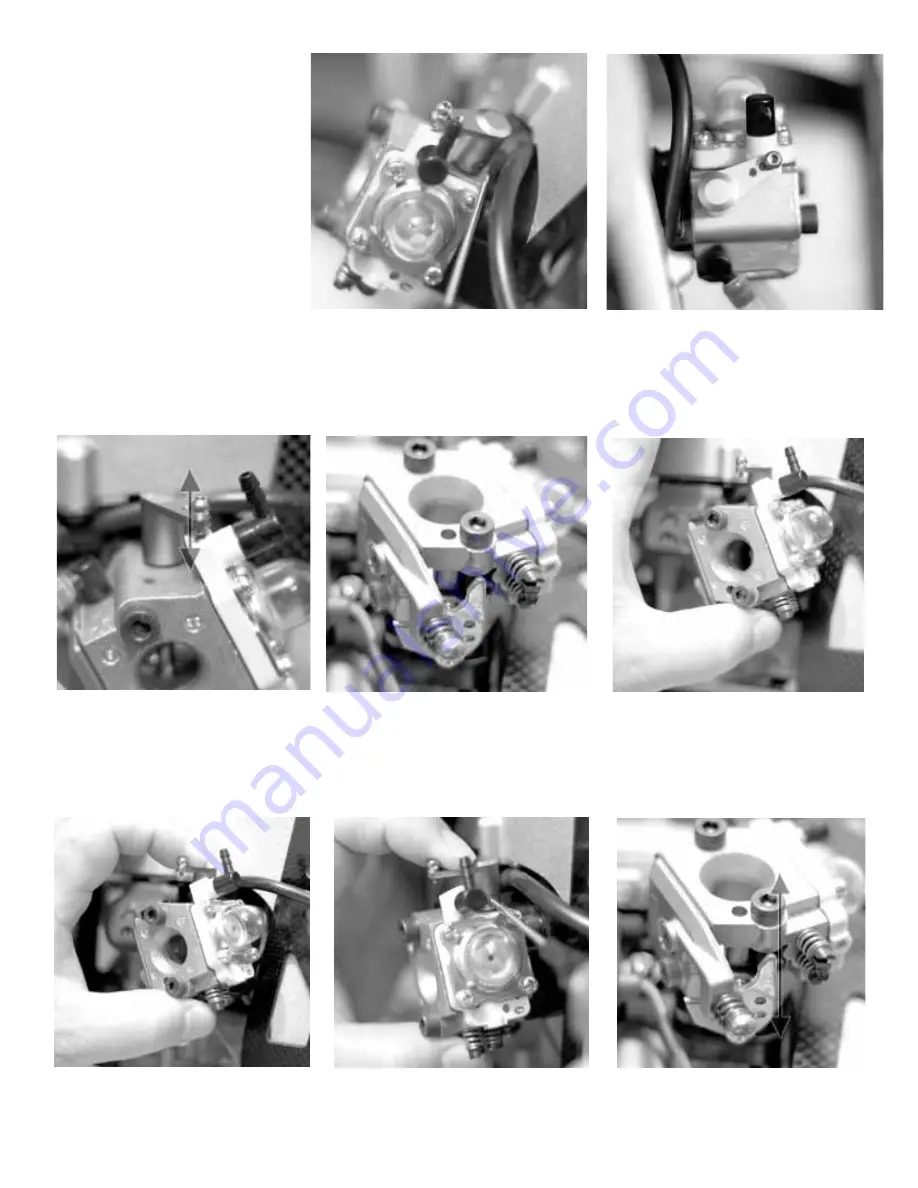
25
In the closed position it will be difficult
to reach the set screw for the throttle arm.
You should follow these guidelines for
optimal throttle performance in the Preda-
tor Gasser.
The ball for the throttle lever must be
placed in the furthest hole from the center
for best deflection.
Set the throttle to the full closed posi-
tion.The control ball on the throttle arm
should be aligned as pictured aligned
with the brass ball in the bulb plate.
This is the throttle control pointer plate.
When the set screw is tightned, the throttle
arm moves this plate.
Grab the throttle pointer and move it
with your thumb until exposing the set
screw. Prepare your index finger to hold
the position of the throttle arm.
After exposing the set screw carefully
hold the position of the throttle pointer
and arm in order to tighten the set
screw.
Try testing the method of positioning the
arm. Tighten set screw with locktite only
when position is final.
The halfway point on the throttle is found
by aligning the flat long end of the throttle
pointer with the bolt as shown.
Optimal Throttle Arm Positioning.
Following is a method of achieving
maximum deflection range in the
throttle control. This is the recom-
mended setup to get top performance
out of your gas powered Predator.