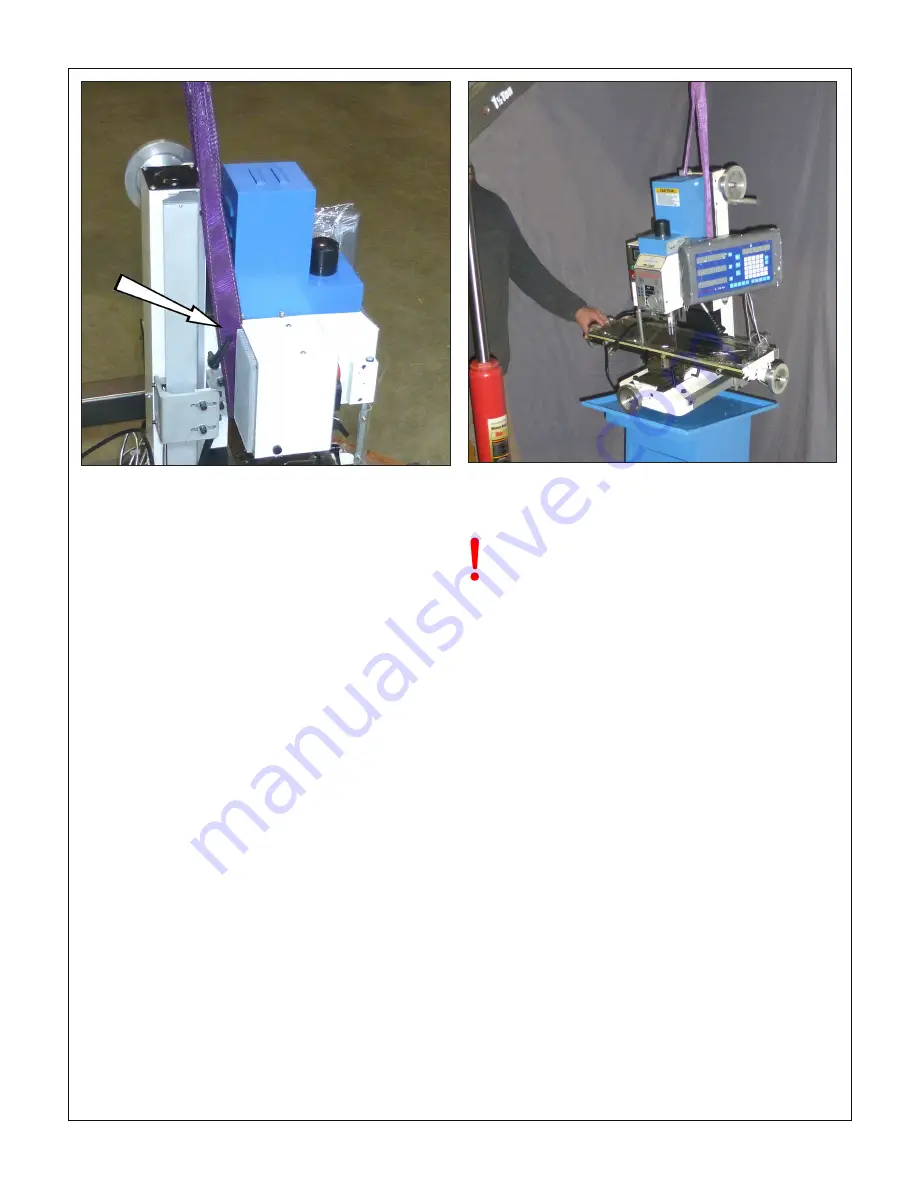
4
PM-30MV v3 2020-10
Copyright © 2020 Quality Machine Tools, LLC
Figure 1-2
Sling position
Figure 1-3
Lowering the mill into position
Assembly and cleanup
Unfinished metal surfaces
may be protected in shipping by
thick grease and/or paper. Carefully remove these using a
plastic paint scraper, disposable rags and a light-oil such as
WD-40. Coat bright machined surfaces with a rust preventa-
tive such as Rustlick.
Level the mill using the table surface for reference, shimming
under the tray if necessary. Oil the ways and leadscrews (Z-ax-
is screw excepted, inaccessible).
Initial checks
Read Section 3 if unsure about any item in the following
1. Check that: A There is no chuck or collet is installed; B
There are no clamps or locks on moving parts, and; C The
speed control knob is at its
lowest setting
, fully count-
er-clockwise.
2. Remove the blue motor cover. Make sure the belt is set
for low speed (belt running on the larger spindle pulley.)
If not, re-position the belt, Figure 3-2. Replace the motor
cover.
3. Connect 220 Vac power.
4. Be sure the E-Stop (Emergency) button has not been
pushed in (it should pop out when twisted firmly clock
-
wise).
5. Press the Power button. The power lamp and the tach
display should light.
6. Check the emergency function by pressing the E-Stop
button. The power lamp should go out, de-energizing the
contactor circuit, disabling all electrics.
If this doesn’t
happen, the E-stop function is defective, and needs
attention.
7. Restore power by twisting the E-Stop button
firmly
to the
right; this will cause it to pop out.
8. Check that the chip guard switch disconnects power when
the guard is swung out.
DO NOT LEAVE THE MACHINE UNATTENDED
DURING THIS PROCEDURE
Test run procedure
1. Select Forward (F) spindle direction. The tachometer
should display between 50 and 100 rpm.
2. Rotate the speed potentiometer cw for a speed of about
200 rpm. Run the spindle at that speed for about 1 min-
ute, then progressively increase the speed to the max
(about 1500 rpm), pausing for about 1 minute at each
200 rpm increment.
3. Repeat step (2) with the spindle reversed (R).
4. Set the belt for high speed, then repeat steps (2) and (3).
The machine should now be ready for normal operations.