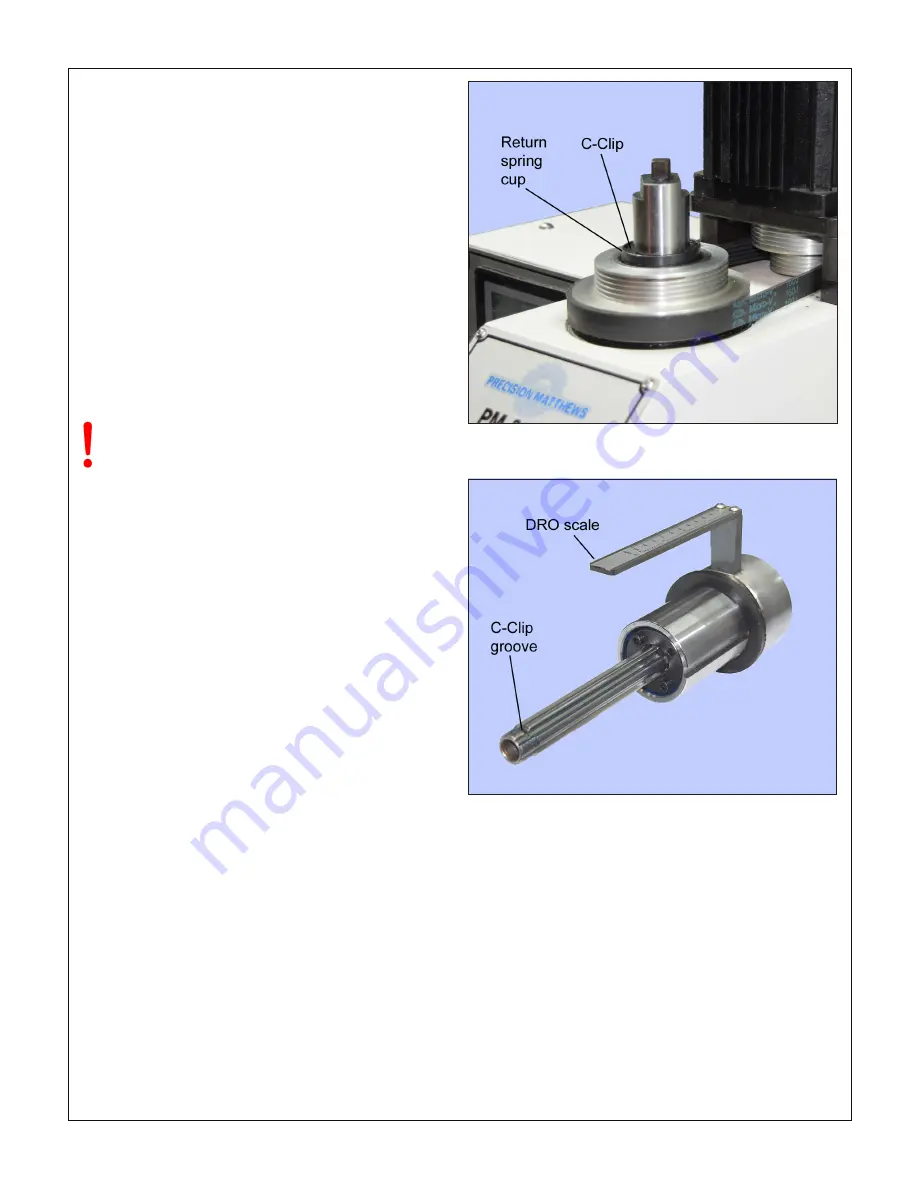
18
PM 25MV v9 2020-10
Copyright © 2020 Quality Machine Tools, LLC
SERVICING QUILL & SPINDLE
In the normal use the quill assembly needs only oiling
on its sliding surface. The spindle runs on pre-lubricated
roller bearings and needs little attention, see Spindle
Bearings, above. If the bearings need to be serviced or
replaced, remove the quill/spindle assembly as follows:
1. Remove any installed R8 device from the spindle.
2. Lock the spindle with the C-wrench, then unscrew
the drawbar cap (17 mm flats) from the spindle.
3. Remove the drawbar.
4.
IMPORTANT:
Use wood blocks or other means to
prevent
unexpected downward movement
of the
quill assembly.
5. Press down on the return spring cup while removing
the C-Clip, Figure 4-6.
6. Remove the return spring, Figure 4-5.
7. Using a 2.5 mm hex key remove the two button head
screws securing the DRO scale and stand-off block
to the quill assembly.
8. Remove the wood blocks (4), then remove the quill
assembly from the headstock.
Figure 4-6
Remove drawbar cap for access to the C-Clip
Figure 4-7
Complete DRO scale and quill assembly
For illustration only: for servicing operations the scale should
be detached from the quill and should remain in the DRO
case.
SPINDLE BEARINGS
The spindle runs on grease-lubricated tapered roller
bearings. These should be serviced every 500 hours of
running time. Thoroughly clean each bearing assembly
then repack with a grease such as Kluber Isoflex (auto
shop wheel bearing grease can be used in low-load, low
rpm operations).
Do not over-pack the roller bearings!
Bearing manufacturers recommend that the free volume
between inner and outer should be no more than 30%
filled with grease. (If smothered with grease, bearings
are subject to overheating.)
Especially during the first 10 hours of running time
check that the spindle runs smoothly, without ex-
cessive heat build up (the spindle will run warm
when used at high speeds over long periods, but
should not be uncomfortably hot). Overheating can
be due to excessive grease, see above, or an over-
tight spanner nut at the upper end of the spindle.
Call Precision Matthews for guidance.