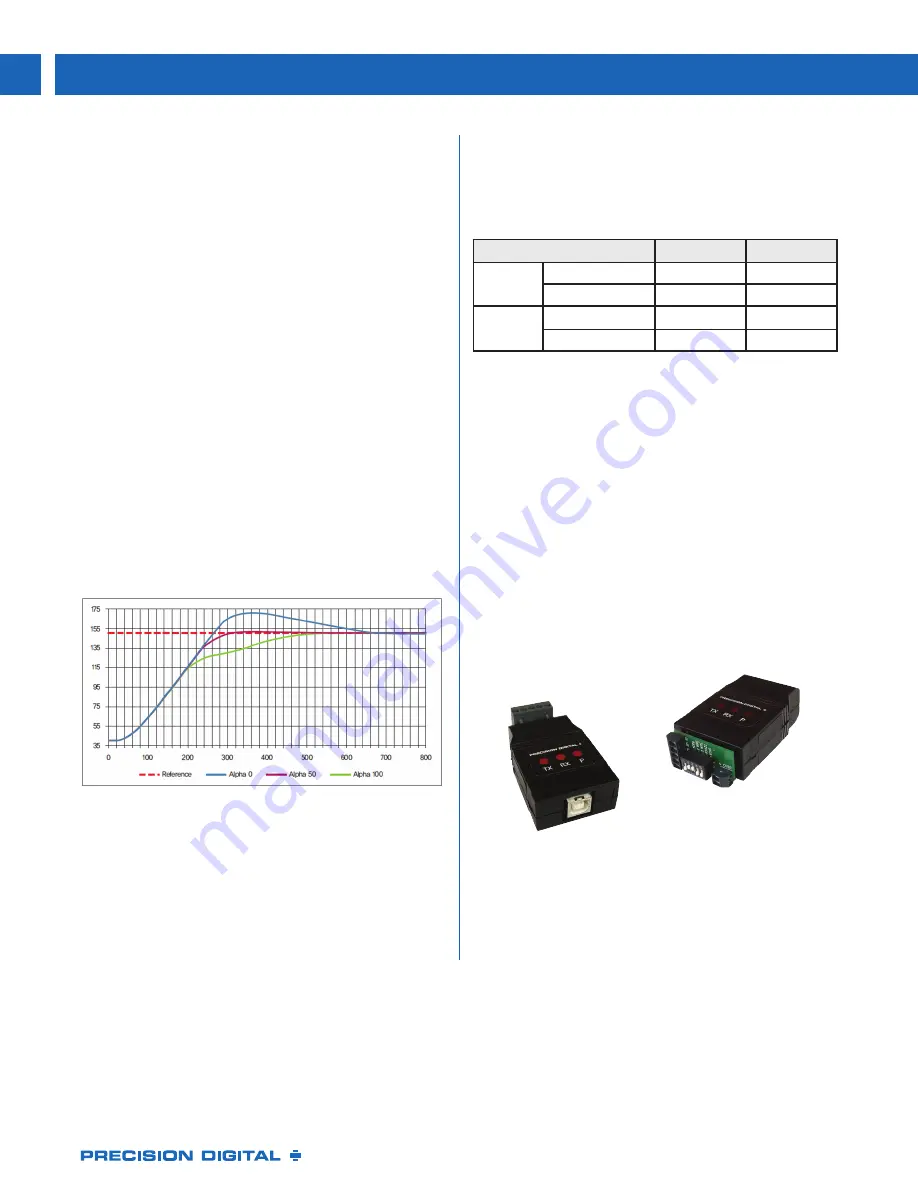
PD500
SuperNova PID Process & Temperature Controllers
www.predig.com
6
Digital Input Set Point Selection
Two digital inputs can be added as an optional feature. Digital
inputs are active with dry contacts or low logic levels. The
configuration of the two inputs can select which set point to
use (SV1, SV4, or remote) and select run and stop modes.
Function
DI 1
DI 2
R/S
STOP
0
-
RUN
1
-
SV
SV1
-
0
SV4 or REM
-
1
Normally open switches (external excitation not required) or
open collector transistor contacts may be used to operate the
digital inputs.
Serial Communications & Adapters
SuperNova controllers with the serial communications option
include RS-485 serial communications for Modbus.
The SuperNova Controllers are Modbus server (slave)
devices. Process control information can be read from the
units, and setting parameters can be read or written to the
controllers.
The PDA7485 RS-232 to RS-485 and PDA8485 USB to
RS-485 converters are available for use with the SuperNova
TCS software or other PC applications. They are especially
useful with Modbus communications packages, so multiple
controllers on the RS-485 bus may be accessed by computers
without RS-485 communications ability.
PDA7485
PDA8485
Analog Retransmit Output
An optional 4-20 mA retransmitting output is available on all
sizes of SuperNova Controllers.
This is especially useful when using a temperature input,
to provide a 4-20 mA signal to the control room or other
equipment.
•
•
4-20 mA Retransmitting Output
•
•
Retransmit Based on PV, SV, or MV
Auto-Tuning PID
A high accuracy auto-tuning function calculates the PID
values for your system with the push of a button, eliminating
the need for complex PID calculations and time consuming
setup. After several on/off cycles, the PID values will be setup
automatically.
Simple PID Response Adjustment
The Alpha parameter allows for easily adjusting the system
response without the need to change P, I, or D values.
The ALPHA parameter is used to adjust the response
characteristics to the set value (SV) changes.
If ALPHA is set to 0%, it is the same as the normal PID control
response.
If ALPHA is set to 100%, it may take a long time to reach a
normal state, but overshoot and undershoot will be minimized.
Set Value Ramp Up/Down
When the ramp functions are used, the set value (SV)
changes over time to reach a newly selected set value.
When ramp functions are not used, a newly selected
SV immediately becomes the active SV.
This is useful to prevent overshoot and protect
equipment from rapidly changing output values as set
points are changed.