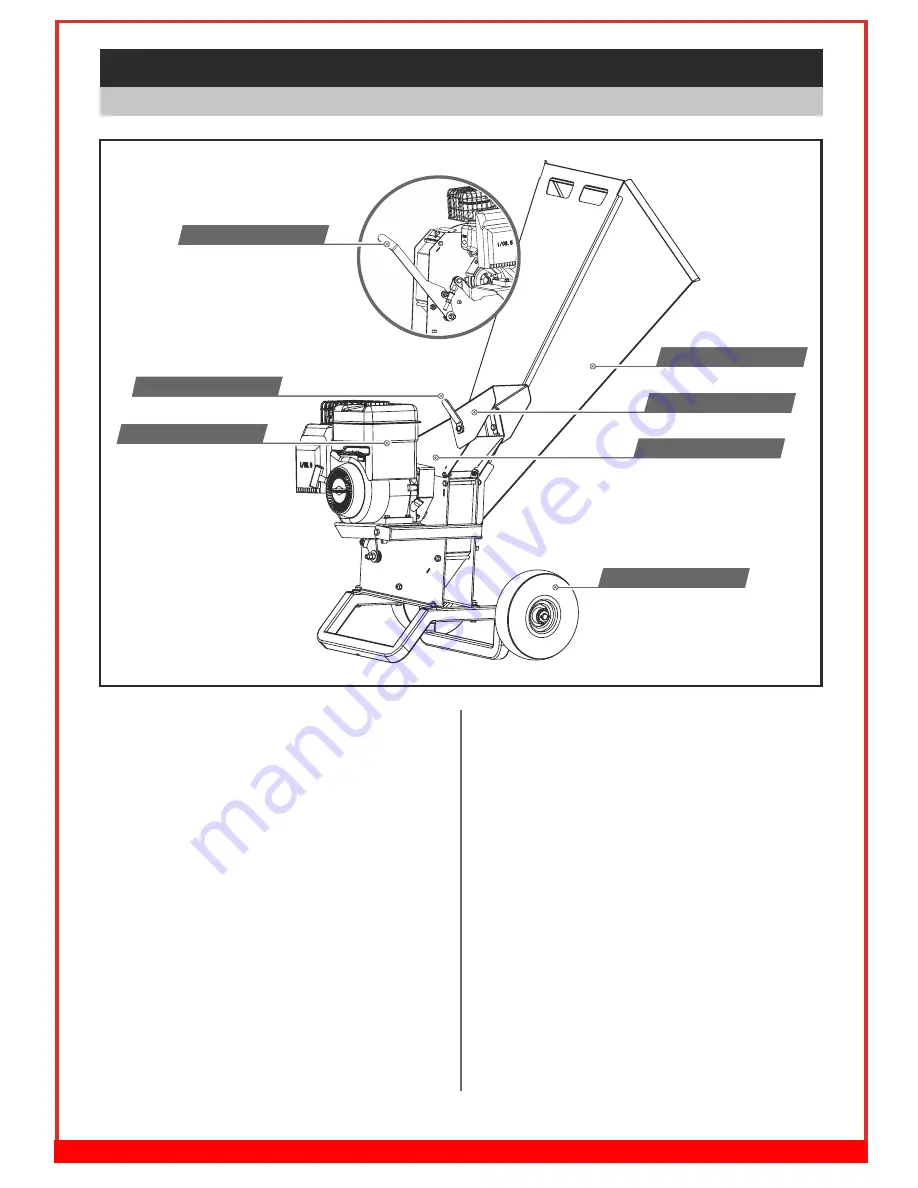
9
Pow’R’kraft Chipper 9
Revision 9/22/16
KNOW YOUR CHIPPER
Features and Controls
Deflector Lever
Deflector
Feed Hopper
Discharge Chute
Transport Wheels
Engine
Fuel Valve Control
The fuel valve opens and closes the passage
between the fuel tank and the carburetor. The
fuel valve lever must be in the ON position
for the engine to run. When the engine is not
in use, leave the fuel valve lever in the OFF
position to prevent carburetor flooding and to
reduce the possibility of fuel leakage.
Throttle Control
The throttle lever controls engine speed.
Moving the throttle lever makes the engine
run faster or slower.
Engine Switch
The engine switch enables and disables the
ignition system. The engine switch must be in
the ON position for the engine to run. Turning
the engine switch to the OFF position stops
the engine.
Choke Lever
The choke lever opens and closes the choke valve
in the carburetor. The closed position enriches the
fuel mixture for starting a cold engine.
The open position provides the correct fuel
mixturefor operation after starting, and for
restarting a warm engine.
Recoil Starter Grip
Pulling the starter grip operates the recoil
starterto crank the engine.
Feed Hopper
It is the opening into which all materials to be
chipped should be fed.
Belt Tension Lever