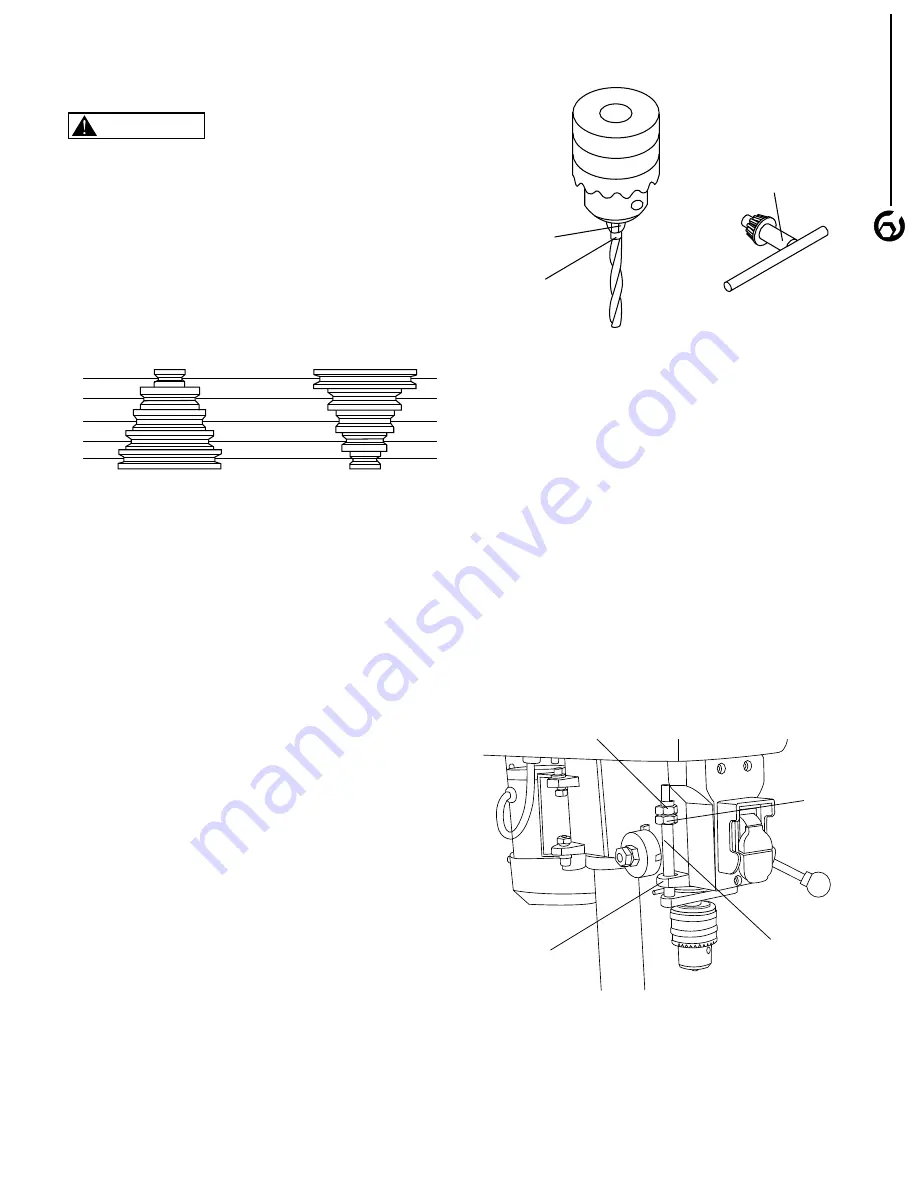
ADJUST SPEEDS
Refer to Figure 13
Turn the switch to “OFF” position and disconnect the
machine from power source.
This drill press has 5 speeds: 620 RPM,
1000RPM, 1720RPM, 2340RPM and 3100RPM. The
speed is determined by the location of the belt on the
pulleys. The speed chart shows the pulley configuration
for each speed.
INSTALL DRILL BIT
Refer to Figure 14
• Insert the chuck key. Rotate counterclockwise to loosen
the chuck jaws so that the opening is slightly larger than
the bit size you intend to use.
• Insert the smooth end of drill bit all the way into the
chuck. Slightly pull back the drill bit by 1/16”. If the spiral
groove (flute) of drill bit is still inside the chuck, pull
further until the spiral groove is free from chuck
jaws’ grip when tighten.
• Turn chuck key clockwise to tighten the chuck jaws.
Check to see the drill bit is centered and secure in the
chuck.
• Remember to remove chuck key before operating the
machine.
ADJUST DEPTH STOP
Refer to Figure 15
The depth stop is attached to the quill with hex hut that
can be lowered or raised on the stud. To set the depth
stop:
• Lower the drill bit to the desired height by using the
handles.
• Hold the feed handle at the desired position.
• Use wrench to spin the lower lock nut down to contact
the depth stop and lock the nut.
• Spin the upper nut against against the lower stop nut
and tighten.
• The drill bit will stop after traveling the distance on the
depth scale.
7
OPERATION
7
Figure 13
5
4
3
2
1
5-5
4-4
3-3
2-2
1-1
3100
2340
1720
1100
620
5
4
3
2
1
Spindle
Belt
Location RPM
Motor
Figure 14
Chuck Jaws
Drill Bit
Chuck Key
Figure 15
Upper Lock Nut
Depth Stop
Depth Scale
Lower
Lock Nut
WARNING