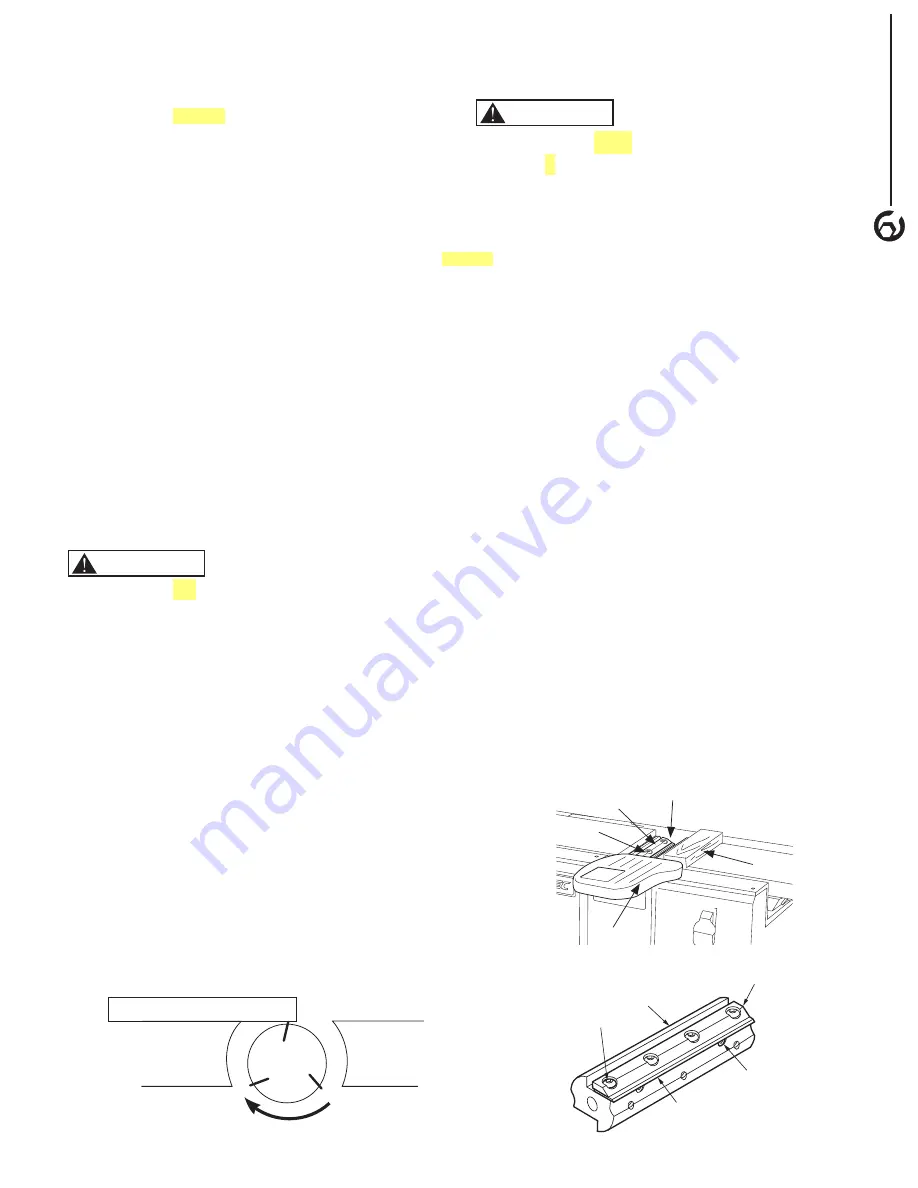
• Push the Limit Block Shaft (3) toward the fence. Place
the Limit plate (1) of the Fence Bracket Assembly into
the Limit Block Rear Slot (2).
• Pull the fence toward perpendicular to the table (90°)
position. The fence will hit and be stopped by Limit
Block Shaft (3). Now tighten the Fence Tilting Handle
(6). The Fence is at 90° position.
To set the inward 45° stop:
• Position the fence on the bed. Place sliding handle (7) in
locked position. Loosen the fence tilting handle (6).
• Pull the top of the fence toward the table. It will hit and
stopped by the inward stop bolt (4). Now tighten the
fence tilting handle (6). The fence is at inward 45°
position.
To set the outward 45° stop:
• Position the fence on the bed. Place sliding handle (7) in
locked position. Loosen the fence tilting handle (6).
• Pull out the limit block shaft (3) so it will not limit outward
movement of the fence.
• Pull the top of the fence outward. It will hit and stopped
by the outward stop bolt (8). Now tighten the fence tilting
handle (6). The fence is at outward 45° position.
CHECK BLADE OUTFEED TABLE
ALIGNMENT
Turn the switch in “OFF” position and disconnect the
jointer from the power source.
Do not touch the blade cutting edge at any time.
The blades have been adjusted in the factory and should
require no adjustment. Nevertheless, the blades can
become out of alignment during shipping and handling.
For accurate cutting, the blades must be at the same level
with the outfeed table.
• To adjust the blades, position a straight edge on the
outfeed table and have it extend over the cutterhead.
• Gently rotate the cutterhead under the straight edge.
The blades should just touch the straight edge by a hair.
The blades may brush the straight edge and pull it
forward slightly (No more than 1/8” on each blade pass).
If a blade does not touch the straight edge at all, it is too
low. If a blade pulls forward the straight edge more than
1/8”, it is too high.
• Check blade height at both ends of the blade to see if it
is level from side to side.
• Check each blade using the same procedure.
ADJUST THE HEIGHT OF THE CUTTERHEAD
BLADES:
Turn the switch to OFF position and diconnect the ma-
chine from power source.
Refer to Figure 12 and 13
• Pull open the blade guard (4) and block it in open
position with a piece of wood (3). Now the cutterhead
(1) is fully exposed.
• Locate the blade lock screws (5) and jack screws (6) on
the cutterhead (1)
• Loosen the four blade lock screws (5) and the two jack
screws (6) with enclosed 4mm hex wrench.
• Use a wood block to push down the blade (7) gently
until the blade edge is slightly below the straightedge
(see Figure 11).
• Turn each jack screw (6) clockwise, 1/8 of a turn at a
time, until the edge of the blade just touches the straight
edge by a hair. Adjust the blade at both ends so they
are even from side to side.
• With the screws are partially loose, gently rotate the
cutterhead (1) under the straight edge. The blades (7)
may brush the straight edge and pull it forward slightly
(No more than 1/8” on each blade pass). If a blade (7)
does not touch the straight edge at all, it is too low. If a
blade pulls forward the straight edge more than 1/8”, it
is too high. Adjust the jack screws until the blade height
is correct at both ends.
• Tighten each blade lock screws (5) and jack screws (6)
firmly.
• Adjust each blade using the same procedure.
• Return the blade guard (4) to its original position.
WARNING
Figure 11 - Cutterhead Alignment Setup
WARNING
Figure 12 - Block Blade Guard
Figure 13 - Cutterhead Illutration
OPERA
TION
7
Outfeed
Table
Infeed
Table
CUTTER HEAD
Straight Edge
1
2
3
4
5
1
2
6
7
5
the "OFF"
the
(remove "toward")
be
to the