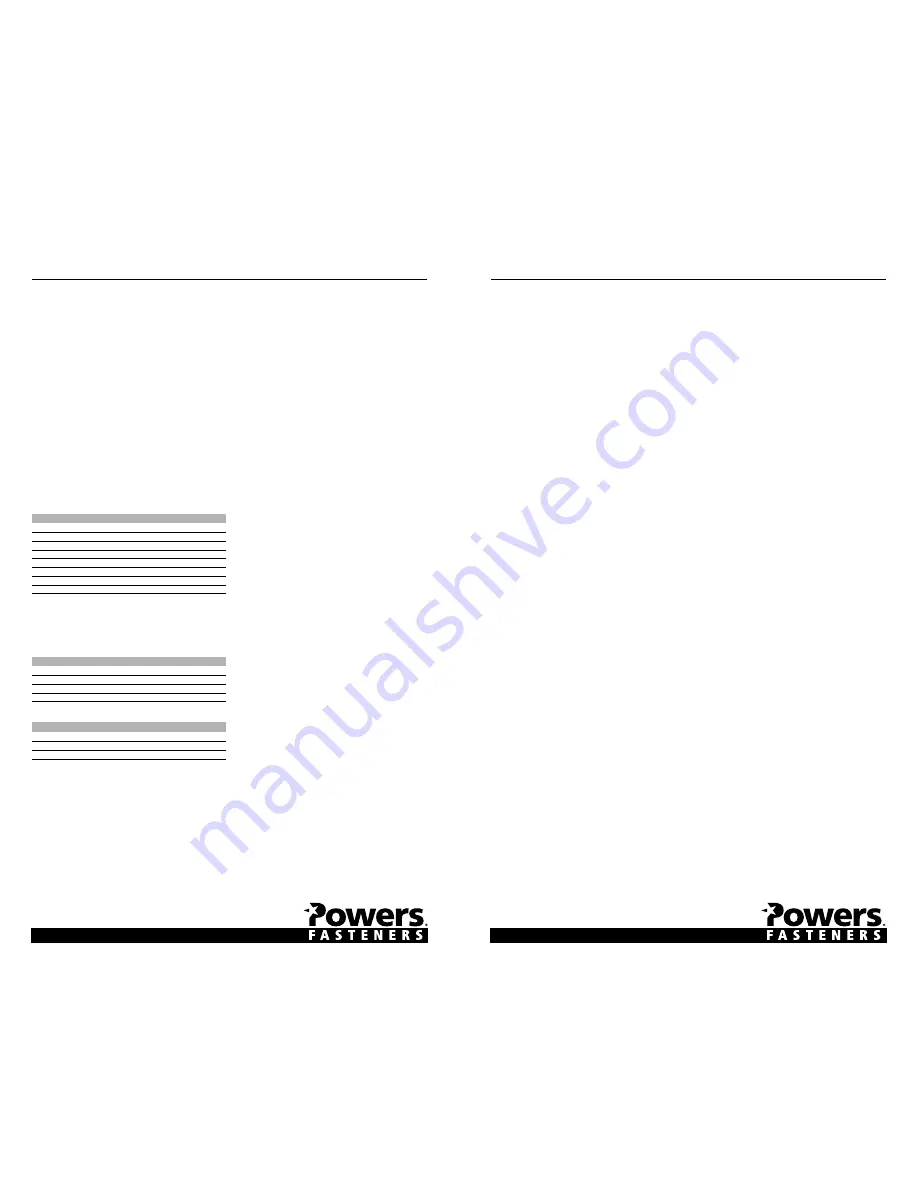
7
PA
351
MODEL
PA351
CAT. NO.
50266/Deluxe Kit
6
PA
351
MODEL
PA351
CAT. NO.
50266/Deluxe Kit
penetration. This will be the minimum fastener shank
length required. Do not select a shank length longer
than that required for the application. An excessively
long shank can burnish or polish the hole created in the
steel resulting in a reduction in load capacity. To
determine the minimum threaded length, add the
thickness of the fixture and the nut / washer thickness.
The nut and washer thickness is equal to the nominal
thread diameter.
Do not over tighten threaded studs, the maximum
tightening torque is listed in the table below. Use of a
nut setter is recommended to reduce the possibility of
over tightening the fasteners. For critical applications,
perform a job site test.
Fastener
Selection Guide
8MM HEAD DIAMETER DRIVE PINS
10 MAGAZINE STRIP
CAT.
STD
STD.
NO.
SHANK LENGTH
BOX
CTN.
50240
5/8" K
500
2500
50242
3/4" K
500
2500
50244
3/4"
500
2500
50246
7/8"
500
2500
50248
1"
500
2500
50250
1-1/4"
500
2500
50252
1-1/2"
500
2500
50254
1-5/8"
500
2500
Powder Load
Selection Guide
.27 CALIBER SAFETY STRIP
®
CAT.
POWER
LOAD
STD.
STD.
MASTER
NO.
LEVEL
COLOR
SIZE
BOX
CTN.
CTN.
50620
2
Brown
.27 strip
100
1000
20000
50622
3
Green
.27 strip
100
1000
20000
50626
4
Yellow
.27 strip
100
1000
20000
50630
5
Red
.27 strip
100
1000
20000
.27 CALIBER SAFETY STRIP
®
MASTER PACK
CAT.
POWER
LOAD
STD.
STD.
MASTER
NO.
LEVEL
COLOR
SIZE
BOX
CTN.
CTN.
50624
3
Green
.27 strip
1000
-
20000
50628
4
Yellow
.27 strip
1000
-
20000
50632
5
Red
.27 strip
1000
-
20000
Safety Precautions
Safety is your primary responsibility when operating any
powder actuated tool. You must read and understand
the contents of this manual. You must be familiar with
all functional and safety requirements of the tool. It is
your responsibility to obtain proper training and a
Powers Fasteners operator card prior to using this tool in
compliance with the current American National Standard
A10.3 Safety Requirements for Powder Actuated
Fastening Systems and the Federal Occupational Safety
and Health Administration Standards (OSHA). Existing
state or local regulations should also be followed. When
using this tool, you must have the qualified operators
card in your possession.
Revocation of card - Failure to comply with any of the
rules and regulations for safe operation of powder
actuated tools shall be cause for the immediate
revocation of your qualified operator card.
The following is a summary of safety precautions to
be followed when operating a Powers Fasteners powder
actuated tool. Failure to follow these safety instructions
can result in serious injury or death to operators
or bystanders.
PRIOR TO OPERATING THE TOOL
1.
Warning signs should always be posted within the area
in which a powder actuated tool is to be used. These
signs should be at least 8" x 10" in size with boldface
type that is not less than 1" in height. The sign should
state “Powder Actuated Tool In Use".
2.
Approved safety goggles should always be worn by
operator or bystander, to protect their eyes from flying
particles. Hearing protection should always be worn by
the operator and bystanders when using a powder
actuated tool. Other personal safety protection as
required should also be used.
3.
Never modify or fabricate parts for use in your Powers
tool. Use only Powers fasteners, loads, and tool parts.
4.
Hands or other body parts must never be placed in front
of muzzle/barrel. Accidental discharge can cause piston
and/or fastener to pass through the operator’s hand.
5.
Never compress the tool against any part of the body.
Serious injury or death may result in the event of an
accidental discharge.
6.
Always point tool in a safe direction at all times.
7.
Use the tool for its intended purpose only.
PREPARATION FOR LOADING THE TOOL
1.
Tools must be checked prior to operating to make sure
they are not fully or partially loaded with a powder
load or fastener.
2.
To insure safe operation, perform the daily function test
described in this manual. Be sure the tool is not loaded
prior to performing this test.
3.
Do not operate this tool unless all its parts are in
place and operating appropriately. Never attempt
to use a malfunctioning tool. Call 1-800-524-3244
for assistance.
4.
Never guess about the suitability of a base material.
If you are uncertain about the suitability of a base
material, perform a center punch test.
5.
Do not operate the tool until you learn and understand
the color code / numbering system used to identify the
power level of powder loads.
OPERATING THE TOOL
1.
Only use fasteners and powder loads designed
for this tool as supplied by Powers Fasteners.
2.
Do not use powder actuated tools in a flammable
or an explosive atmosphere.
3.
Do not fire a tool without a fastener. The piston will
impact the work surface possibly causing serious injury
to the operator or bystanders along with damage to
the tool.
4.
Do not load the tool until you are ready to make a
fastening. Check the power load level before inserting
it into the tool chamber.
5.
Fastener must be loaded prior to loading the powder
load, to prevent injury to operator or bystander in the
event of an accidental discharge.
6.
Do not close tool against work surface. The tool should
be manually closed, with hand away from muzzle/barrel
to prevent accidental discharge.
7.
Hold the tool perpendicular to the work surface at all
times. Use a spall guard wherever possible. This will limit
the possibility of fastener ricochet which could cause
serious injury or death to the operator or bystanders.
8.
Always perform a test fastening with the lightest load
level designed for use in the tool. If the lightest load
fails to set the fastener, try the next highest load until
the proper level is attained. Failure to follow this
procedure may cause the fastener to be overpowered.
If this occurs, the fastener may fully penetrate the base
material causing serious injury or death to someone.
Overpowering the fastener can also damage the
tool, creating a safety hazard to both the operator
or bystanders.
9.
Do not fasten into cast iron, tile, glass, or other types of
brittle materials. These materials can shatter and create
sharp fragments which may cause injury.
10. Do not fire tool within 3" (three inches) of the edge of
a concrete base material or within 1/2" (one-half inch)
of the edge of a steel base material.
11. Do not attempt to install a fastener closer than 3"
(three inches) to another previously inserted fastener
in concrete or 1-1/2" (one and one-half inch) in steel.
12. Do not fasten into a concrete base material less than
3 times as thick as the fastener penetration or into a
steel base material thinner than 1/8".
13. Never attempt to install a fastener in a cracked or
spalled area in concrete. Place fastener at least 3"
(three inches) away from a spalled area to prevent
the possibility of the fastener bending and striking
an operator or bystander.
14. Do not attempt to install fasteners in areas that have
been welded or cut with a torch as these procedures
may have caused local hardening of the steel.
15. Do not fasten through a predrilled hole unless proper
guidance is provided.
16. If you decide not to make a fastening after the tool has
been loaded, you must always remove the powder load
first followed by the fastener.
17. Never attempt to override the safety features of
this tool.
HANDLING THE TOOL AND POWDER LOADS
1.
Never leave a loaded tool unattended. Once the tool
is loaded, make the fastening immediately or unload
the tool.
2.
Always unload the tool before work breaks, changing
parts, cleaning or servicing, and when storing.
3.
To prevent accidental discharge of loads, never carry the
powder loads in the same container as the fasteners or
other hard objects.
4.
Always store the powder loads in the containers
provided or in an enclosure provided for them. Never
intermix the various power levels. Keep them segregated
in clearly identified containers.
5.
Powder loads should never be used in firearms. They are
normally more powerful that the cartridges supplied
with the firearms.
6.
Powder actuated tools and powder loads should always
be stored under lock and key. Tools must be unloaded
when not in use.
TOOL MALFUNCTION
1.
In the event that a load fails to discharge after the
trigger is pulled, the tool must be kept depressed
against the work surface for a minimum of 30 (thirty)
seconds in case of a delayed load discharge. Then
carefully remove the entire load strip. and dispose of it
in a can of water or other nonflammable liquid. Never
attempt to force or pry a load out of a tool chamber.
2.
Never discard unfired powder loads into a
trash container.
3.
Do not attempt to unload or disassemble a jammed,
stuck or broken tool as improper handling may cause
it to discharge and strike operator and/or bystander.
A jammed tool must be pointed in a safe direction
at all times. Tag the tool and lock it up. Call your
Powers Fasteners representative for proper assistance.