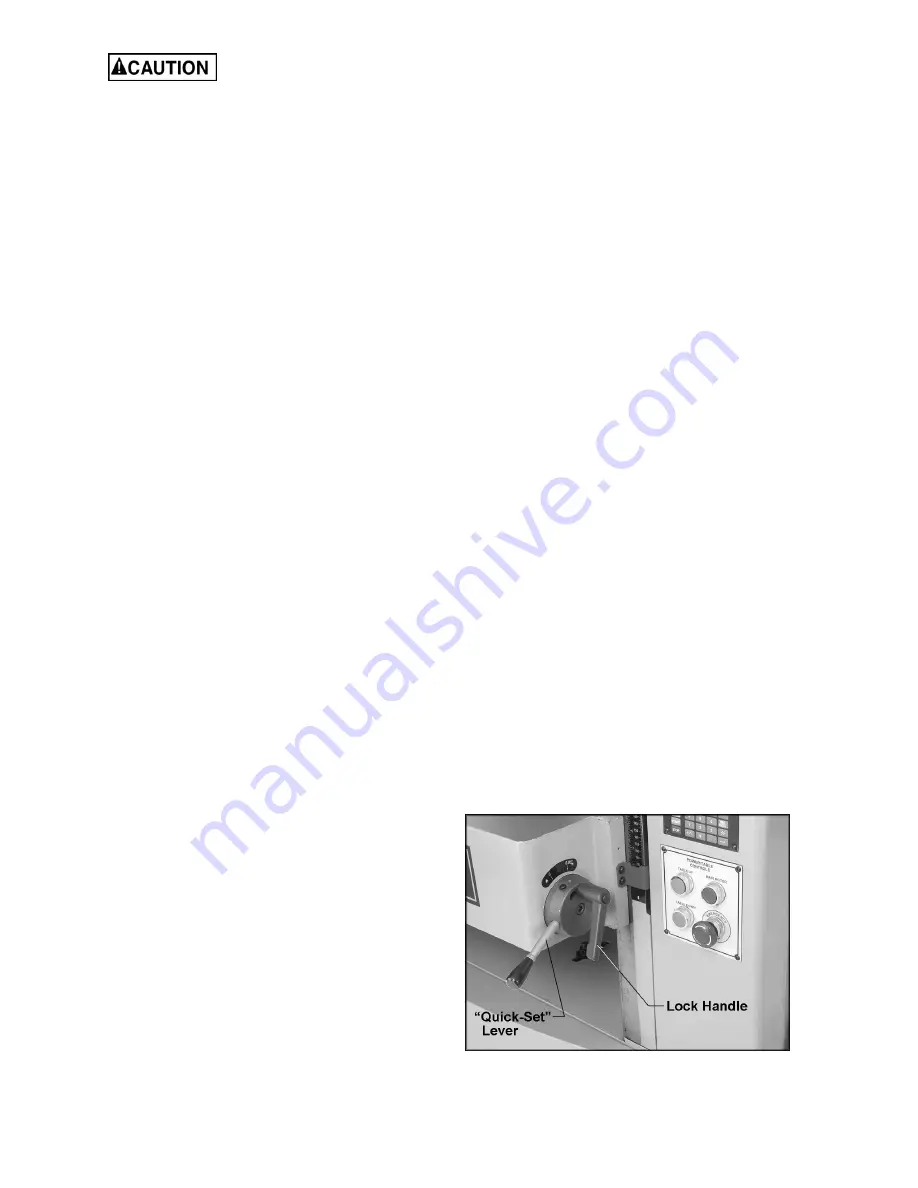
15
A chipbreaker set too low or
with excessive tension may prevent stock
from feeding into the machine.
Pressure Bar
Most planing problems can be traced to
improper setting of the pressure bar. Its function
is to hold down the material after it passes under
the cutterhead and throughout the remainder of
the cut. Its basic setting is to be in line with the
arc of the cutterhead knives.
If it is too high, a shallow “clip” will occur at each
end of the board. If it is too low, stock will not
feed through.
Use a gauge to set the full length of the
pressure bar to be .000-.001” (.02mm) below the
arc of the cutterhead. Figure 11 shows the
height adjustment screw (D) and the spring
tension adjustment screw (E) for the pressure
bar. This initial setup is a starting point and final
adjustment may have to be made during a test
cut.
Outfeed Rollers
The two outfeed rollers are of smooth, one-piece
construction to help avoid marring the finished
surface of the material being cut. Their function
is to continue to feed the material through the
machine after it leaves the infeed roller. The
correct free position setting is 1/32” (.8mm)
below the arc of the cutterhead knives.
Use a gauge, such as a bed and feed roll gauge
or wood gauge block, to check the outfeed
rollers in the same manner as the infeed roller.
Adjust as necessary using the screws (F, Figure
11). When finished adjusting, tighten the hex
nuts on the screws (F, Figure 11).
Table Rollers
The Planer has two table rollers which help
reduce friction of the stock on the table as it
feeds through the machine. It is not possible to
give exact height setting of the table rollers
because each type of wood behaves differently.
As a general rule, however, the table rollers
should be set high when planing rough stock,
and set low for finish cuts.
The planer is equipped with a quick-set table
roller adjustment. With a single lever, you can
raise the rollers from their finishing board height
to a roughing board height. See Figure 12. The
range is 0.00 to 0.05”.
To adjust the height of the table rollers, loosen
the lock handle (Figure 12) and turn the quick-
set lever. Re-tighten the lock handle to lock the
setting.
Figure 12
Summary of Contents for WP2510
Page 35: ...35 17 M15S Specifications ...
Page 39: ...39 Column Assembly ...
Page 42: ...42 Gearbox Assembly ...
Page 46: ...46 Table Assembly ...
Page 48: ...48 Base Assembly ...
Page 54: ...54 Electrical Connections 230Volt ...