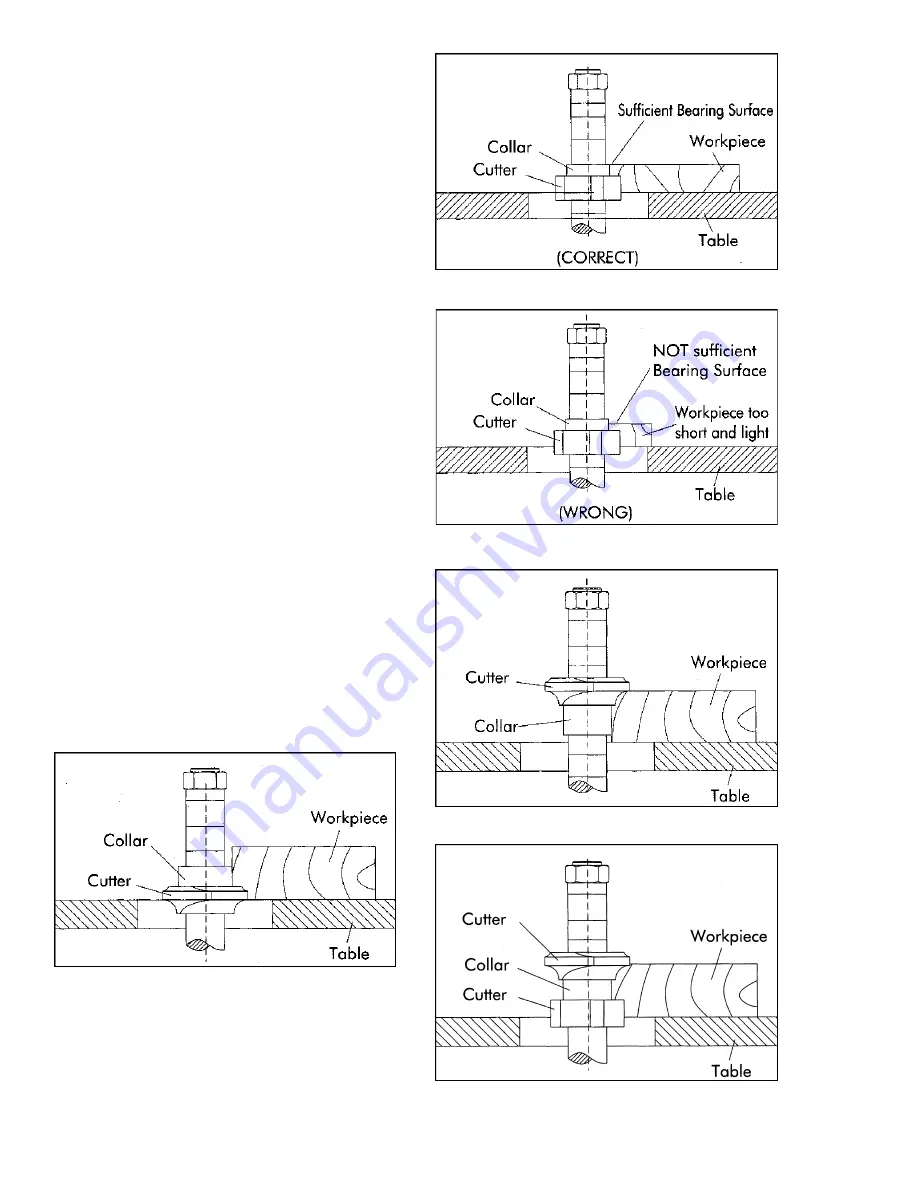
18
POSITION OF COLLARS
When shaping with collars, the collar must have suffi-
cient bearing surface, as shown in Figure 35. Also
the work must be fairly heavy relative to the cut being
made. Under no circumstances should a short, light
workpiece be shaped against the collars, as shown in
Figure 36.
The collars may be used in any of the following posi-
tions: above, below, or between the cutters.
1.
When the collar is used below the cutter, as shown
in Figure 37, the progress of the cut can be seen
throughout the operation. However, any accidental lift-
ing of the work will gouge the wood and ruin the
workpiece.
2.
When the collar is used above the cutter, as shown
in Figure 38, the cut can not be seen, but this method
offers an advantage in that the cut is not affected by
slight variations in the thickness of the stock. Also,
accidental lifting of the workpiece will not gouge the
workpiece; simply repeat the operation to correct the
mistake.
3.
Using the collar between two cutters has the
advantages and disadvantages of the first two proce-
dures, and is frequently used where both edges of the
work are to be molded. See Figure 39.
NOTE: It is advisable to place the cutter as low as
possible on the spindle to reduce spindle deflection
and ensure the best possible finish. Also make sure
that the contacting surfaces of the cutter are smooth,
sharp, clean and without dents.
FIGURE 35
FIGURE 36
FIGURE 37
FIGURE 39
FIGURE 38
Summary of Contents for TS29
Page 25: ...25 Fence Assembly TS29 Shaper ...
Page 27: ...27 Spindle Assembly TS29 Shaper ...
Page 29: ...29 Cabinet Assembly TS29 Shaper ...
Page 31: ...31 Sliding Table Assembly TS29 Shaper ...
Page 33: ...33 Speed Indicator TS29 Shaper ...
Page 35: ...35 Electrical Components TS29 Shaper ...
Page 38: ...38 Quill Assembly TS29 Shaper ...