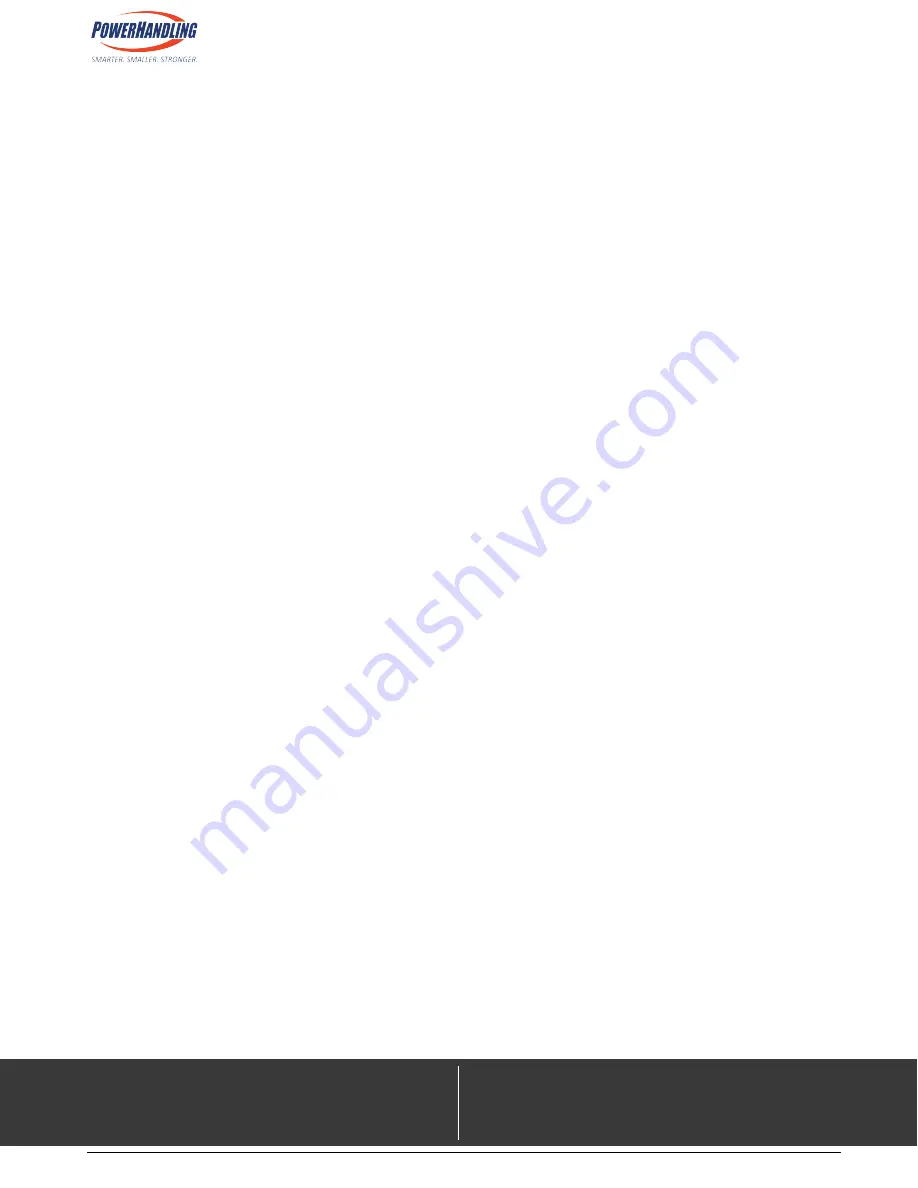
20 of 20
The unit being used in a normal and responsible manner and for the purpose for which it was intended - consistent
with the application details provided to PowerHandling.
The unit is being used in accordance with PowerHandling’s recommended operation and maintenance instructions as
outlined in the documentation provided with the machine.
The unit having all replacement parts provided by PowerHandling. The use of non-original PowerHandling
replacement parts voids all warranties.
All afore-mentioned parts being correctly installed, either by PowerHandling, an authorized reseller or by the customer
(per the instructions or directions provided by PowerHandling).
Warranty Periods
Any and all defects either due to improper use, negligent maintenance, or as a result of normal wear and tear are not covered by this guarantee.
Hence the following are excluded:
Exceptions - Long Term Consumables:
Air motor damage due to air that is not clean (unfiltered) or not dry (no inline water trap fitted).
Brushed electric motor damage caused by over-use (too high a duty cycle for the PowerRoll).
Brushed electric motor damage caused by non-timely brush replacement and/or improper or incomplete brush maintenance.
Terms & Conditions
All parts supplied under warranty will be provided at no charge to the customer FOB, Post Falls, ID, once the failed parts have been received
back at PowerHandling. If the warranty parts are provided in advance of the failed items being returned, they will be invoiced as a normal
parts sale and then a credit note will be applied when the failed parts are received by PowerHandling. If the warranted parts are available
from another PowerHandling location closer to the customer, the parts may be supplied from that location if available.
In the event of a claim being made under the terms of this Warranty which requires the unit to be returned to PowerHandling, the customer
must first obtain a Return Material Authorization (RMA) from their sales contact. All freight and related duties and other costs are to
customer’s account. All parts and labor costs incurred for the repair and / or replacement of warranted parts will be provided at no charge
to the customer.
PowerHandling and its distributors, agents, and resellers assume no other responsibility beyond the scope of this Warranty. The repair or
replacement of the said unit constitutes the limit of PowerHandling’s liability to the customer and PowerHandling specifically disclaims and
excludes rescission as a remedy, or the payment of compensatory or consequential damages, attorney’s fees or costs of litigation.
THE WORLD LEADER IN COMPACT MATERIAL HANDLING SOLUTIONS
Warranty & Guarantee (Machines & Parts / Materials & Labor)
Overview & Conditions:
PowerHandling Incorporated hereby warrants and guarantees all of its material handling machines and parts will be free from
defects in materials and workmanship.
This Warranty is conditional upon:
Servicing the Americas and Asia-Pacific Region
Main Office & Sales |
www.powerhandling.com
[email protected] | 509-244-8860
1110 W Riverside Ave, STE 400, Spokane, WA 99201 (USA)
Servicing all Europe, Middle East, Africa & Brazil
European Sales & Service | www.powerhandling.com
[email protected] | +351 210-909-000
Praceta Outeiro da Vela, Nº 135 2750-455 Cascais (Portugal)
RVB Series is warranted for a period of twenty four (24) months from the date the user receives the unit(s) from
PowerHandling.
PowerPallet, PowerCart H-Series, PowerCart L-Series, PowerMover G-Series, RGB-Series, A-Series are warranted for a
period of twelve (12) months from the date the user receives the unit(s) from PowerHandling.
NiMH battery packs are warranted for a period of three (3) months from purchase. If battery life is less than 12
months, please review your application and charging procedures with PowerHandling to ensure they are consistent
with maximizing their service life.
Lithium Battery Packs are warranted for a period of twelve (12) months from purchase. If battery life is less than 24
months, please review your application and charging procedures with PowerHandling to ensure they are consistent
with maximizing their service life.
Exceptions - Use/Misuse Related:
Vanes / vane kits (for air machines) and brushes / brush kits (for battery machines).
Brushed electric motors are a long-term consumable and will typically need to be replaced after 5-10 brush replacements,
depending on the condition of the commutator bars.
Battery packs are long-term consumables and will need to be replaced periodically. Life depends on many factors including cycling
rate, charging practices, and operating/storage temperatures. Misuse or failing to follow best practices can reduce battery life.
Muffler materials, connectors and other miscellaneous hardware (for air machines).