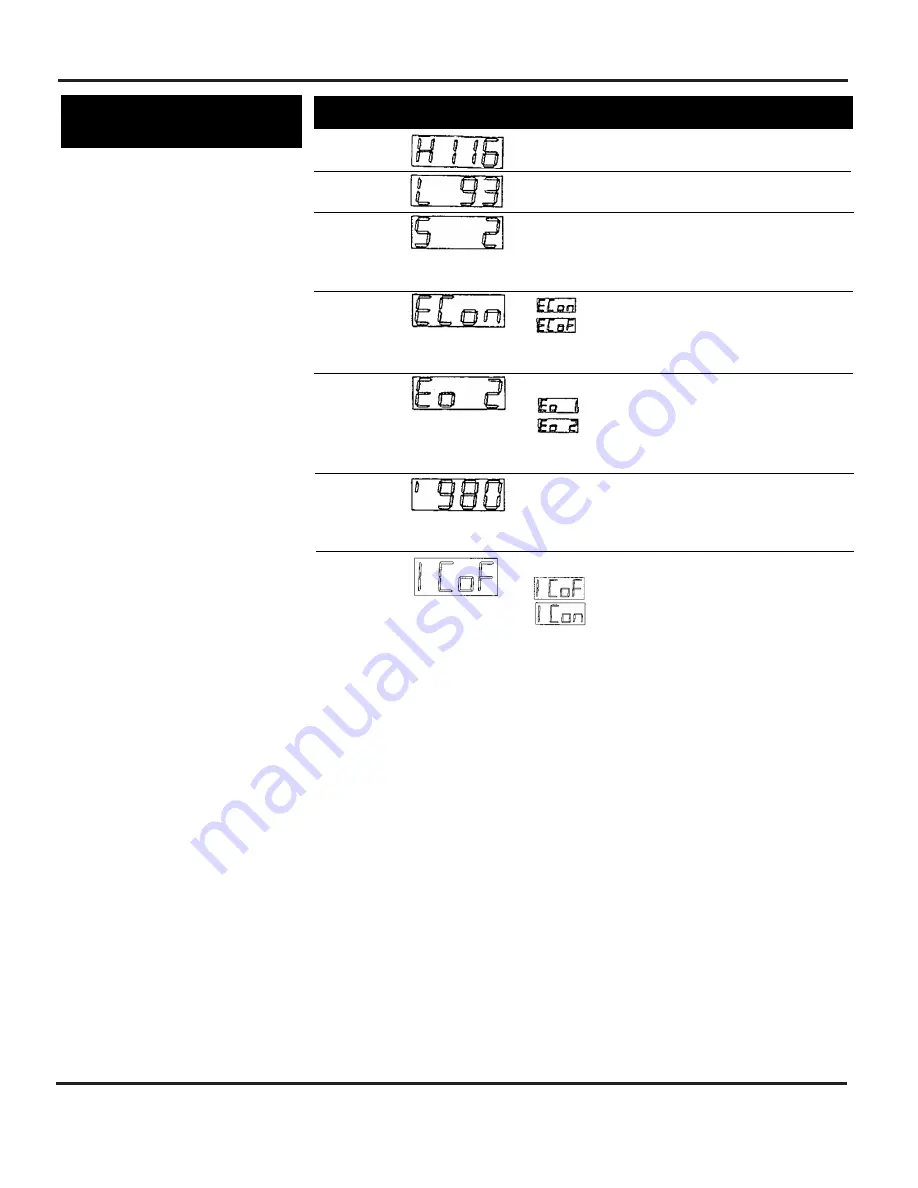
8
Scroll Enclosure Air Compressors
4. SET MODE - Push Mode Selector
Switch so that Set Mode light is
illuminated. Item Selector Switch
can show each of the set contents
as shown in Chart
8. It functions
only when compressor stops.
CHANGING MINIMUM AND MAXI-
MUM PRESSURE SETTING
See Figure 4.
1. Change to Set Mode by utilizing
Mode Switch.
2. Display maximum pressure or mini-
mum pressure by utilizing Item
Switch.
3. You can decrease set pressure by
pushing OFF button and Item
Button at the same time.
4. You can increase set pressure by
pushing Off button and Mode
Button at the same time.
Restrictions:
•
Maximum pressure does not
exceed figure initially set at our
plant.
•
Pressure difference between maxi-
mum and minimum pressure is14.5
psig or over.
• Minimum pressure is 29 psig.
* The display will round all pressure
increments to the nearest psi.
Operating Panel
(Continued)
Max. Pressure
Shows Max. Set Pressure in psig. (This display means
116 psig.)*
Min. Pressure
Shows Min. Set Pressure in psig. (This display means 93
psig.)*
Time to
Shows Time to Change Operating Air End and prevents
Change
the same air end from operating for a long time. 1 on
Operating Air
display means 15 minutes. (This display means 2 x 15
End
minutes - 30 minutes.)
External
means that external operation is set.
Operation
means that external operation is canceled.
(When either displays, it can be changed by pushing
reset switch.)
External
Shows set situation of external output.
Output
displays when emergency stop occurs.
displays when emergency stop or caution
occurs. (When either displays, it can be changed by
pushing reset switch.)
Maintenance
Shows remaining time till intermediate maintenance
Time 1
and inspection in terms of 10 hours. The first figure is
980 (9800 hours) and decreases as operating time
becomes longer.
Group Control
Shows set situation of Group Control.
means that Group Control mode OFF is set.
means that Group Control mode ON is set.
(When either displays, it can be changed by pushing
reset switch.)
Chart 8 - Set Mode
Item
Display
Contents