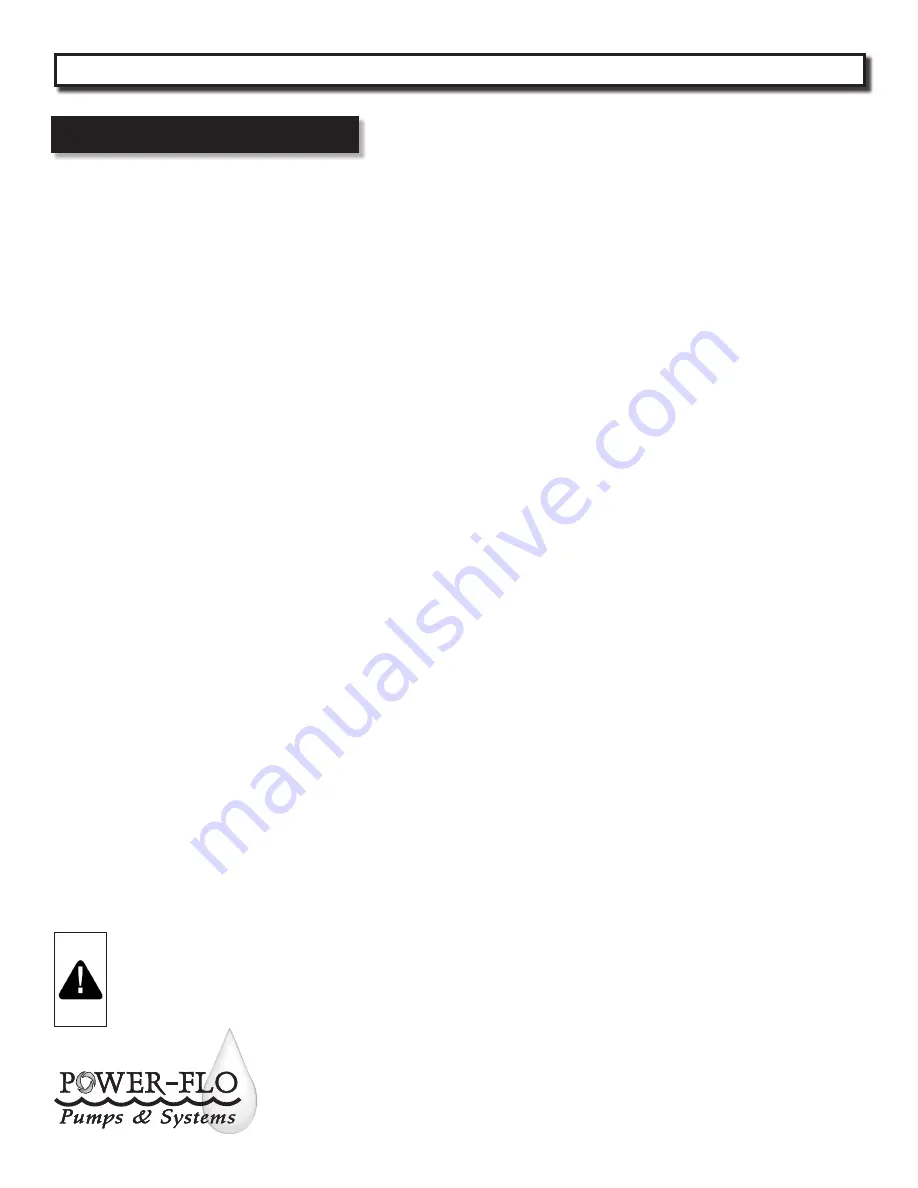
Power-Flo Pumps & Systems • 877-24PUMPS • www.powerflopumps.com
8
10. Remove o-ring (3), replace if damaged,
11. Check motor capacitor (11) with
an Ohm meter by first grounding the
capacitor by placing a screwdriver across
both terminals and then removing
screwdriver. Connect Ohm meter (set
on high scale) to terminals. If needle
moves to infinity (
∞
) then drifts back,
the capacitor is good. If needle does not
move or moves to infinity (
∞
) and does
not drift back, replace capacitor (11).
12. Inspect motor winding for shorts and
check resistance values. Check rotor for
wear. If rotor or the stator windings are
defective, the complete motor must be
replaced.
Shaft Seal:
13. Remove snap ring (6) from seal plate
(8). Remove shaft and motor from seal
plate (8).
14. Remove seal’s (26) rotating member,
spring and retaining ring from seal plate
(8). Examine all seal parts, if seal faces
show signs of wear, uneven wear pattern,
chips or scratches replace entire seal.
DO NOT interchange seal components,
replace the entire shaft seal (26).
If replacing seal, remove stationary by
prying out with flat screwdrive.
Bearings:
15. Examine lower bearing (5), and upper
bearing (23), if replacement is required,
remove by using a wheel puller.
Reassembly
Bearings:
1. Press bearings (5) and (23) onto shaft.
IMPORTANT! - All parts must be
clean before reassembly.
Handle seal parts with extreme
care. DO NOT damage lapped
surfaces.
Shaft Seal:
2. Clean seal cavity in seal plate (34) and
oil. Press seal’s (26) stationary member
firmly into seal plate (8), use a seal tool
or pipe. Nothing should come in contact
with the seal face except the seal tool. Be
sure the stationary is in straight.
3. Place seal’s retaining ring onto shaft.
Lightly oil
(Do not use grease)
shaft and
inner surface of bellows.
4. With lapped surface of seal’s rotating
member facing outward, slide over shaft
using a seal tool, being carefull not to
damage seal face. Make sure spring is
seated in retaining ring and spring is
lined up on rotating member and not
cocked or resting on bellows tail.
Motor:
5. Slide rotor/shaft with bearings and seal
parts (26) into seal plate (8) until bearing
seats into seal plate. Install snap ring (6)
into seal plate (8).
6. Place spring washer (24) onto bearing
(23) and lower motor housing (25) with
motor stator onto seal plate (8).
7. Place screws (4) through seal plate
(8) into housing (25)
and torque to 10
Ft-lbs.
8. Assemble capacitor (11) with bracket
(10) onto motor housing (25). Place
o-ring (9) on motor housing (25).
Power Cord:
9. Check power cord (15) for cracks or
damage and replace if required.
10. Place power cord (15) with nylon
housing (15D), ring (15C), Kellum grip
(15F) and gland nut (15E) into upper
housing (17) and reconect wires to cord
set.
11. Set upper motor housing (17) onto
motor housing (25) being careful not to
damage o-ring (9). Place capscrews (21)
and washer (22) through upper housing
(17) into motor housing (25) and tighten.
12. Tighten gland nut (15E) to 17.5 ft/lbs.
Impeller, V-ring and Volute:
13. Position v-ring (29) into seal plate (8)
until seated.
14. Clean the threads with thread locking
compound cleaner. Apply removable
Loctite® 242 or equivalent to shaft
threads. Screw impeller (31) onto the shaft
hand tight while using a screwdriver in
the slot at the end of the shaft to hold it
stationary. Rotate impeller to check for
binding.
15. Position gasket (2) on volute flange
and position impeller and motor housing
assembly on volute (1).
16. Place lock washers (28) on cap screws
(27) and screw into volute (1). Torque
to 25 ft/lbs. Check for free rotation of
impeller.
17. Re-attach strainer (32) and legs (33).
18. Refill with cooling oil. 40.6 oz (1.2 liters)
Float Switch:
19. Attach float (34) to upper motor
housing (17) with cable clamp (35) and
screw (36). Leave a minimum tether of
3.50 inches from cable clamp to end of
float. (see Fig. 5 on page 9 and also page
4)
Service
PFS411HTCE-2
Submersible Effluent, Sump & Sewage Pumps