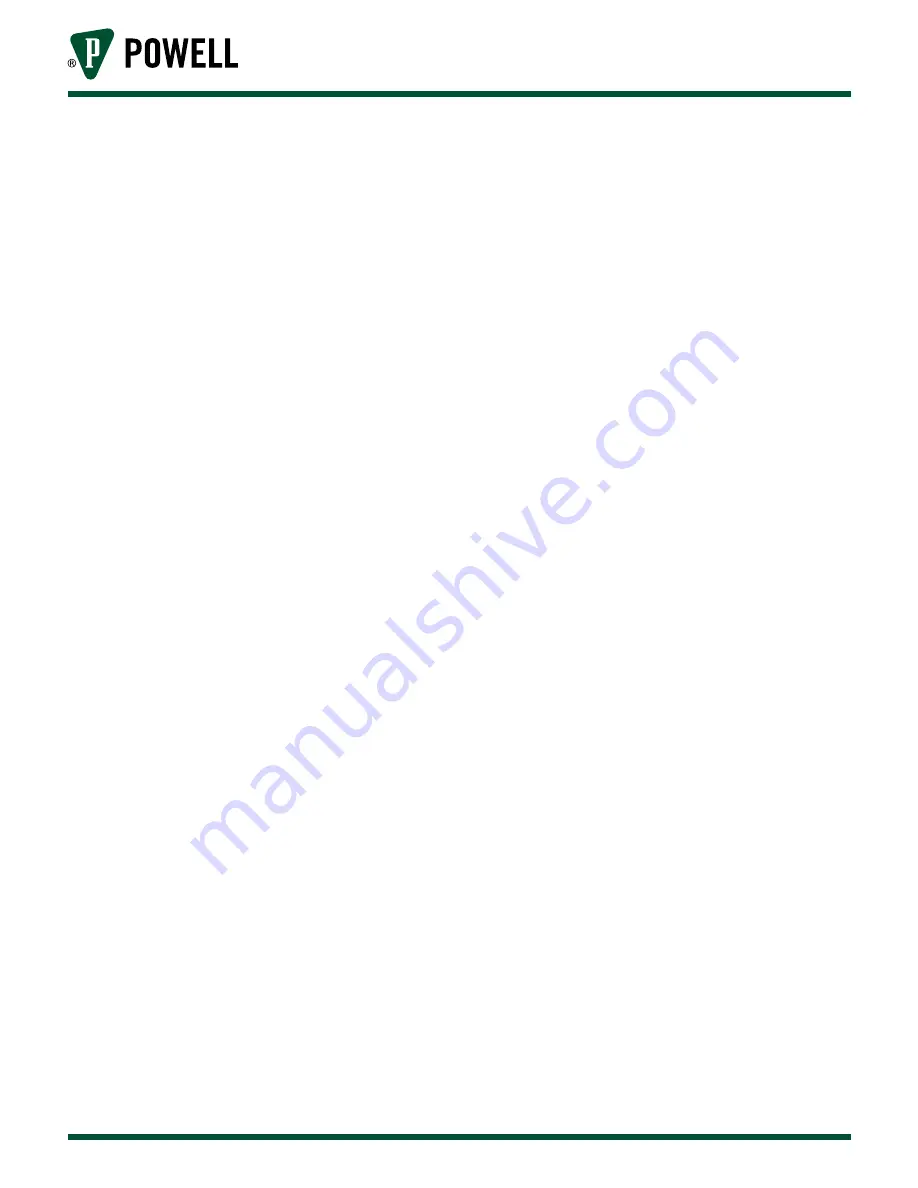
2) Closing Operation
By either energizing the close solenoid
or depressing the manual close button,
the close latch (Figure 1, #4) is rotated
counterclockwise and releases the
close roller (Figure 1, #3) permitting the
flywheel (Figure 1, #1 & #2) to rotate
counterclockwise by the force of the close
spring. This action, transmitted to the
by means of
the pull rod (Figure 1, #13) transfer crank
(Figure 1, #14 & #16), pulls the close toggle
through the center against link
(Figure 1, #19) which is tied to the frame.
This action rotates the output crank
(Figure 2, #22) counterclockwise. The
Pole 1 bellcranks (Figure 2, #23), on the
same shaft as the output crank, also rotate
counterclockwise, and by means of the
horizontal connecting bar (Figure 2, #28)
rotate Pole 2 and 3 bellcranks. This rotation
compresses the opening spring
(Figure 2, #29), closes the vacuum
interrupters connected with each operating
rod (Figure 2, #25), and compresses the
wipe spring (Figure 2, #26) on each pole
when the trunnion (Figure 2, #24)
continues
moving after the operating rod
(Figure 2, #25) stops. Rotation of an arm
(Figure 2, #34) coupled to the output shaft
(Figure 2, DD) changes the auxiliary switch
(Figure 2, #37) position, and the position
flag (Figure 2, #38) indicates “CLOSED”. The
lever (Figure 2, #44) is moved out of the
notch in the flywheel (Figure 1, #2) and with
the close latch
(Figure 1, #4) in position to
catch the close roller, the limit switch
(Figure 2, #43) energizes the gear motor
as described under
. With the ground and test device
closed, closing spring discharged, the
toggle linkage appears as shown in
Figure 3 (b). With the ground and test
device in the closed position, the links
(Figure 1, #17) can move up past the close
toggle without disturbing it as they are
slotted to accommodate a close spring
charged, ground and test device closed, the
toggle linkage appears as shown in
3) Opening Operation
By either energizing the trip solenoid or
depressing the manual trip button, the trip
latch (Figure 1, #18) is rotated clockwise
permitting the trip toggle
#20) to collapse and the vacuum interrupter
contacts to open under the force of the
wipe springs
(Figure 2, #26) and opening
spring (Figure 2, #29). At the end of the
opening stroke, a stop block (Figure 2, #30)
on the bottom of the trunnion
(Figure 2, #24) strikes set screws in the
horizontal connecting bar (Figure 2, #28)
which limits the over travel. At the same
time an opening stop is provided by a plate
and buffer assembly (Figure 2, #50). An
opening dashpot (Figure 2, #31) controls
opening velocity and prevents excessive
rebound of the interrupter contacts.
Rotation of the output shaft (Figure 2, DD)
from a closed to an open position operates
the auxiliary switch (Figure 2, #37) as
described in
Ch 3 Equipment Description,
c. o
perAtIon
,
2) Closing Operation
and
interrupts the trip coil circuit. If the closing
spring is charged, the close toggle can raise
to the top of the slotted link (Figure 1, #17)
thereby permitting the trip toggle to reset
and the trip latch to fall in place under its
roller preparatory to a closing operation. If
the closing spring is not charged, the trip
latch is held, rotated clockwise until the
close spring is compressed as described in
. Electrically
initiated closing is blocked by the latch
checking switch
trip latch is not reset.
Powered by Safety
®
8
Equipment Description
Power/Vac® Electrical Ground and Test Devices
Equipped with ML-17 Mechansim
01.4IB.50100