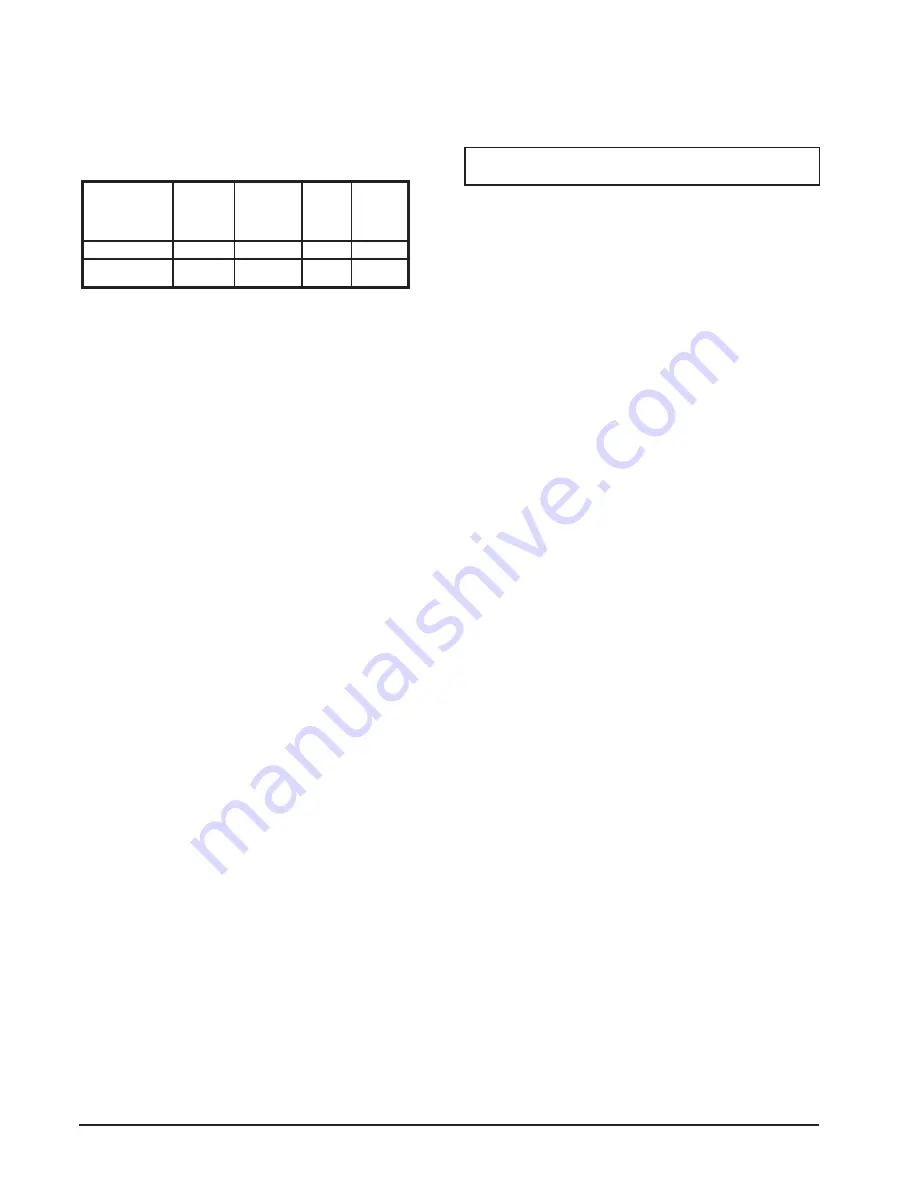
36
© Baxi Heating UK Ltd 2012
Commissioning Checks
1. The gas valve is factory set and the burner pressure
changes as the fan modulates when demand on the
boiler alters. There are two important gas rates that relate
to a corresponding burner pressure that can be checked
as verification during a gas rate check.
2. If necessary the gas rate may be checked after running
the boiler for 10 minutes with any other appliances and
pilot lights turned off.
3. Ensure that the integral programmer and any external
controls are calling for heat, and the selector switch is in
the central heating and hot water position. The current
boiler temperature is shown on the display.
4. To check the gas rate it is necessary to set the boiler
to
#
Calibration Mode
$
.
To carry out this operation
5. Turn both temperature control knobs fully
anticlockwise, then quickly turn the DHW temperature
knob
1
/
4
turn clockwise twice and back fully anticlockwise.
6. The display will now alternate between
#
SF
$
and the
current boiler temperature and both green LEDs will
flash.
7. Turn CH temperature control knob fully clockwise. As
the knob is turned the display will change from
#
0
$
to
#
00
$
indicating maximum rate, then revert to
#
P
$
alternating
with the current boiler temperature.
8. A gas rate measurement may now be made.
Approximate values are:-
Max 2.61 m
3
/hr
Min 0.74 m
3
/hr
9. The
#
Calibration Function
$
is active for 20 minutes
unless the maximum CH temperature is exceeded.
10. The function can be disabled at any time by turning
the DHW temperature knob.
Central Heating System
1. Press programmer CH
button to select heating
(indicated by red neon).
2. Check that any connected room thermostat is calling
for heat.
3. Note that when HW
is selected the 3-way diverter
valve does not allow circulation to the CH circuit
until the storage cylinder contents have reached the
selected temperature. After filling with cold water,
this will normally take between 20 to 25 minutes.
4. With flow to the CH circuit, bleed every radiator and
the pipework high points until all air or air/water mix
has been removed.
N.B. Leave the cap on the auto air vent (above the
pump) partially unscrewed so that the vent remians
operational - note that the burner control goes to safety
shut-down if the system pressure drops below 0.5 bar.
IMPORTANT:
Do not vent the boiler with the burner
running or damage to the heat exchanger may result.
5. Wait until the central heating circuit has reached its
normal temperature of approx. 80 °C before
balancing the radiators in the usual way to
achieve a temperature drop of 10 °C.
6. Allow system to reach full temperature (all radiators
at working temp.) and note “hot system” pressure.
Switch boiler off, drain and flush the system.
7. Refill (using a suitable inhibitor) and remove all air
and air/water mix. Check the relief valve is not
“letting” by observing pipe outlet for several
minutes. (“Letting” is usually due to debris on valve
seat. Snapping the valve open-shut a few times will
normally cure this).
8. Check that the system final pressure equals “hot
system” pressure as noted in 7. above. Adjust if
necessary.
9. Set the room thermostat or programmer according
to the manufacturer
$
s instructions.
10.Disconnect filling loop flexible hose and leave in a
secure place for householder.
Domestic Hot Water System
1. With the cylinder fully heated, check DHW output
temperature is approximately 45 to 65 °C (as
selected) using nearest tap and a flow rate of
approximately 5 l/min. Record inlet and outlet
temperatures in Benchmark Checklist.
2. Measure hot water flow rate at bath tap (fully open)
and record in Benchmark Checklist.
3. Refit outer covers in reverse order.
3.2 Hand Over to the User
1. Explain the boiler controls
2. Give guidance if the system is to be shut down for
long periods when freezing is possible
3. Advise the User that for continued efficient and safe
operation of the boiler it is important that annual
servicing is carried out.
4. Explain how to re-start boiler if red neon indicates
lockout.
5. Hand over the User
$
s Instructions.
6. Carefully read and complete all sections of the
Benchmark Commissioning Checklist at the rear of
this publication that are relevant to the appliance and
installation. These details will be required in the event
of any warranty work. The publication must be handed
to the user for safe keeping and each subsequent
regular service visit recorded. For IE, it is necessary
to complete a “Declaration of Conformity” to indicate
compliance to I.S. 813. An example of this is given in
I.S. 813 “Domestic Gas Installations”. This is in
addition to the Benchmark Commissioning Checklist.
Min Gas Rate
Max Gas Rate
Burner
Pressure
(mb)
0.6 - 0.8
6.8 - 7.2
Gas
Rate
(m
3
/hr)
0.7 - 0.74
2.48 - 2.74
CO
(ppm)
2 - 30
30 - 80
CO
2
(%)
8.4 - 8.8
8.7 - 9.2