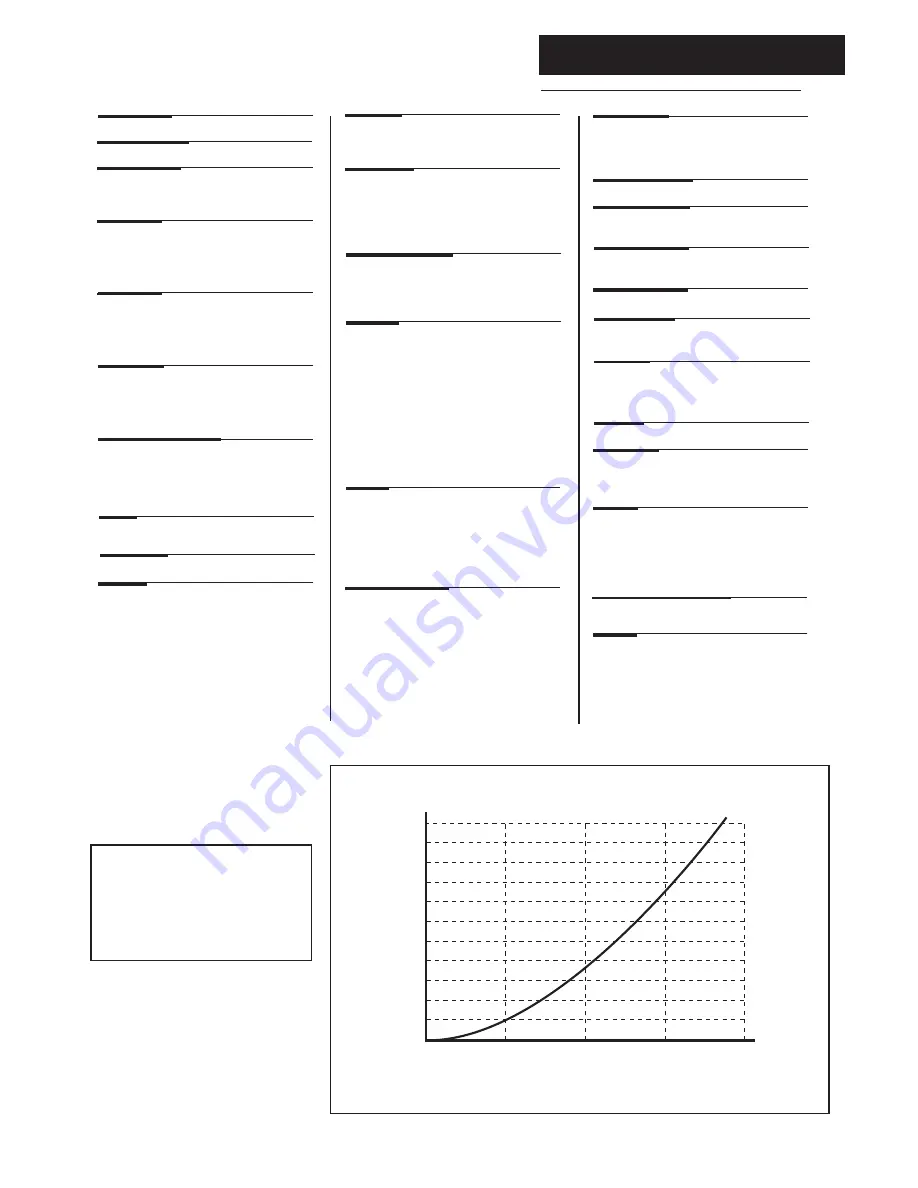
Appliance Category
CAT I
2H
4.0 Technical Data
9
© Baxi Heating UK Limited 2005
Horizontal
Flue Terminal
Diameter -
110mm
Dimensions
Projection -
150mm
Outercase Dimensions
Casing Height
-
850mm
Casing Width
-
390mm
Casing Depth
-
520mm
Weights
kg
Packaged Boiler Carton
- 49.5
Packaged Flue Kit
- 3.6
Installation Lift Weight
- 37.5
Installed Weight (dry)
- 44.5
Connections
Gas Supply
-
15mm
Central Heating Flow
-
28mm
Central Heating Return
-
28mm
Condensate Drain (Pump)
-
10mm o.d.
Recommended System
Temperature Drop
Condensing
20°C
Heat Input (Q)
(Gross) Max
Min
kW 33.76
10.3
Heat Output (P)
(Non Condensing 70° C Mean Water Temp)
Max
Min
kW
30.18
9.2
Electrical Supply
230V~ 50Hz
The boiler must be connected to an earthed
supply. A permanent and switched live are
required. The boiler has a 4 wire connection.
Power Consumption
80W
External Fuse Rating
3A
Internal Fuse Rating
(BS 4265)
Fuse
3.15 AT (PCB)
Max Gas Rate
(2H - G20 - 20mbar)
(After 10 Mins)
kW Input 33.76
m
3
/hr 3.4
Inlet Pressure at Gas Valve
(Natural Gas)
Min
18.1 mbar
Max
22.5 mbar
(see Section 10.1)
Injector
(Natural Gas)
Diameter
6.5mm
Minimum Clearances
(For unventilated compartments see Section 7.2)
Both Sides
- 5mm
Above Casing
- 15mm
Above Casing
Under fixed worktop -
(It is recommended that any
worktop is removable)
- 25mm
Front (For Servicing)
- 500mm
Front (In Operation)
- 5mm
0
10
20
30
40
20
40
60
80
100
120
140
160
180
200
220
Water Flow Rate (litres/min)
Pressure Drop (mbar)
8
17
25
33
42
50
58
66
75
83
91
Pressure Drop (in wg)
Boiler Hydraulic Resistance Chart
Appliance Type
C
13
C
33
NOx Class
5
Heat Output (P)
(Condensing 40° C Mean Water Temp)
Max
Min
kW
32.61
10.0
Water Content
litres
2.6
Static Head
max
30 metres
min
1 metre
Low Head
0.2m min
System Detail
Fully pumped open vented & sealed systems.
No bypass required.
Controls
boiler thermostat, safety thermostat,
flow switch, electronic flame sensing,
temperature protection thermostat &
condensate blockage and level sensors
The efficiency is 90.9%
This value is used in the UK Government’s Standard
Assessment Procedure (SAP) for energy rating of
dwellings. The test data from which it has been
calculated has been certified by 0087.
SEDBUK Declaration
Electrical Protection
IPXX
CO/CO
2
Ratio
0.001
Boiler Flow Temperature
(adjustable)
55° C to 78° C (± 5° C)
Condensate Pump
Head
3 metres
Flow Rate
1.8 l/min
Connection
10mm o.d. (pipe supplied)