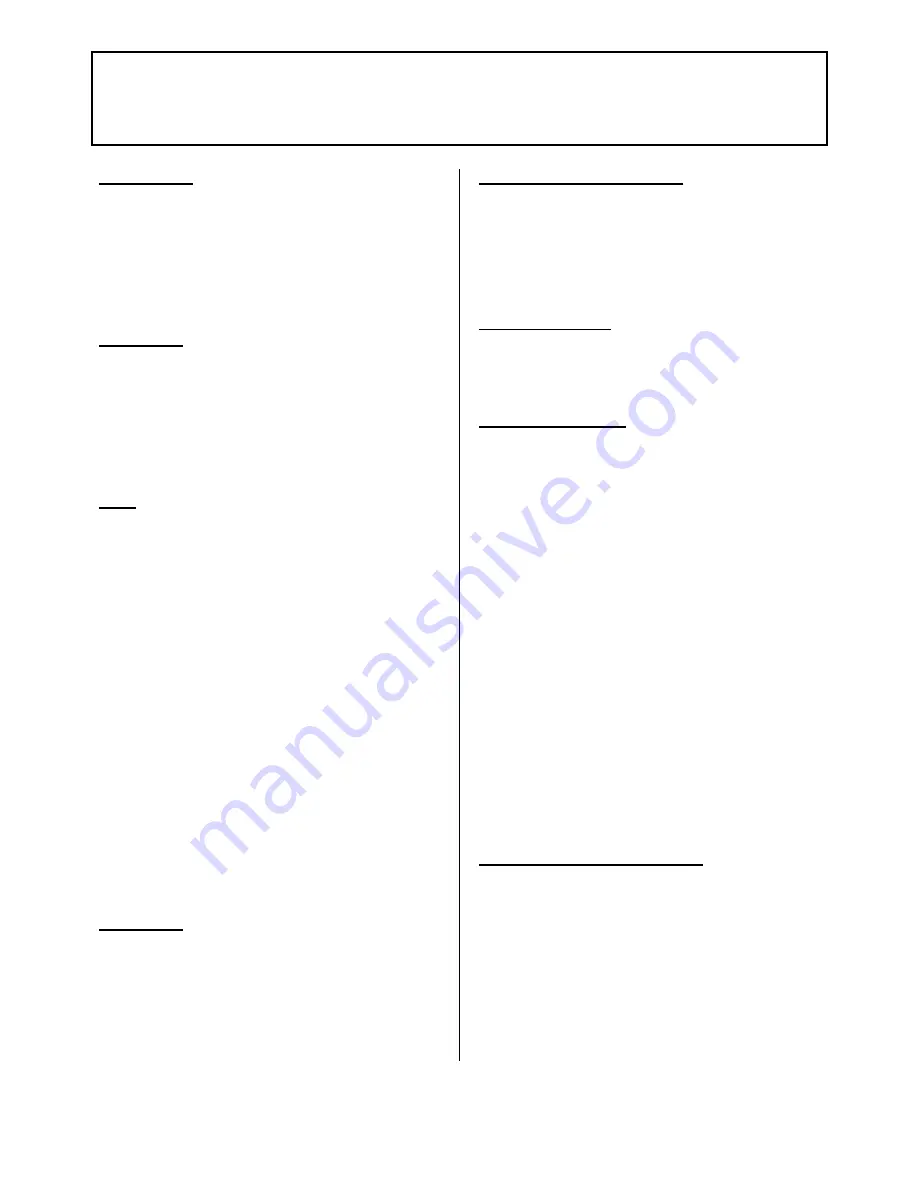
POTTERTON COMMERCIAL PRODUCTS DIVISION SECTION 3
INSTALLATION, OPERATION & MAINTENANCE MANUAL
NXR3
PAGE 7
VENTILATION
Safe, efficient and trouble free operation of
conventionally flued boilers is vitally dependent on the
provision of an adequate supply of fresh air to the
room in which the appliance is installed. Account
must also be taken of any other fuel burning appliance
existing or to be fitted when designing the ventilation
and combustion air systems.
IMPORTANT
:
The use of an extractor fan in the
same room as the boiler (or in an adjacent room in
communication) can, in certain conditions,
adversely affect the safe operation of the boiler
and therefore must be avoided.
Further guidance on ventilation for gas appliances is
provided by BS 6644: 2005. For oil see relevant
Standard.
FLUE
To ensure safe and satisfactory operation the chimney
system, which may be individual or common in the
case of modular boiler installations, shall be capable
of the complete evacuation of combustion products at
all times. The effective height of the chimney
terminal(s) above the boiler(s) flue outlet(s) shall
ensure sufficient buoyancy to overcome the
resistance of the bends, tees and runs of the flue pipe
involved and shall terminate in a down draught free
zone. The number of bends used should be kept to a
minimum and runs of flue pipe less than 45° to the
horizontal should be avoided in order to comply with
the recommendations made in BS 6644: 2005 and
British Gas publication IM/11 "Flues for Commercial
and Industrial Gas Fired Boilers and Air Heaters".
The third edition of the 1956 Clean Air Act
Memorandum and the Building Regulations should be
strictly observed and approval obtained where
applicable, combustion chamber details are given in
section 1.
The flue system must be designed to work specifically
to remove the products of combustion.
IMPORTANT: 90° square bends must not be used
on the flue system, including the boiler flue
spigot, a straight length followed by an "easy
sweep" or lobster back bend should be used.
FLUE SIZE CONSIDERATIONS
Nominal flue connection sizes are given in Table 3,
these sizes refer to the boiler flue connection spigot.
The actual size of the flue system will depend on
individual site applications. Below are general
considerations on sizing flue systems.
Horizontal Flue Runs
Horizontal flue runs are not recommended particularly
over 3m in length, where these are unavoidable
advice should be sought from a flue system specialist.
Common Flue Systems
Where multiple boilers are installed on a common flue
system then the flue system should be designed to
ensure the correct operation of the flue on varying
load conditions. In particular that the appliance flue
draught is within the operating parameter under full
load and partial load conditions. For safe and reliable
operation of the boiler plant it is recommended that
the variance in flue draught available at each
appliance under full and part load operation is
designed to a minimum.
(It is essential that the services of a specialist flue
system manufacturer are sought for the design of
common flue systems)
.
For further information regarding ventilation and
flueing see relevant British Standard publication
BS6644: 2005.
THE ABOVE RECOMMENDATIONS ARE FOR
GENERAL GUIDANCE ONLY. POTTERTON
COMMERCIAL DIVISION CANNOT ACCEPT
RESPONSIBILITY FOR FLUE SYSTEM DESIGNS
BASED ON THE ABOVE RECOMMENDATIONS.
WATER CIRCULATION SYSTEMS
The water circulation system should be indirect and
installed in accordance with the relevant parts of
British Standards Codes of Practice CP342.2 and BS
6644: 2005.
The maximum and minimum design temperature
differential across the boiler should be 20°C and 10°C
and the boiler should be prevented from operating
with flow rates giving a temperature difference across
the boiler greater than 25°C based on the full boiler
output.