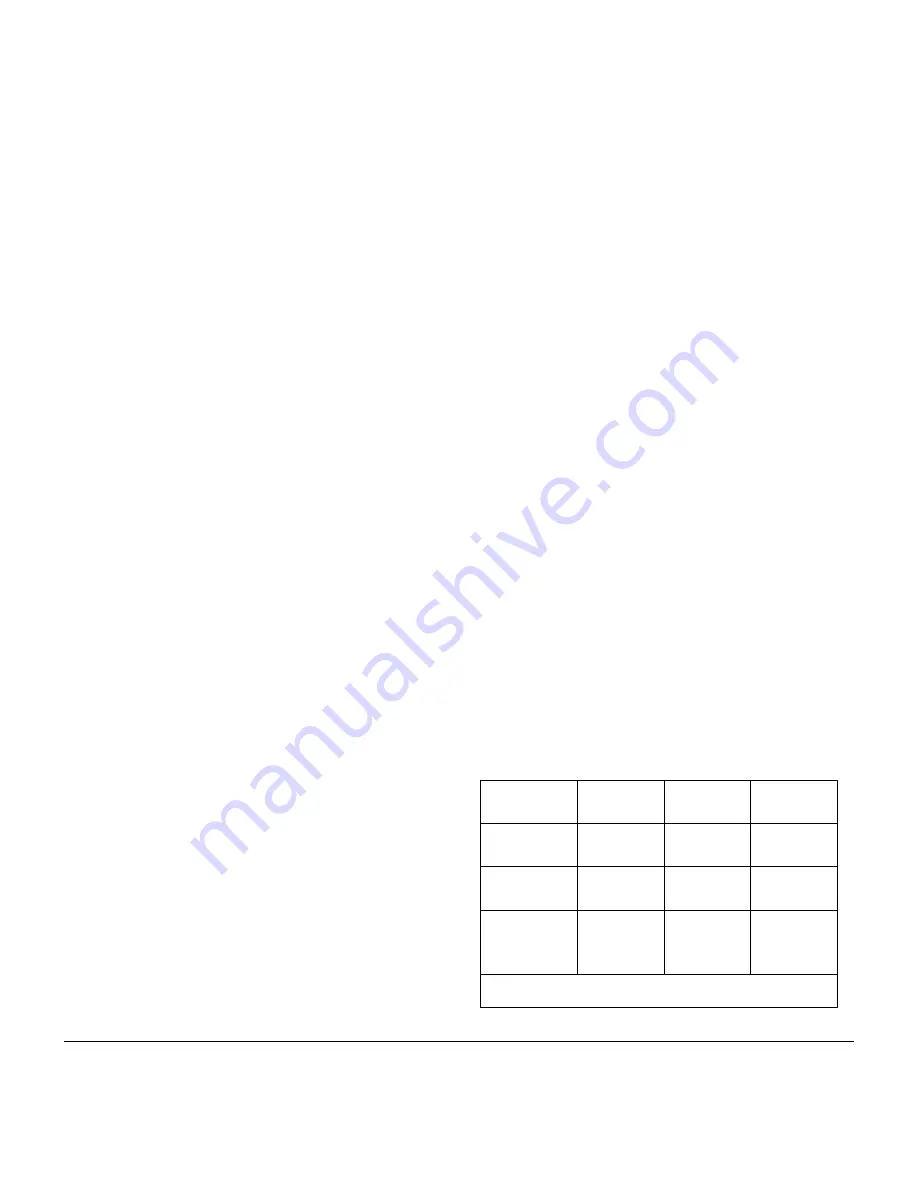
Commissioning - Page 18
14. Fully open all domestic hot water outlets, vent flexible
hose connections to the washing machine and
dishwasher. Remove air from the domestic hot water
distribution system. If this is not done the internal water
flow switch will not function properly. Test for gas
soundness around the gas components using leak
detector fluid.
15. Check the minimum burner pressure (Table 3) by
disconnecting one of the Modulating Coil electrical
connections (wire colours Red or Black).
Note:
The modulating coil connections are 24V only.
Fig. 18.
16. Reconnect and check maximum burner pressure
against Table 3. If any adjustment is necessary see
Section 3.4, 'Gas Pressure Adjustment'.
Note:
The boiler is so designed that if required the
central heating output can be down rated to the lowest
setting stated on the data plate without affecting the
D.H.W output. If adjustment is required see Section 3.4
'Gas Pressure Adjustment'.
3.4
Gas Pressure Adjustment
Note:
The gas pressures are set at the factory (with
central heating output set at maximum) and should not
require further adjustment. If gas pressure readings are
being obtained which differ from that stated in Table 3,
check the inlet pressure using the inlet pressure test
point on the gas valve (Fig. 18). The inlet pressure
should be checked with the appliance at full gas rate, to
ensure this occurs put a high water flow through the
domestic hot water side of the system.
Note:
Full rate will be achieved with cold water supply
temperatures below 15 °C.
Note:
When checking gas inlet pressure only connect
one tube from the measuring manometer's +ve side
(positive). Do not connect the -ve (negative) tube as
with minimum and maximum pressure readings.
Adjustment of the Modulating Valve
Pressures are measured by connecting the +ve
connection to the gas outlet and -ve connection to the
base of the inner casing as described in Section 3.3 .
Set the pressures to the values in Table 3 by adjusting
the gas valve in the following manner.
Note:
It is important to note the order in which the
maximum and minimum pressures are set.
The maximum pressure must always be set before
adjustment of the minimum pressure.
Adjusting the Maximum Pressure - Fig. 12.
i.
Cut off cable tie retaining modulator Cover.
ii.
Remove Cover (C) by twisting it anticlockwise 90°
and levering off with a small screwdriver.
iii.
With a 10 mm spanner turn nut (B), (Clockwise to
increase pressure). Adjust to the value for
maximum pressure stated in Table 3.
Adjusting the Minimum Pressure - Fig. 12.
This adjustment is only to be made after the maximum
setting has been completed.
i.
Disconnect one of the electrical connections of the
modulating coil and tape. (24V only)
ii.
Using a 10 mm spanner hold nut (B) and adjust
screw (A) with a screwdriver (clockwise rotation will
increase the pressure). Set to the value for
minimum pressure stated in Table 3.
iii.
Reconnect the electrical connection to the
modulator.
iv. Check maximum and minimum settings. Repeat
adjustment if required.
v.
Refit cover (C), snap into place and turn.
After the setting operation remove the pressure gauge
tubes from the gas valve body and inner casing. Refit
the pressure test point screws.
3.5
Products Of Combustion Measurement
The combustion performance can be assessed by
placing a suitable sampling probe through the access
hole in the inner casing door whilst the appliance is
running. Typical figures based on a 500 mm flue length
with the boiler operating at maximum output are:-
CO.
0.002 - 0.005%
CO
2
4.5 - 5.0%
Re-fit the screw in access hole after test.
Setting
Pressure
Tolerance
Gas Rate
Maximum
Pressure
15.0 mbar
15.2 mbar
14.8 mbar
2.79 m³/hr
98.1 ft³/hr
Range Rate
8.3 mbar
8.4 mbar
8.2 mbar
2.10 m³/hr
73.7 ft³/hr
Inlet Pressure 20 mbar (8” w.g.)
Minimum
(Ignition)
Pressure
3.5 mbar
3.6 mbar
3.4 mbar
1.34 m³/hr
47.1ft³/hr
Table 3. Gas Pressures
Summary of Contents for Combi 80
Page 6: ...Installation Requirements Page 6 Fig 3 ...
Page 23: ...Servicing Routine Maintenance Page 23 ...
Page 25: ...Servicing Routine Maintenance Page 25 ...
Page 29: ...Replacement of Parts Page 29 Fig 18 ...
Page 39: ...7 Electrical Layouts Page 39 Control Flow Sequence ...
Page 40: ...Functional Flow Page 40 ...
Page 41: ...Electrical Diagram Page 41 ...
Page 43: ...9 Optional Extras Page 43 ...
Page 44: ...Optional Extras Page 44 ...
Page 45: ...Optional Extras Page 45 ...