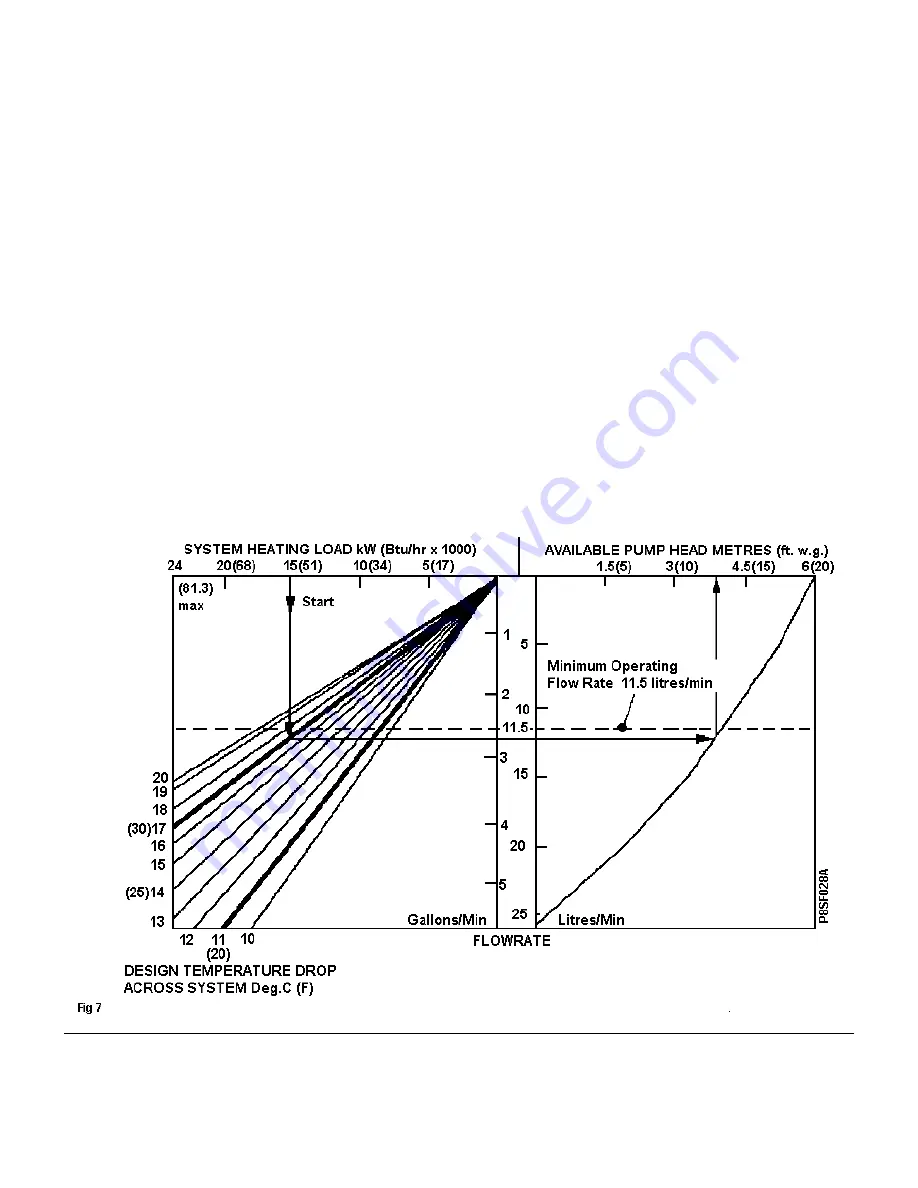
Installation Requirements - Page 12
•
Inhibitors
When the heating system has been completed, it should
be cleaned thoroughly in accordance with BS 7593
(code of practice for Treatment of Water in Domestic Hot
Water Central Heating Systems) to prevent foreign
matter from entering the boiler.
Ideally, it should be flushed before the boiler is
connected, and again after the system has been heated
and is still warm. BetzDearborn Sentinel X300 or Fernox
Superfloc are our recommended cleansers for new
systems.
Where a boiler is being fitted as a replacement to an
existing system, it is best practice to clean the system
prior to fitting the new boiler. In this case BetzDearborn
Sentinel X400 or Fernox Superfloc should be used.
In order to minimise corrosion in the system, inhibit scale
formation and microbiological growth, we recommend
that an inhibitor is added to the system when it is refilled
following the final (hot) flushing. BetzDearborn Sentinel
X100 or Fernox MB-1 are suitable products.
For more information regarding cleansers and inhibitors,
contact:
BetzDearborn Ltd.
Widnes, Cheshire.
WA8 8UD.
Telephone 0151 420 9563.
Fernox Alpha Fry Ltd.
Tandem House, Marlowe Way,
Beddington Farm Road,
Croydon. CR0 4XS.
Telephone 01799 550811.
Summary of Contents for Combi 80
Page 6: ...Installation Requirements Page 6 Fig 3 ...
Page 23: ...Servicing Routine Maintenance Page 23 ...
Page 25: ...Servicing Routine Maintenance Page 25 ...
Page 29: ...Replacement of Parts Page 29 Fig 18 ...
Page 39: ...7 Electrical Layouts Page 39 Control Flow Sequence ...
Page 40: ...Functional Flow Page 40 ...
Page 41: ...Electrical Diagram Page 41 ...
Page 43: ...9 Optional Extras Page 43 ...
Page 44: ...Optional Extras Page 44 ...
Page 45: ...Optional Extras Page 45 ...