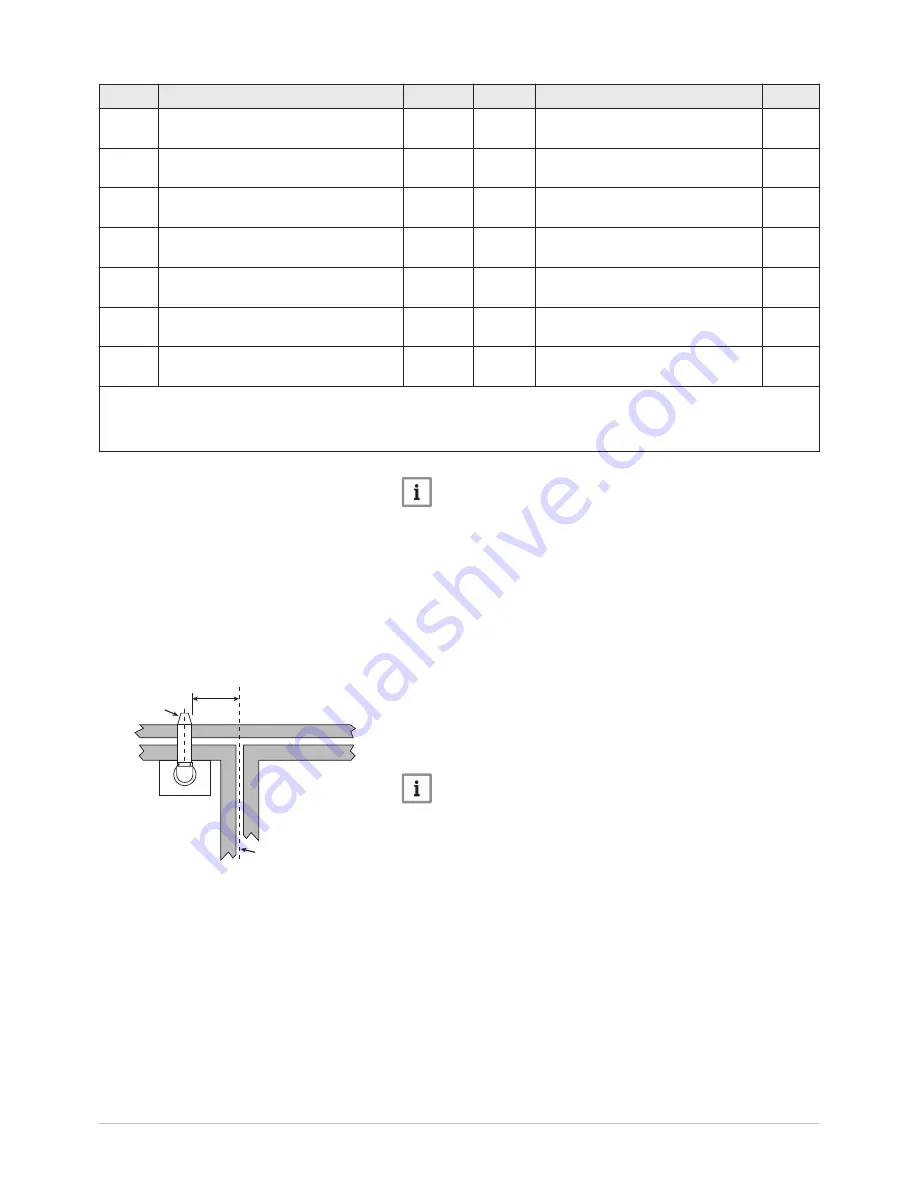
Key
Description
mm
Key
Description
mm
C
(1)
Horizontally to an opening, air brick,
opening window etc.
300
L
From an opening in carport (e.g. door,
window) into the dwelling
1200
D
(2)
Below gutters, soil pipes or drain pipes
25 (75)
M
Vertically from a terminal on the same
wall
1500
E
(2)
Below eaves
25 (200)
N
Horizontally from a terminal on the
same wall
300
F
(2)
Below balconies or car port roof
25 (200)
R
From adjacent wall to flue (vertical on
ly)
300
G
(2)
From a vertical drain pipe or soil pipe
25 (150)
S
From an adjacent opening window
(vertical only)
1000
H
(2)
From an internal or external corner
25 (300)
T
Adjacent to windows or openings on
pitched and flat roofs
600
I
Above ground, roof, or balcony level
300
U
Below windows or openings on pitch
ed roofs
2000
(1) In addition, the terminal should be no nearer than 150mm to an opening in the building fabric formed for the purpose of accommodating
a built-in element such as a window frame.
(2) Only ONE 25mm clearance is allowed per installation. If one of the dimension D,E,F,G or H is 25mm then the remainder MUST be as
shown in brackets, in accordance with BS 5440–1.
Important
Under car ports we recommend the use of the plume displace
ment kit. The terminal position must ensure the safe and nuisance
- free dispersal of combustion products.
If the terminal discharges onto a pathway or passageway, check that com
bustion products will not cause a nuisance and that the terminal will not
obstruct the passageway.
If a terminal is less than 2 metres above a balcony, above ground or
above a flat roof to which people have access, then a suitable terminal
guard must be provided.
1
Property boundary line
2
Terminal assembly
3
Top view rear flue
A
300mm minimum*
*Reduction to the boundary is possible down to 25mm but the flue deflec
tor must be used.
Important
The distance from a fanned draught appliance terminal installed
parallel to a boundary may not be less than 300mm in accordance
with the diagram opposite.
Fig.17
Property boundary
PN-0000457
3
1
2
A*
5 Before installation
7678846 - A - 22052017
33