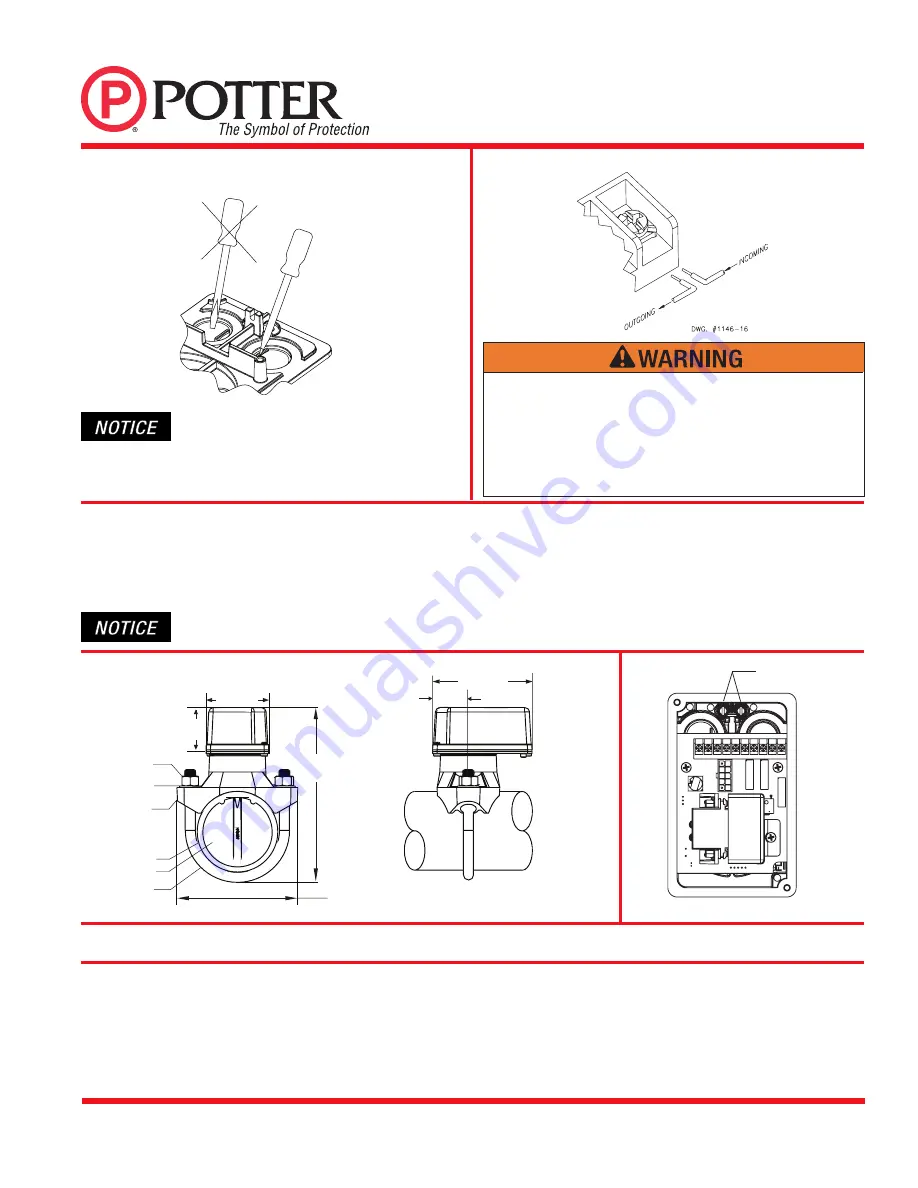
PRINTED IN USA
PAGE 3 OF 6
AUTO TEST VSR (VSR-AT)
VANE TYPE WATERFLOW ALARM SWITCH WITH
ELECTRONIC RETARD AND AUTO TEST FEATURE
MFG. #5401239 - REV B
3/14
Removal of Waterflow Switch
•
To prevent accidental water damage, all control valves should be shut tight and the system completely drained before waterflow detectors are
removed
or
replaced.
• Turn off electrical power to the detector, then disconnect wiring.
•
Loosen
nuts
and
remove
U-bolts.
• Gently lift the saddle far enough to get your fingers under it. With your fingers, roll the vane so it will fit through the hole while continuing
to lift the waterflow detector saddle.
• Lift detector clear of pipe.
To remove knockouts: Place screwdriver at inside edge of knockouts, not in
the center.
DWG 1146-4
Fig. 2
Do not drill into the base as this creates metal shavings which can
create electrical hazards and damage the device. Drilling voids the
warranty.
Fig. 3 Switch Terminal Connections Clamping Plate Terminal
An uninsulated section of a single conductor should not be looped around the
terminal and serve as two separate connections. The wire must be severed,
thereby providing supervision of the connection in the event that the wire
become dislodged from under the terminal. Failure to sever the wire may
render the device inoperable risking severe property damage and loss of life.
Do not strip wire beyond 3/8" of length or expose an uninsulated conductor
beyond the edge of the terminal block. When using stranded wire, capture all
strands under the clamping plate.
Maintenance
Inspect detectors monthly. If leaks are found, replace the detector. The VSR-AT waterflow switch should provide years of trouble-free service.
Fig. 4 Mounting Dimensions
DWG. 1146-14
3.50 in
(89.0 mm)
2.34 in
(59.4 mm)
PIPE DIA.
+ 5.25 in
(+ 133.4 mm)
5.56 in
(141.2 mm)
2.00 in
(50.8 mm)
U-BOLT NUT
U-BOLT WASHER
PIPE SADDLE
PIPE
PLASTIC PADDLE
U-BOLT
NOMINAL PIPE DIA. +1.75 in (+44.5 MM) FOR DN 50 – DN 65 2–2.5 in
NOMINAL PIPE DIA. +2.125 in (+54.0 MM) FOR DN 80 – DN 200 3–8 in
Fig. 5
GREEN GROUND
SCREWS
Testing
The frequency of inspection and testing for the Model VSR-AT and its associated protective monitoring system shall be in accordance with applicable
NFPA Codes and Standards and/or the authority having jurisdiction (manufacturer recommends quarterly or more frequently).
An inspector’s test valve shall be provided for commissioning and test purposes when required by the AHJ. If there are no provisions for testing
the operation of the flow detection device on the system, application of the VSR-AT is not recommended or advisable.
A minimum flow of 10 GPM (38 LPM) is required to activate this device.
Advise the person responsible for testing of the fire protection system that this system must be tested in accordance
with the testing instructions.