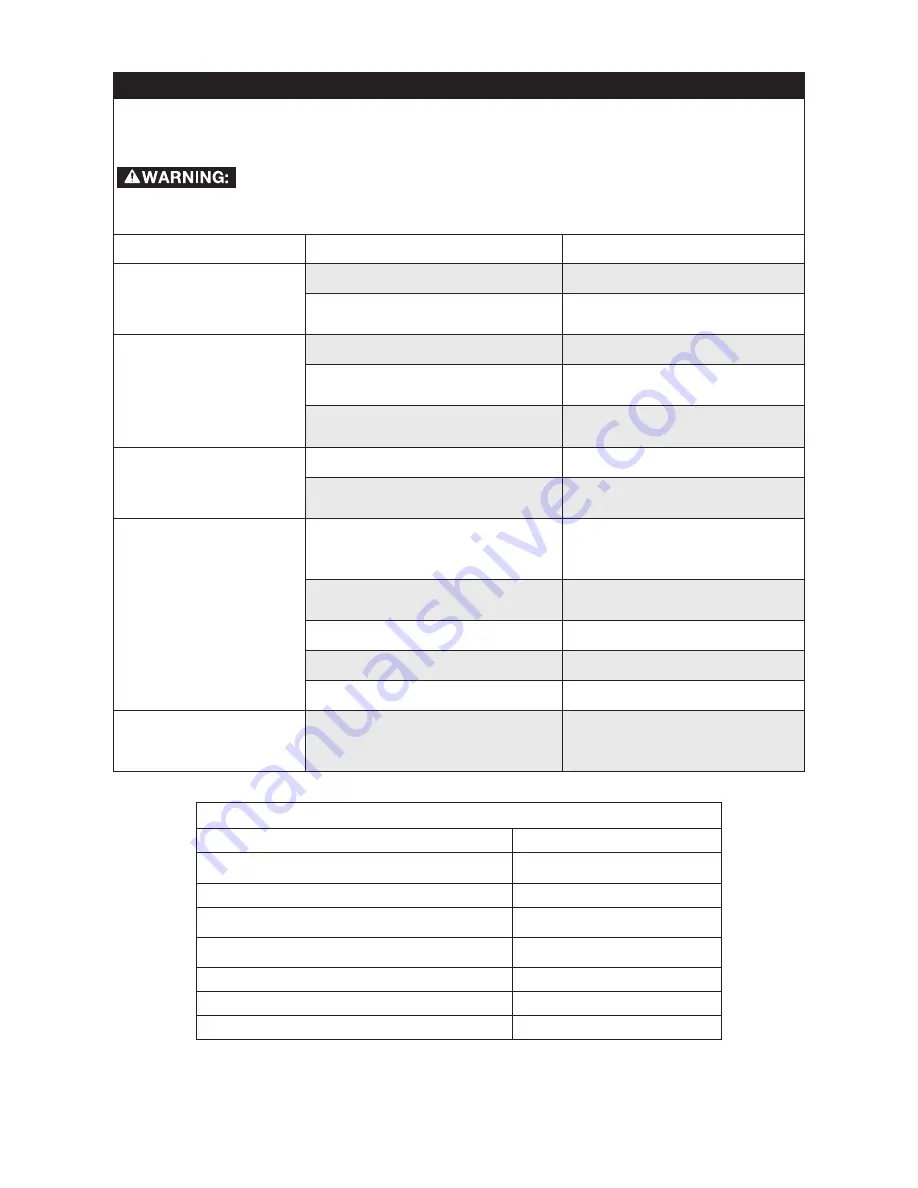
15 - ENG
TROUBleSHOOTInG GUIDe
MANY COMMON PROBLEMS CAN BE SOLVED EASILY BY UTILIZING THE CHART
BELOW. FOR MORE SERIOUS OR PERSISTENT PROBLEMS, CONTACT A PORTER-
CABLE SERVICE CENTER OR CALL 1 888 848-5175.
To reduce the risk of serious personal injury, AlWAyS disconnect
air from tool and engage trigger lock, before all repairs.
SyMpTOM
pROBleMS
SOlUTIOnS
Air leak near top of
tool or in trigger area
Loose screws.
Tighten screws.
Worn or damaged
o-rings or seals.
Install Overhaul Kit.
Tool does nothing or
operates sluggishly
Inadequate air supply.
Verify adequate air supply.
Inadequate lubrication.
Put 5 or 7 drops of
oil into air inlet.
Worn or damaged
o-rings or seals.
Install Overhaul Kit.
Air leak near
bottom of tool
Loose screws.
Tighten screws.
Worn or damaged
o-rings or bumper.
Install Overhaul Kit.
Tool jams frequently
Incorrect fasteners.
Verify approved fasteners
of correct size and 34°
collation angle.
Damaged fasteners.
Bent collation wire.
Replace with undamaged
fasteners.
Canister or nose screws loose Tighten screws.
Canister is dirty.
Clean magazine.
Driver tip is worn or damaged. Install Driver Maintenance Kit.
Other
Contact a PORTER-CABLE
Authorized Warranty
Service Center
TOOl SpeCIFICATIOnS
FC350B
Height (inch/mm)
14.76/375
Width (inch/mm)
4.72/120
length (inch/mm)
19.09/485
Weight (lbs/kg)
7.28/3.30
Recommended Operating pressure 70-120 psi (4.8 to 8.3 bar)
Air Consumption per 100 cycles
9.74 CFM
loading capacity
80 nails