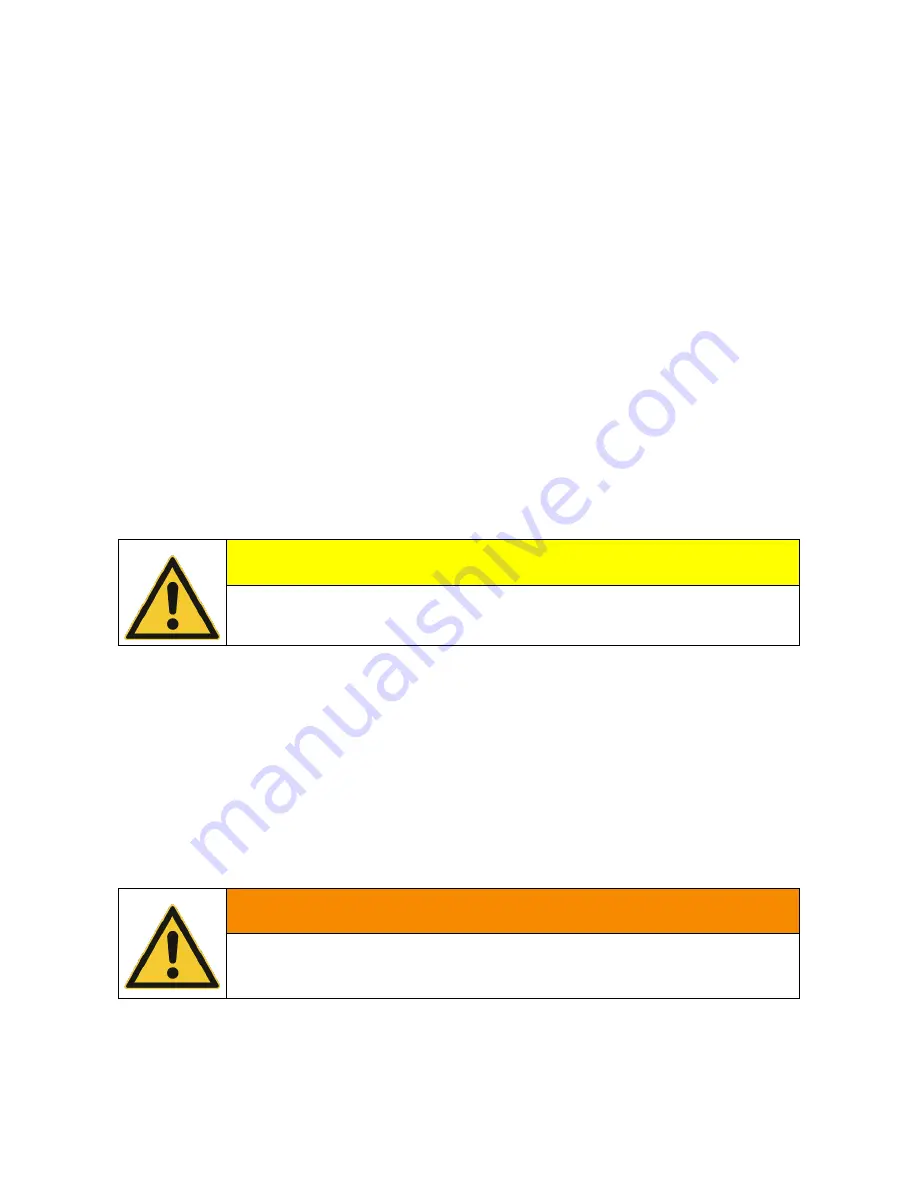
18
RAIL SAW SR-10-26-O & SR-10-26-1
ORIGINAL OPERATION MANUAL
6.1.1
Tool preparation
Hydraulic system
-
Use calibrated flow meter and pressure gauge to check the hydraulic power source. The source should provide a flow of 10
gpm/40 lpm at 2000 psi/ 140 bar. A relief valve setting between 2100-2250 psi/ 145-155 bar is required for the operation of
this tool.
-
The hydraulic system’s back pressure should be less than 250 psi/17 bar, measured at the end of the tool’s operating hoses. All
systems checks should be made at minimum operating temperatures (maximum fluid viscosity of 400 ssu/82 centistokes).
-
The hydraulic fluid cooling system should limit the maximum fluid temperature to 140º F/60º C at the maximum expected
ambient temperature. The minimum cool capacity should be 5hp/3.73 kW at the 40 º F/22 º C difference between ambient
temperature and fluid temperature.
-
A minimum of 25 micron filtration is required for the hydraulic system. For cold weather startup and maximum dirt holding
capacity a filter element sized for 30gpm/120 lpm is recommended.
-
If the tool is used in cold weather, preheat the hydraulic fluid by running power source at low engine speed. Fluid temperature
should be at or above 50 ºF/10 ºC (400ssu/82 centistokes) before use, when using recommended fluid.
CAUTION
Using too thick of fluid may result in tool damage.
The PortaCo G-18D55-53-W power unit is recommended for hydraulic supply. This unit is equipped with two 5 gpm/20 lpm circuits
that can be combined for one 10 gpm/40 lpm circuits.
Tool trigger and trigger lock
-
Check that trigger lock presses into handle tube easily and returns to locking position when released.
-
Check that trigger cannot be activated with trigger lock in the released position.
-
With the trigger lock pressed into the handle tube, pull the trigger to the tube. The trigger should return to the “Off” position
when released.
-
If trigger or trigger stop sticks or doesn’t operate easily check for obstructions. If trigger or trigger lock doesn’t return to “Off”
or lock position when released, check the return springs.
WARNING
Do not operate a tool if the trigger or trigger lock is not working properly!