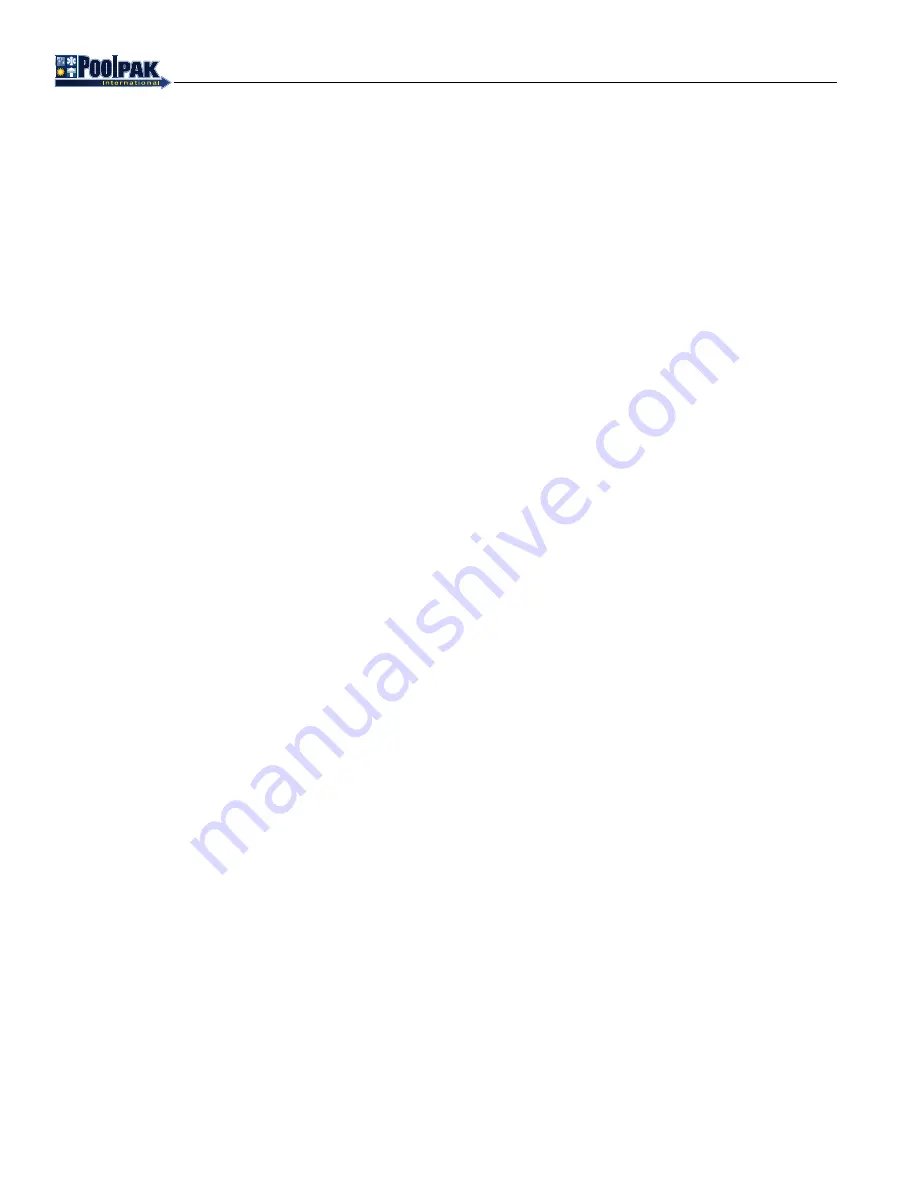
52
EGW05-SWHPEG-20140724
TM
TM
Fire Trip Active
An external fire control system has requested fire trip operation by sending a signal to the PoolPak™ unit Fire Trip
terminals.
Smoke Purge Active
An external control has requested smoke purge operation by sending a contact closure to the PoolPak™ unit Smoke
Purge terminals.
Return Air Temperature Out of Range
The return air temperature is outside of the safe operating range (60°F to 105°F dry bulb, <55°F wet bulb) for the
compressor(s). If the space temperature is close to the set point, the most likely cause of this alarm is a defective return
air temperature sensor.
Supply and Return Fans Not Running
The controller has detected that both fan motors (SR) are not running even though the appropriate digital outputs are
energized. The most likely cause is the motor protectors have been set to the OFF position or a damper feedback issue.
Freeze Danger, Low Supply Air Temperature
The supply air temperature measured by the controller is less than 40°F. This condition can potentially damage a
hot water or steam coil. The ECC III will close the outside and exhaust air dampers in an attempt to protect the non-
functioning coil. The most likely cause of this condition is a failure of the auxiliary heat source (e.g., hot water pump or
valve) or a bad outside air damper or acuator.
Low Compressor Oil Pressure (Recip Compressors only)
The oil pressure monitor on the compressor has detected insufficient oil pressure for 2 minutes. The ECC III will shut
down the affected compressor. The most likely cause of this condition is loss of power during compressor operation.
High Compressor Motor Temperature
The controller has detected that the temperature of the compressor motor winding is too high or the compressor motor is
drawing too much current based on the compressor overload detection device(s).
High Refrigerant Pressure
The controller has detected that the compressor is not running even though the digital output for the compressor
contactor is energized. This condition is detected with the current transducer for the compressor motor. The most likely
cause is the high-pressure safety switch is open. The switch opens if the discharge pressure exceeds 585 psig on R-410A
units. The most likely cause of this condition is insufficient airflow caused by dirty filters or loose belts.
Low Refrigerant Pressure
The controller has detected that the low-pressure safety switch is open. The switch opens if the suction pressure drops
below 45 psig on R-410A units. The most likely cause is insufficient evaporator airflow caused by dirty filters or loose
belts.
Compressor Current Transducer Failed
The controller has detected that the current transducer for the compressor has failed. Compressor operation will be
disabled to prevent repetitive high pressure faults. The most likely cause of this fault is a defective compressor motor
current transducer.