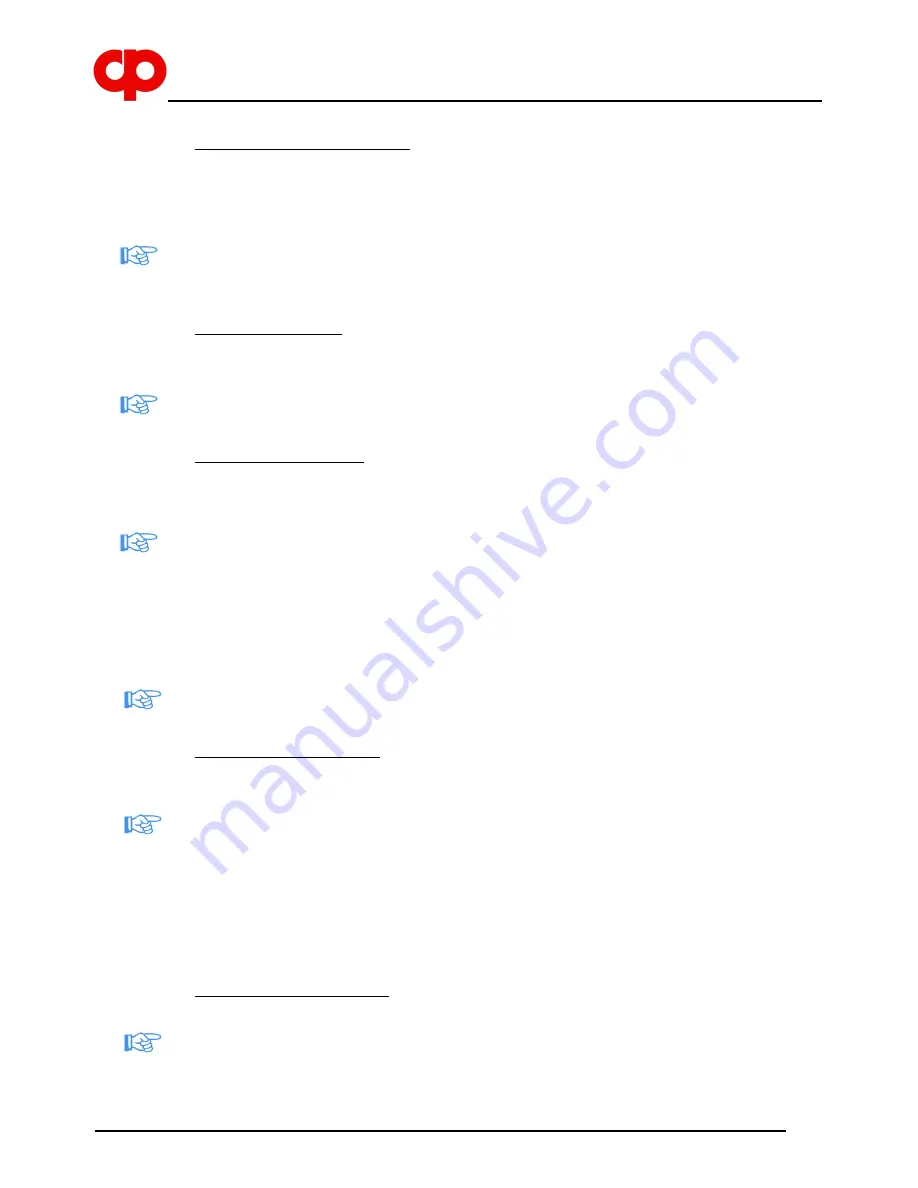
Pompa ad Ingranaggi - Serie WPP, WPL
Gear Pump - WPP, WPL Series
37
1) Single seal (see Figure 1)
a) Access to the mechanical seal
Remove the lantern from the engine, unscrew the fastening pin
F
and disassemble the cou-
pling
H
. Disassemble the clamp
E
and disconnect the pump from the lantern
J
; remove
the feather key
G
from its housing.
Remove, by means of the proper pliers, the seeger rings
?
housed in the front cover
:
, ex-
tract the ball bearing
@
and the gland ring
>
which houses the stationary ring of the me-
chanical seal
<
A. In this way, it is possible to check the wearing status of the seal contact
surfaces. During re-assembly do not pinch the O-ring
=
housed in the front of the pump
body.
b) Replacing static seal
To remove the static part of the seal
<
A from the seal cover
>
, it is necessary to carry out
the same operations as item
a)
and exert a pressure upon the external side of the seal. After
placing the seal cover on a plane and greasing the walls to make assembly easier, insert the
new static seal with the relevant O-ring; use a pad interposed with a soft bearing to exert the
force perpendicularly to the cover.
c) Replacing dynamic seal
To remove the dynamic part of the seal
<
it is advisable to use an iron wire bent at 90° at
one end to hook the first or the second coil of the seal spring
<
B. Exert a traction force par-
allel to the shaft
K
, by paying attention not to scratch this last. After greasing the shaft to
make assembly easier, insert the new mechanical seal by rotating the spring in the direction
opposite to that of the coil; use a pad interposed with soft bearing to press the seal up to
make the spring
<
B rest on the seeger
;
provided on the shaft.
2) Magnet coupling (see Figure 2)
a) Access to the inner magnet
Place a container of suitable capacity under the inner magnet bell; unscrew the Allen screws
`
and disassemble the ring
^
, the bell
a
and the O-ring
Y
. Unscrew the fastening pin 46
and the screw
b
and disassemble the inner magnet
\
. On reassembly, pay attention not to
pinch the sealing O-rings
Y
housed in the flange
Z
.
You are recommended to use tools
in non-magnetic material.
d) Replacing bearing bushes
Carry out the same operations as indicated in items
a)
,
b), c)
,
e)
. To replace the supporting
bushes
4
and
4
A, break them with a chisel or similar, paying attention not to damage the
diameter of the bushing seats. Before inserting the new bushings, clean accurately the seat
with alcohol to remove all impurities and wipe them very well. Fit new bushes by spreading a
thin layer of glue of “LOCTITE 648” type over their outer diameters, by paying attention that
the cut bush and the integer bush match perfectly. First introduce the integer bush and then
the other, by letting glue dry for about 10 - 15 minutes. When the operation is over, set to ze-
ro the bush shims with the relevant housing covers. If a surfacing feed is not available, you
can choose a base plane abraded with fine emery cloth with P80 type grain for rough grind-
ing and 400 type grain for finishing. For assembly, follow the instructions at points
e)
,
c)
,
b),
a)
.
e) Replacing gears and shafts
Carry out the same operations as indicated in items
a), b)
,
c)
.Remove the socket head
screws
B
fastening the rear cover
1
and remove it, considering that the operation might be
difficult because of the accuracy of shafts and dowel pins
C
.