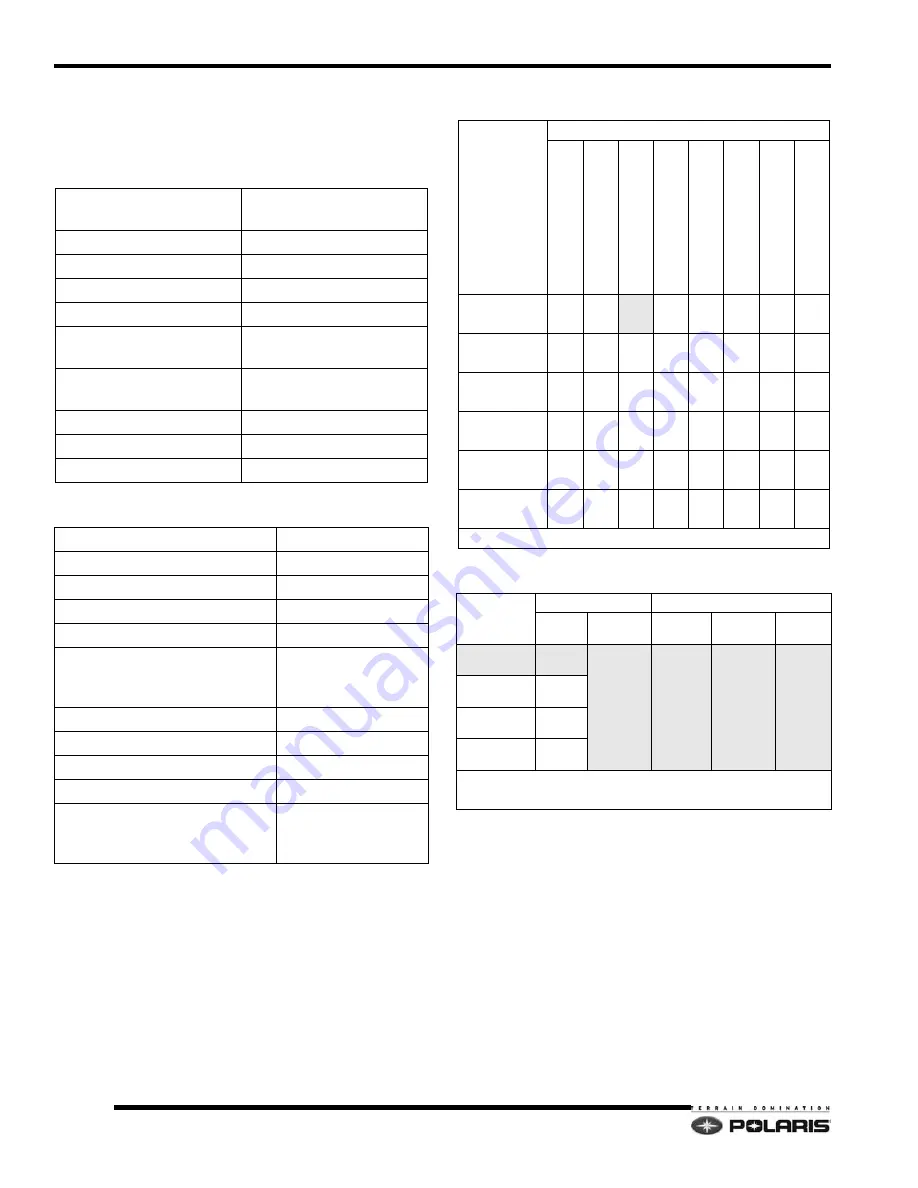
1.42
Model Specifications
9923396 - 2007-2012 EDGE/Widetrak LX Service Manual
©2011 Polaris Sales Inc.
2011 Widetrak LX
Model Numbers: S11SU4BSL / S11SU4BEL
Engine
Engine Type
Fuji Liquid-Cooled / Piston
Port Induction
Model Number
EC50PL023B
Displacement / # Cylinders
488cc / 2
Bore (inches/mm)
2.83 / 72
Stroke (inches/mm)
2.36 / 60
Piston to Cylinder
Clearance (inches/mm)
.0035 - .0049 / .090 - .125
Installed Ring Gap
(inches / mm)
.0078 - .0157 / .20 - .40
Operating RPM ±200
7000
Idle RPM ±200
1600
Engagement RPM ±200
3800
Carburetor Settings
Type
Mikuni VM34SS
Main Jet
195
Pilot Jet
35
Jet Needle / Clip Position
6EJ26 / 2
Needle Jet
P-6 (166)
Throttle Gap (Under Cutaway)
(in/mm)
Drill Bit Size
.240 / 6.1
B - 15/64
Cutaway
3.0
Valve Seat
1.5 Viton
Starter Jet
1.5
Air Screw (Turns Out)
.5
Fuel Octane (R+M/2)
(Minimum)
(Recommended)
87 Non-Oxygenated
89 Oxygenated
Carburetor Jetting
Altitude
Meters
(feet)
Ambient Temperature
< -25°
F/<-3
5
°C
-30°F t
o
-
10°F/
-34
°C to -23
°C
-15°
F
to
+5°F/
-26°
C
to
-15°
C
0°F
to
+2
0°F/
-18°
C t
o
-7°
C
+1
5°F to
+35
°F/-9°C to
+2
°C
+30°
F
to
+50°F/
-1°
C
t
o
+10°
C
+4
5°F to
+65
°F/+7°C to
+18
°C
>+60
°F/>+1
6°C
0-600
(0-2000)
210
#2
200
#2
195
#2
190
#2
185
#2
175
#2
170
#2
170
#1
600-1200
(2000-4000)
195
#2
185
#2
180
#2
175
#2
170
#2
165
#2
155
#1
155
#1
1200-1800
(4000-6000)
185
#2
175
#2
170
#2
165
#2
160
#2
155
#1
145
#1
145
#1
1800-2400
(6000-8000)
170
#2
165
#2
155
#2
155
#2
150
#1
140
#1
135
#1
135
#1
2400-3000
(8000-10,000)
160
#2
155
#2
145
#1
145
#1
140
#1
130
#1
120
#1
120
#1
3000-3700
(10,000-12,000)
150
#2
140
#1
135
#1
130
#1
125
#1
120
#1
110
#1
110
#1
If fuel = 93 non-oxygenated, decrease main jet size by 5.
Clutch Settings
ALTITUDE
meters
(feet)
DRIVE CLUTCH
P2 DRIVEN CLUTCH
Shift
Weight
Clutch
Spring
Clutch
Spring
Driven
Helix
Gearing
0-900
(0-3000)
10-62
100/340
(7043121)
140/200
P2 Tab
(7043495)
40/38-.45
P2
(5137150)
19:41-66
900-1800
(3000-6000)
10-60
1800-2700
(6000-9000)
10-58
2700-3700
(9000-12,000)
10-56
Drive Clutch Bolt Torque: 50 lb.ft. (68Nm)
Re-torque after running engine.