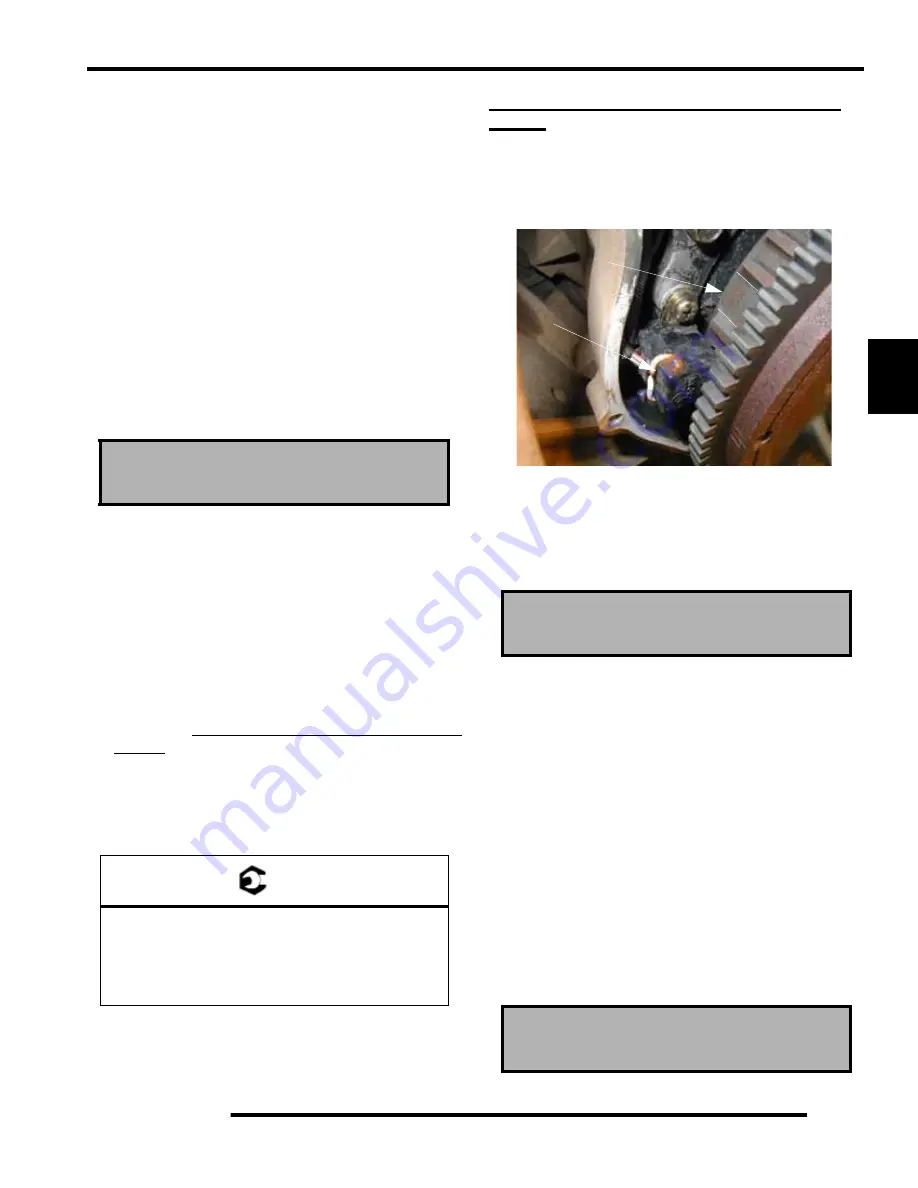
4.17
FUEL INJECTION
4
Injector problems due to dirt or clogging are unlikely due to the
design of the injectors, the high fuel pressure, the use of filters
and the detergent additives in the gasoline. Symptoms that could
be caused by dirty/clogged injectors include rough idle,
hesitation/stumble during acceleration, or triggering of fault
codes related to fuel delivery. Injector clogging is usually
caused by a buildup of deposits on the director plate, restricting
the flow of fuel, resulting in a poor spray pattern. Some
contributing factors to injector clogging include; dirty air filters,
higher than normal operating temperatures, short operating
intervals and dirty, incorrect, or poor quality fuel. Cleaning of
clogged injectors is not recommended; they should be replaced.
Additives and higher grades of fuel can be used as a preventative
measure if clogging has been a problem.
Fuel Injector Resistance Test
If an injector is not operating, it can indicate either a bad injector,
or a wiring/electrical connection problem. Check as follows:
• Using an ohmmeter, test for continuity by placing the
test leads on each pin of the injector.
• Resistance specification is
12.0
Ω
±0.4
Ω
(20°C, 68°F)
Fuel Injector Replacement
1.
Engine must be cool. Depressurize fuel system through
test valve in fuel rail.
2.
Remove the front fender assembly and fuel tank.
3.
Thoroughly clean the area around and including the throttle
body/manifold and the injectors.
4.
Disconnect the fuel injector harness.
5.
Remove the fuel rail mounting screws, doubler plate and
carefully loosen / pull the rail away from the injector.
6.
Reverse the procedures to install the new injector and
reassemble.
Use new O-rings any time an injector is
removed
(new replacement injectors include new O-rings).
Lubricate the upper O-ring lightly with soapy water to aid
installation. The lower O-ring should remain dry. Torque
the fuel rail mounting screws to
5~7 ft. lbs. (6-9 Nm)
. Then
install the doubler plate and torque to
8~9.5 ft. lbs. (11-13
Nm)
.
CRANKSHAFT POSITION SENSOR
(CPS)
General Information
The engine speed sensor is essential to engine operation,
constantly monitoring the rotational speed (RPM) of the
crankshaft.
A ferromagnetic 36-1 ring gear is cast onto the flywheel. The
inductive crankshaft sensor is mounted
0.4 - 1.2 mm (0.015 -
.047 in.)
away from this ring gear. During rotation, an AC pulse
is created within the sensor for each passing tooth. The tooth
gap creates an “interrupt” input signal, corresponding to specific
crankshaft position for PTO cylinder. This signal serves as a
reference for the control of ignition timing by the ECM.
Within one (1) revolution at start-up, the ECM calculates
crankshaft position from the time interval between the
consecutive pulses. Synchronization of the CPS, ECM and
MAP sensor takes place during the first two (2) revolutions each
time the engine is started. Once the engine is started, the ECM
monitors the MAP sensor for the engine intake stroke. The CPS
must be properly connected at all times. If the sensor fails or
becomes disconnected for any reason, the engine will quit
operating.
Crankshaft Position Sensor Test
The crankshaft position sensor is a sealed, non-serviceable
assembly. If fault code diagnosis indicates a problem within this
area, test and correct as follows:
1.
Disconnect main harness connector from ECM.
2.
Connect an ohmmeter between the pin terminals. A
resistance value of
185
Ω
±
20% at room temperature (20
°
C, 68
°
F)
should be obtained. If resistance is correct, check
the mounting, air gap, toothed ring gear (damage, runout,
etc.), and flywheel key.
Injector Resistance Specification:
12.0
Ω
±0.4
Ω
(20°C, 68°F)
=
T
Fuel Rail Mounting Screws:
5~7 ft. lbs. (6-9 Nm)
Doubler Plate Screws
8~9.5 ft. lbs. (11-13 Nm)
Crankshaft Position Sensor Air Gap:
0.4 - 1.2 mm (0.015 - .047 in.)
Crankshaft Position Sensor Resistance:
185
Ω
± 20% @ (20° C , 68° F)
CPS
Interrupt
Summary of Contents for 2007 Sportsman 450 EFI
Page 4: ...NOTES...
Page 20: ...NOTES GENERAL INFORMATION 1 16...
Page 27: ...2 7 MAINTENANCE 2 LUBRICATION FLUIDS SPORTSMAN Component Locations Sportsman Only Deluxe...
Page 58: ...2 38 MAINTENANCE Maintenance Schedule Service Date Hours Miles Service Performed Serviced By...
Page 78: ...3 20 ENGINE Cylinder Head Exploded View EH50PL EH50PL A...
Page 114: ...4 2 FUEL SYSTEM...
Page 139: ...4 27 FUEL INJECTION 4 EFI CIRCUIT Fuel Pump EFI CIRCUIT Ignition Coil...
Page 140: ...4 28 FUEL INJECTION EFI CIRCUIT Idle Air Control EFI CIRCUIT Throttle Position Sensor...
Page 142: ...4 30 FUEL INJECTION EFI CIRCUIT Air Temperature Sensor EFI CIRCUIT Malfunction Indicator Light...
Page 156: ...4 44 CARBURETOR SPORTSMAN 450 FUEL TANK FUEL DELIVERY SYSTEM Fuel System Exploded View...
Page 185: ...5 25 BODY STEERING SUSPENSION 5 X2 CARGO BOX Exploded View...
Page 188: ...5 28 BODY STEERING SUSPENSION X2 SEAT ASSEMBLY Exploded Views...
Page 268: ...NOTES FINAL DRIVE 7 40...
Page 270: ...8 2 GENERAL INFORMATION TRANSMISSION GENERAL Mounting Exploded View x2 x3 x4 x4 x2 x1 x1 x1...
Page 276: ...8 8 GENERAL INFORMATION 242 262 262 262 262 262...
Page 318: ...NOTES BRAKES 9 30...
Page 337: ...10 19 ELECTRICAL 10 ALL WHEEL DRIVE AND SPEEDOMETER TROUBLESHOOTING TEST 1 No All Wheel Drive...
Page 338: ...10 20 ELECTRICAL TEST 2 No Speedometer Display TEST 3 No Reverse Speed Limit...
Page 339: ...10 21 ELECTRICAL 10 TEST 4 No AWD Hub Safety Limit...
Page 341: ...10 23 ELECTRICAL 10 TEST 7 Fuel Gauge Display Not Working TEST 8 Shift Indicator Not Working...
Page 347: ...10 29 ELECTRICAL 10 Components of EFI Alternator and DC CDI Ignition System...
Page 348: ...10 30 ELECTRICAL EFI Ignition System Testing Flow Chart...
Page 353: ...10 35 ELECTRICAL 10 PDM...
Page 363: ...10 45 ELECTRICAL 10 Starter Lockout Diagram EFI Starter Lockout Diagram Sportsman 450...
Page 369: ...10 51 ELECTRICAL 10 BASIC WINCH WIRING Pre wired Models...
Page 370: ...10 52 ELECTRICAL TROUBLESHOOTING DIAGRAMS Power On EFI Start Circuit EFI To ECU Pin 12...
Page 371: ...10 53 ELECTRICAL 10 Ignition Coil EFI Fuel Pump EFI...
Page 372: ...10 54 ELECTRICAL Fan EFI Charging System EFI...
Page 373: ...10 55 ELECTRICAL 10 All Wheel Drive EFI Transmission Switch EFI...
Page 374: ...10 56 ELECTRICAL Reverse Override EFI Differential Solenoid X2...
Page 383: ...11 3 500 EFI INTERNATIONAL QUADRICYCLE 11 Exploded View Foot Brake Supply Hand Brake Supply...
Page 392: ...IX 6...
Page 393: ...WD 1 WIRE DIAGRAM 2007 SPORTSMAN ACTIVE DESCENT CONTROL ADC WIRE DIAGRAM...
Page 394: ...WD 2 WIRE DIAGRAM INTENTIONAL BLANK PAGE...
Page 395: ...WD 3 WIRE DIAGRAM 2007 SPORTSMAN 450 WIRE DIAGRAM...
Page 396: ...WD 4 WIRE DIAGRAM...
Page 397: ...WD 5 WIRE DIAGRAM 2007 SPORTSMAN 500 EFI STANDARD WIRE DIAGRAM...
Page 398: ...WD 6 WIRE DIAGRAM...
Page 399: ...WD 7 WIRE DIAGRAM 2007 SPORTSMAN 500 EFI DELUXE WIRE DIAGRAM...
Page 400: ...WD 8 WIRE DIAGRAM...
Page 401: ...WD 9 WIRE DIAGRAM 2007 SPORTSMAN 500 EFI INTERNATIONAL WIRE DIAGRAM...
Page 402: ...WD 10 WIRE DIAGRAM...
Page 403: ...WD 11 WIRE DIAGRAM 2007 SPORTSMAN 500 EFI X2 WIRE DIAGRAM...
Page 404: ...WD 12 WIRE DIAGRAM...
Page 405: ...WD 13 WIRE DIAGRAM 2007 SPORTSMAN 500 EFI X2 QUADRICYCLE WIRE DIAGRAM...
Page 406: ...WD 14 WIRE DIAGRAM...