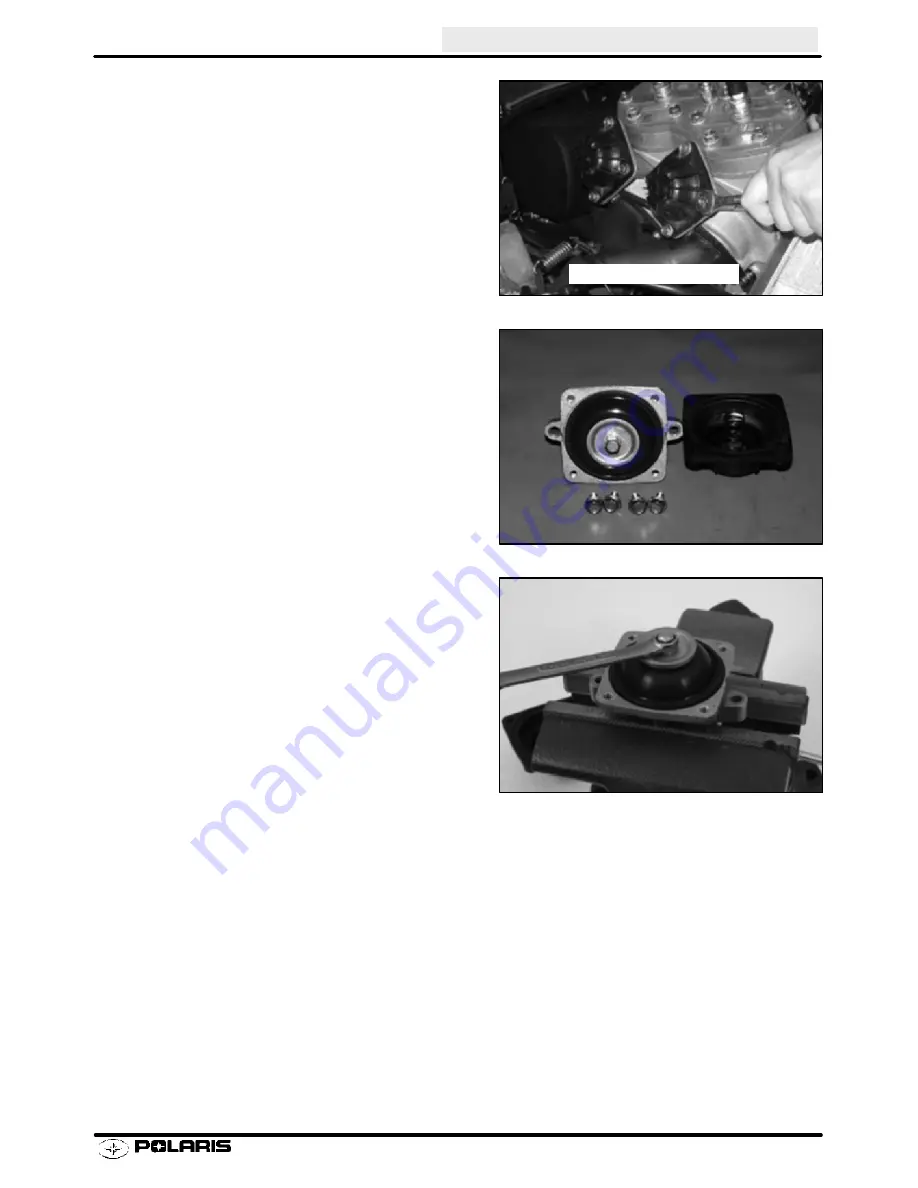
ENGINE
2.43
V.E.S. Removal
1.
Remove the mounting bolts.
On Domestic Engines remove all four (4) mounting bolts
and be ready to catch the spring and cover as you remove
the mounting bolts.
CAUTION:
Valve is spring loaded. Hold cover in position
until all bolts are removed.
2.
Remove exhaust valve assembly from the cylinder(s).
3.
800 Fuji engines, remove four cover bolts, cover, and
return spring.
CAUTION:
Valve is spring loaded. Hold cover in position
until bolts are removed.
4.
If the spring stays in the cover, hold the cover with
spring facing toward you. Rotate spring in a
counterclockwise direction while pulling outward on the
spring. Do not distort the spring upon removal.
5.
Insert V.E.S. in a soft jawed vice. Carefully remove
exhaust valve cap.
NOTE:
Top nut is secured to valve with adhesive. Remov-
ing top nut may damage threads on valve. If nut will not
loosen, apply a small amount of heat to cap. DO NOT
OVERHEAT or damage to the bellows will result.
Domestic Twin Engines
Enfocus Software - Customer Support
Summary of Contents for 2003 Pro X
Page 1: ......
Page 5: ......
Page 30: ......
Page 32: ......
Page 98: ......
Page 132: ......
Page 184: ......
Page 190: ...CHASSIS BRAKES FINAL DRIVE 5 6 Pro X Tunnels 2003 440 PRO X 2003 440 Fan 600 700 800 PRO X ...
Page 212: ......
Page 236: ......
Page 238: ......
Page 267: ...REAR SUSPENSION TRACK TRACTION 7 29 Suspension Lubrication L L L ...
Page 278: ......
Page 301: ...ELECTRICAL 8 23 Wiring Diagram 440 Pro X Fan ...
Page 302: ...ELECTRICAL 8 24 Wiring Diagram 440 Pro X ...
Page 303: ...ELECTRICAL 8 25 Wiring Diagram 600 700 800 Pro X ...
Page 304: ......
Page 309: ...PN 9918053 Printed in USA ...