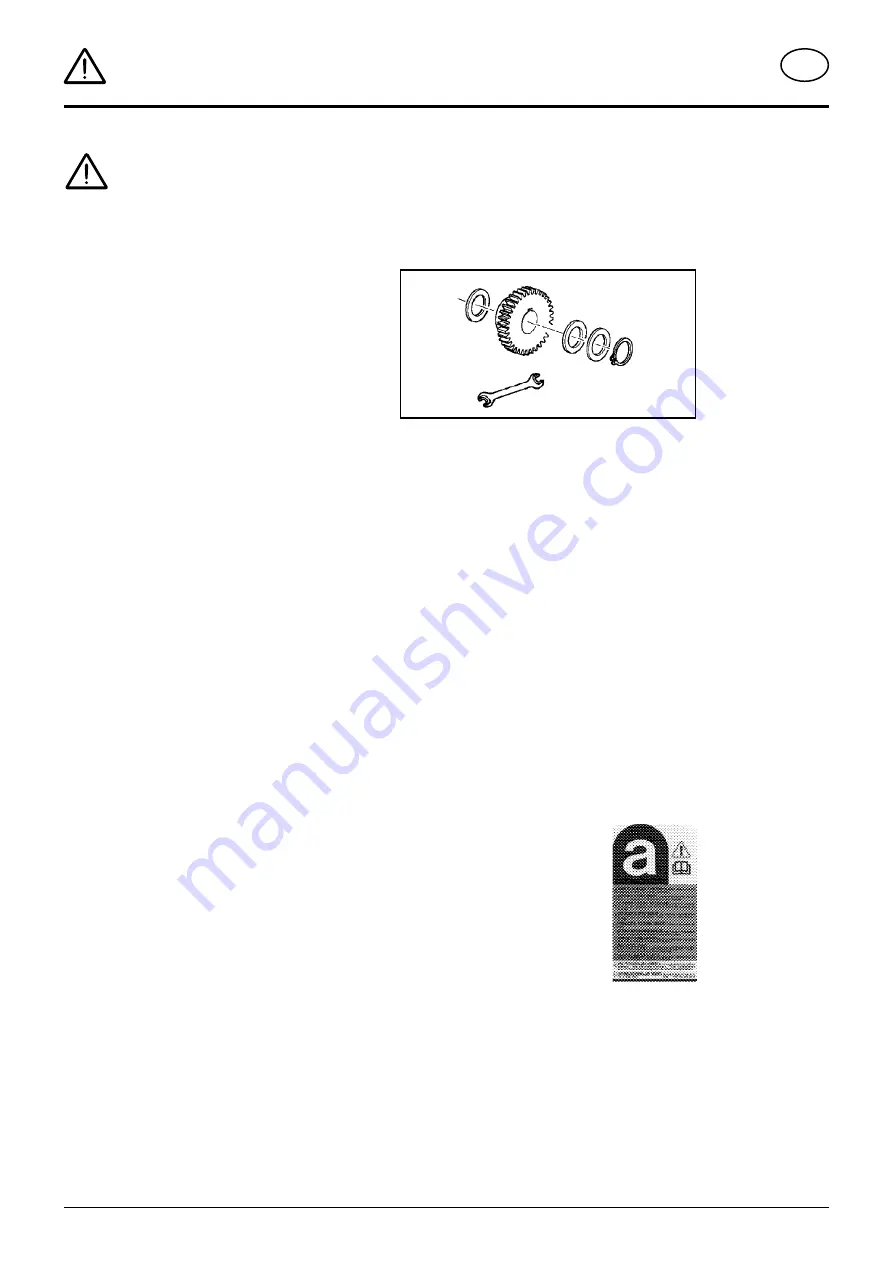
- 23 -
1200_GB-ANHANGA_SICHERHEIT
Supplement - A
EN
Recommendations for work safety
Recommendations for work safety
All points refering to safety in this manual are
indicated by this sign.
1. Operating instructions
a. The operating instructions are important for the correct
operation of the machine. Make sure that the operating
instructions are always on hand when operating the
machine.
b. Keep the operating instructions as long as the machine
is in your hands.
c. Pass the operating instructions on to the buyer when
selling the machine.
d. Make sure that all safety and warning symbols remain
attached on the machine and keep them readable. The
hazard warnings provide important information for a
safe operation and, thus, your safety.
2. Qualified personnel
a. Only persons of legal age, mentally and physically able
and having been trained or familiarized accordingly must
operate this machine.
b. Persons not yet trained or familiarized or under training
must only operate this machine under the supervision
of an experienced person.
c. Inspection, setting and repair work must only be
performed by authorized persons.
3. Repair work
a. These instructions only refer to service, maintenance
and repair operations the user is able to carry out
without assistance. Any work beyond this scope has
to be carried out at authorized workshops only.
b. Repairs on the electrical and hydraulic system, preloaded
springs, pressure accumulators, etc. require sufficient
knowledge, correct tools and protective clothing and,
thus, must only be performed at authorized workshops.
4.) Defined use
a. See "Technical Data".
b. The keeping of operating, service and maintenance
requirements layed down by the manufacturer also
come under the heading of "defined use".
5.) Spare parts
a. The original components and accessories have been
designed especially for these machines and appliances.
b. We want to make it quite clear that components and
accesories that have not been supplied by us have not
been tested by us.
c. The installation and/or use of such products can,
therefore, negatively change or influence the
construction characteristics of the appliance. We are not
liable for damages caused by the use of components
and accessories that have not been supplied by us.
d. Alterations and the use of auxiliary parts that are not
permitted by the manufacturer render all liability invalid.
6.) Protection devices
a. All protection devices must remain on the machine and
be maintained in proper condition. Punctual replacement
of worn and damaged covers is essential.
7.) Before starting work
a. Before commencing work, the operator must be aware
of all operating devices and functions. The learning
of these is too late after having already commenced
operation!
b. The vehicle is to be tested for traffic and operating safety
before each operation.
8.) Asbestos
a. Certain sub-supplied components
of the vehicle may contain asbestos
due to technical reasons. Observe
the warning on spare parts.