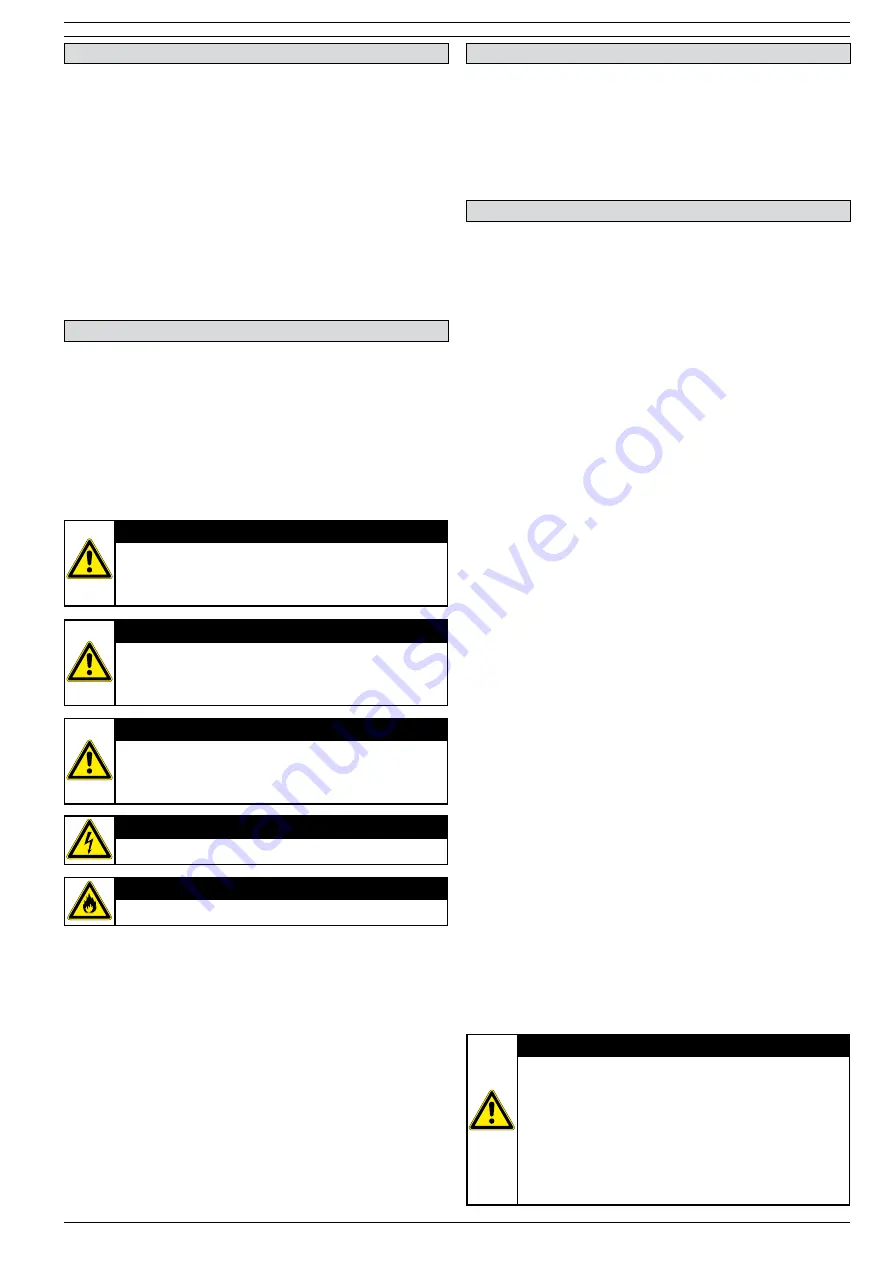
ATTENTION
A remark with additional information for the user.
A remark brings possible problems to the user’s
attention.
CAUTION!
Procedures, if not carried out with the necessary
caution, could damage the product, the workshop or
the environment.
WARNING!
Procedures which, if not carried out with the
necessary caution, may damage the product or cause
serious personal injury.
WARNING!
Denotes risk of electric shock.
WARNING!
Important warning to prevent fire.
PUM_SBT_091102_EN
2/38
PREFACE
Using this manual
This manual is intended to be used as a work of reference for
professional, well trained and authorized persons / user’s to
be able to safely install, use, maintain and repair the product
mentioned on the cover of this document.
Pictograms and symbols
The following pictograms and symbols are used in this manual:
Service and technical support
For information about specific adjustments, maintenance or
repair jobs which are not dealt with in this manual, please
contact the supplier of the product. He / she will always be
willing to help you.
Make sure you have the following specifications at hand:
- The SBT Pneumatic product user manual
1. IMPORTANT SAFETY INSTRUCTIONS
Please read these instructions before installing the Sliding
Balancer Track (hereafter called SBT) system. This will help
you obtain the full benefit from the exhaust removal system
you have selected.
A. Read the Product user manual and Safety Instructions
carefully. Failure to follow these instructions could
cause a malfunction in the system or unsatisfactory
performance.
B. Follow a regular service and maintenance schedule for
efficient operation.
1.1 Identification of the product
The SBT system is made up out of various different parts
which together form the SBT-Exhaust Removal System. All
these individual parts can be traced back to this product
user manual.
2. INTRODUCTION
3. PRODUCT DESCRIPTION
The SBT system consists of a number of parts of which the
Plymovent yellow and black extraction hose assembly is most
visible to the user.
The extraction hose has a Safety Disconnect Coupling built
in, this to protect the system against misuse. The hose is
positioned in the Saddle which connects to the balancer. The
balancer is connected to the aluminium track via a special
trolley. This enables the balancer to move inside the aluminium
profile which is positioned above and to the tailpipe side of the
vehicle.
The aluminium profile is designed to a three (3) section
principle of which two (2) sections have open areas, one on
the underside and one on the overside. The overside open area
is used for positioning the support legs, duct and exhaust hose
connector and the release valve. The underside open area is
used for positioning the end stops and for the sliding the
trolley.
Method of use:
An automatic, pneumatic controlled exhaust gas extraction
system, specially designed for fire and rescue vehicles with low
level, side exhaust pipes. The system is used to remove the
poisonous petrol and diesel gas fumes direct at the emission
source, the exhaust pipe.
When the vehicles are on their way out of the station, the
extraction hose, connected to the exhaust by a special device
called a Grabber®, moves along with the vehicle.
Poisonous diesel gases pass from the Grabber®, up the
extraction hose and into the ducting and extraction fan before
escaping to the atmosphere.
As the vehicles drive out through the doors, the trolley moves
over a release valve on the track, which releases the air
pressure in the Grabber® allowing it to disconnect the ex-
haust pipe.
On the return of the vehicle to the station, The SBT
Pneumatic Grabber
®
is easily re-connected to the exhaust
pipe. At the same time the fan automatically starts up and the
vehicle continues to its standard park position.
WARNING!
The use of exhaust removal hose is allowed for:
- Moving of diesel-vehicles in- or out halls / stations.
- Short time maintenance work of diesel-vehicles,
but only if the engine is running on the minimum
rpm.
- The vehicle must leave and enter the station with
a modified speed in order to avoid damage to the
system and possible injury to people.