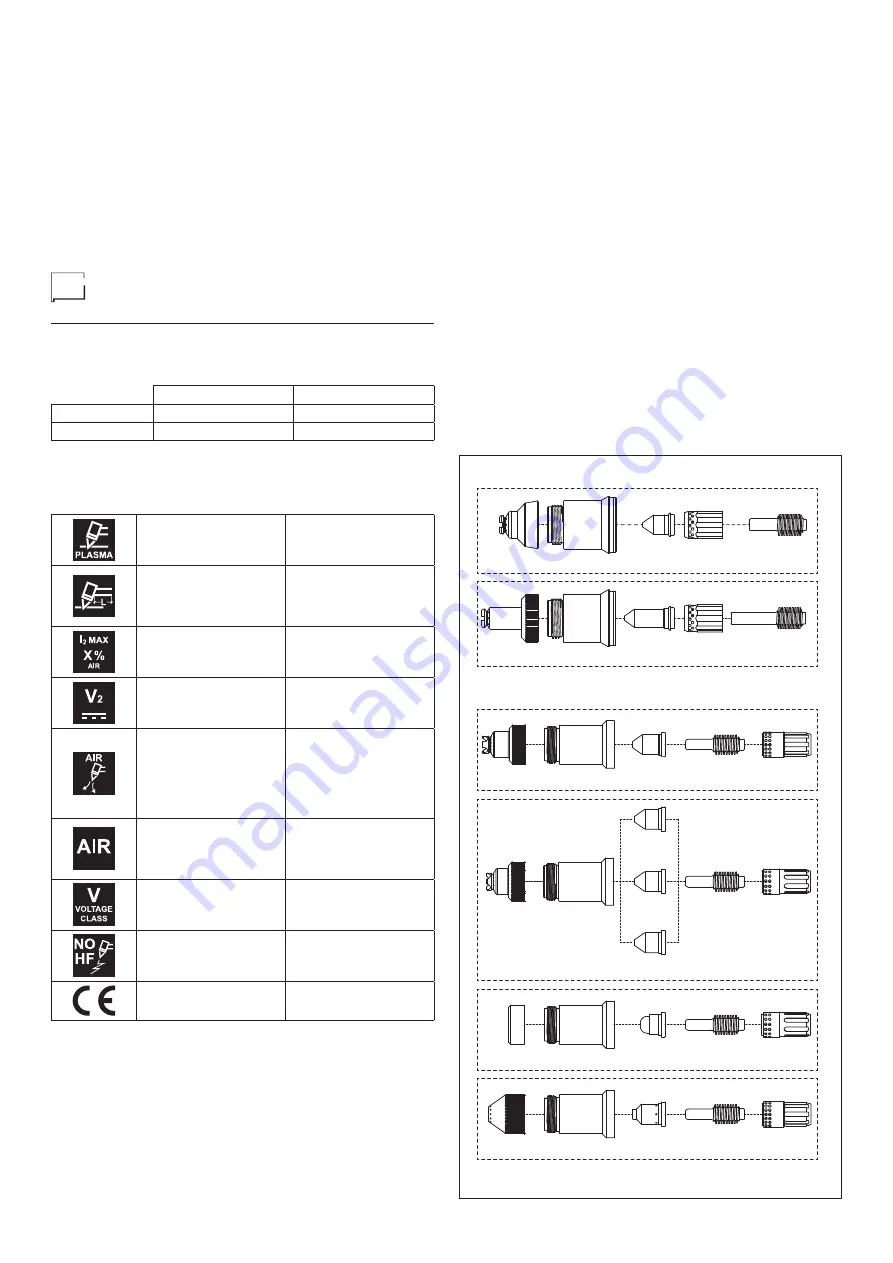
9
device prevents arc transfer in case of incorrect inclination
between the torch and the workpiece.
10) Cut taking care that the fused material flows through the
groove and is not projected in the direction of the torch. If
this occurs, reduce cutting speed.
11) Upon completion of the cutting operation, the air will conti-
nue to issue from the torch for about one minute so as to
cool the torch components. Wait for the air to stop flow-
ing before switching the equipment off. During this time,
you can also start a new cutting operation. If you have to
make cuts near corners or indentations, it is advisable to
use extended electrodes and hoods. If you have to per-
form cir cular cuts, it is advisable to use the special com-
pass sup plied on request.
Configuring the torch
for manual cutting
INTRODUCTION
These machines are supplied with the following standard torch-
es for manual cutting:
Torch
Length
SHARK 75
SK 75
6 m
SHARK 105
SK 125
6 m
Other lengths are available by request.
The torches are air cooled, and do not require special cooling.
The main nominal characteristics of the torches supplied, are
as follows.
SK 75
SK 125
SK 75 = 6 m
(standard)
(Other lengths are
available by request)
SK 125 = 6 m
(standard)
(Other lengths are
available by request)
70 A @ 50%
(10 min. 40°C)
125 A @ 60%
(10 min. 40°C)
DC
DC
5,0-5,5 bar - 72-80 psi
185 l/min - 390 cfh
Cutting: 5,0-6,0 bar /
72-87 psi
Gouging: 4,0-4,5 bar /
58-65 psi
Gas flow @ 125A: 295
l/min - 630 cfh
AIR
- Clean, dry, oil-
free for ISO 8573-1
Class 1.2.2
N
2
- 99.95%
AIR
- Clean, dry, oil-
free for ISO 8573-1
Class 1.2.2
N
2
- 99.95%
M
M
Without HF
Without HF
IEC 60974-7
IEC 60974-7
WORKING LIFESPAN OF CONSUMABLES
The following factors affect the frequency with which consum-
ables need to be replaced:
• Thickness of the metal cut.
• Average cut length.
• Air quality (presence of oil, moisture, or other pollutants).
• Execution of piercing of the metal or cutting from the edge.
• Correct piercing depth.
• Cutting done using mesh or solid material cutting mode. Cut-
ting done in mesh mode give rise to more wear of consum-
ables.
Under normal conditions, the nozzle wears out before the oth-
er consumables during cutting operations.
CONSUMABLES FOR MANUAL CUTTING
Figure F shows the consumables used for the plasma torches
supplied, complete with the CEA order codes.
These torches use shielded consumables and so the point of
the torch can be dragged over the metal to be cut.
To improve the quality of cuts for thin metals (about 2 mm or
less) CLEAN-CUT consumables should preferably be used,
with maximum cutting currents of 45 A (only for SK 125 torch).
100A
125A
100-125A
100-125A
105A
105 A CONTACT CUT
SK 125
SK 75
486029
487631
408612
425023
482136
EXTENDED
STANDARD
486049
424490
408624 (70 A)
408623 (20-50 A)
482134
425059
486049
487630
408610 (70 A)
408609 (20-50 A)
482134
425022
100A
125A
100-125A
105A
486029
487640
408631
425023
482136
105 A GOUGING
45-85A
45-85A
45-85A
45A
45A
45A
65A
85A
45A
85A
45A
85A
45 A max CLEAN-CUT
486028
482030
408613
425023
482135
486028
487632
408614 (45 A)
408615 (65 A)
408616 (85 A)
425023
482135
45-85 A CONTACT CUT
FIG. F
Summary of Contents for SHARK 105
Page 45: ...45 Wiring diagram SHARK 75...
Page 46: ...46 Wiring diagram SHARK 105...