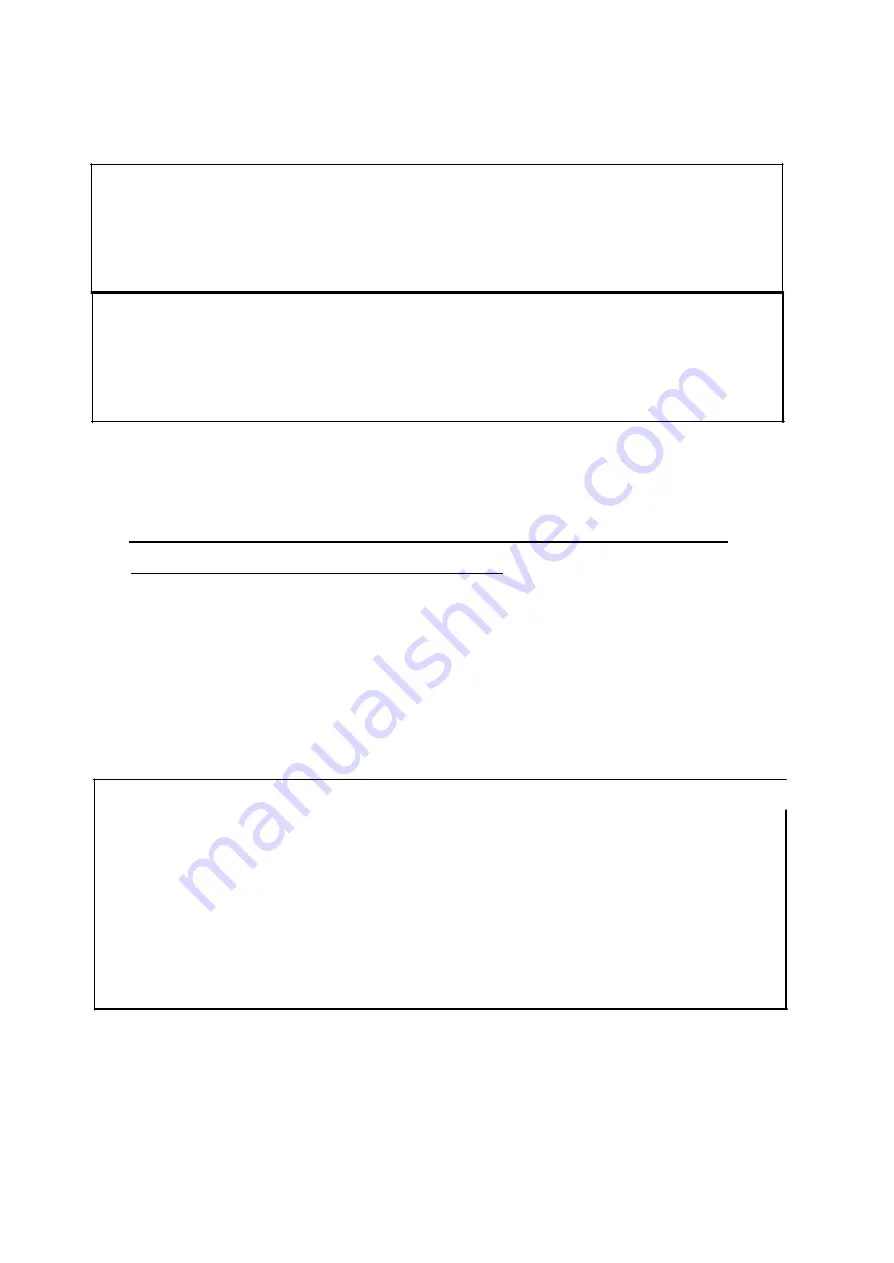
-6
4. Installation
4. 1 Installation
WARNING
Always check the supporting member from which the hoist is suspended is strong
enough to support the weight of the hoist plus the weight of the rated Ioad, etc.
The customer has the responsibility for this.
CAUTION
Only operate the hoist when it is hanging.
Never operate the hoist when the hoist is placed on the floor.
lf operated, irregular winding occurs, causing darnage to the wire rope.
Make certain the hoist is properly installed.
A little extra time and effort in doing so can contribute a Iot toward preventing accidents and
helping you get the best service possible.
The supporting member for the hoist should have successfully passed an
inspection for the applicable safety standard.
• Check the top hook is correctly rigged onto the supporting member and the hook latch is
correctly closed.
• Never use a supporting memberthat suspends the hoist at an angle.
4. 2 Before Air Connection
WARNING
The hoist is designed to operate within a working air pressure range of 0.4,......0.6 MPa
{4,......6kgf/cm, 60---BSpsi}.
• Always keep the working air pressure no greater than 0.6 MPa {6kgf/cm}.
lf necessary, use an air regulator for reducing air pressure.
• Always keep the working air pressure no less than 0.4 MPa {4kgf/cni}.
lf the air pressure is less than 0.4 MPa {4kgf/cni}, the preventive device against reverse
winding which consists of an air pilot valve will not work.
• Check sufficient air can be supplied to the operating area of the hoist.
Campare the air supply from the compressor to the air consumption of the hoist.
(See Chapter 2 "Specifications" .)
Forapipe of excessively small diameter or of great length, the pressure drop can become
large enough to prevent the specified performance.