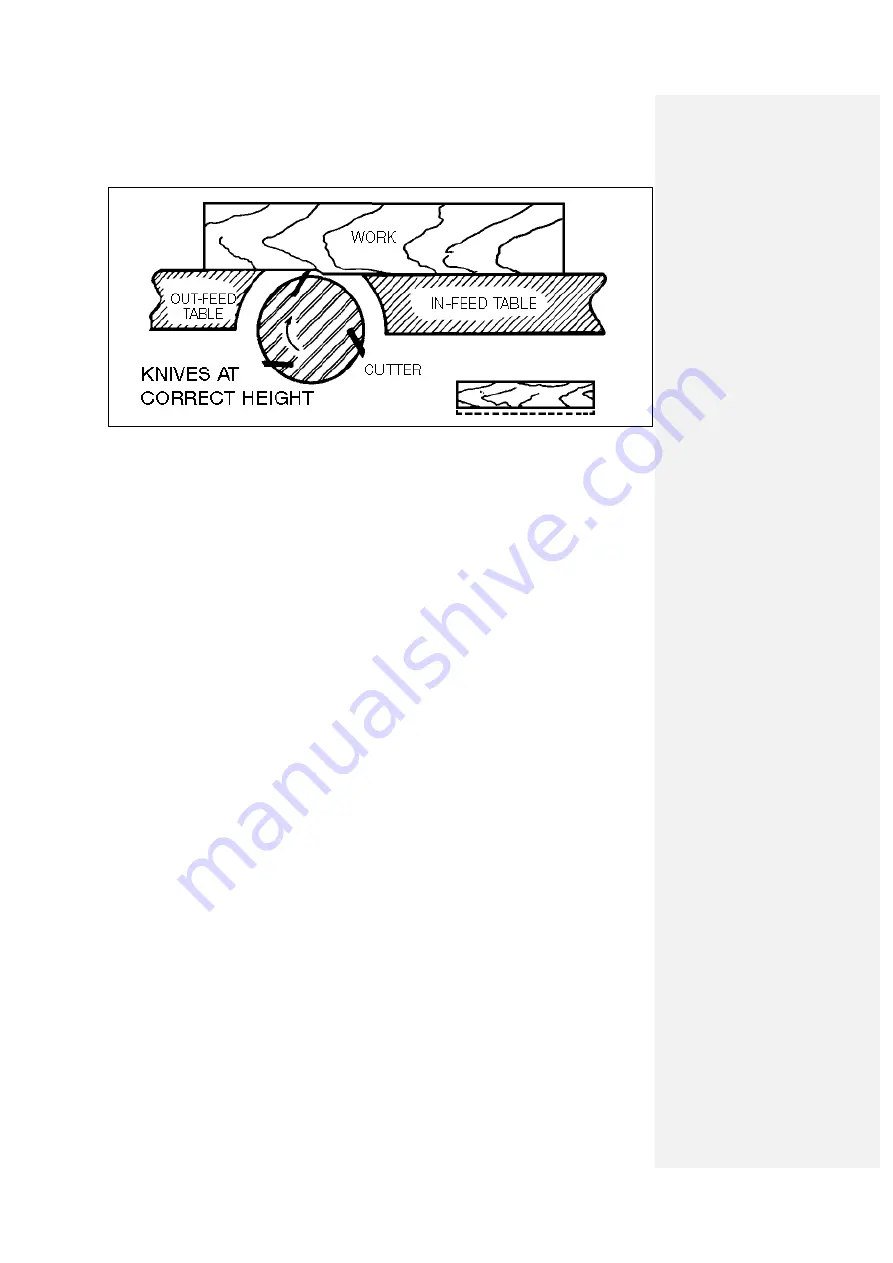
MB502 6” Deluxe Jointer
19
Fig. 45
ADJUSTING TABLE GIBS
“Gibs” are provided to take up all play between the mating dovetail ways of the base and
the infeed and outfeed tables. The “gib” for the infeed table is shown at (A) Fig. 46, and
the “gib” for the outfeed table is shown at (B) Fig. 47. Proper “gib” adjustment is necessary
for the correct functioning of the jointer. The “gibs” were adjusted at the factory and should
require no further adjustment. If, However, it becomes necessary to adjust the “gibs”
proceed as follows.
1.To adjust the infeed or outfeed table “gibs”, loosen three locknuts (F) Fig. 46, for the
infeed table or two locknuts (G) Fig. 47, for the outfeed table.
2. Tighten or loosen three gib adjustment screws (C) Fig. 46, as necessary for the infeed
table or two gib adjustment screws (D) Fig. 47, as necessary for the outfeed table; starting
with the lower screw first and as you proceed to the top screw, gently raise the outboard
edge of the table that is being adjusted. This will offset any tendency for the table casting
to “droop or sag” and permit the gib to be adjusted to a secure fit. After the gibs have been
adjusted, tighten locknuts (F) Fig. 46, (G) Fig. 47.
IMPORTANT:
Do not leave the adjusting screws too loose. It should take a little bit of effort
to move the tables up or down. Jointers are finishing machines and you cannot expect to
get good accuracy or finish if the tables are set loose and sloppy.
FENCE OPERATION
The fence can be moved across the table and can tilt 45 degrees right or left at any
position on the table as follows.
1. To move the fence across the table, loosen lock handle (A) Fig. 48, slide fence to the
desired position on the table and tighten lock handle (A). As the fence is moved across
the table, the rear cutterhead guard (B) covers and guards the cutterhead in back of
the fence.
NOTE:
Lock handle (A) is spring-loaded and can be repositioned by pulling
Summary of Contents for MB502
Page 31: ...MB502 6 Deluxe Jointer 3 Fig 72 Fig 73 ...
Page 32: ...MB502 6 Deluxe Jointer 1 ...
Page 34: ......