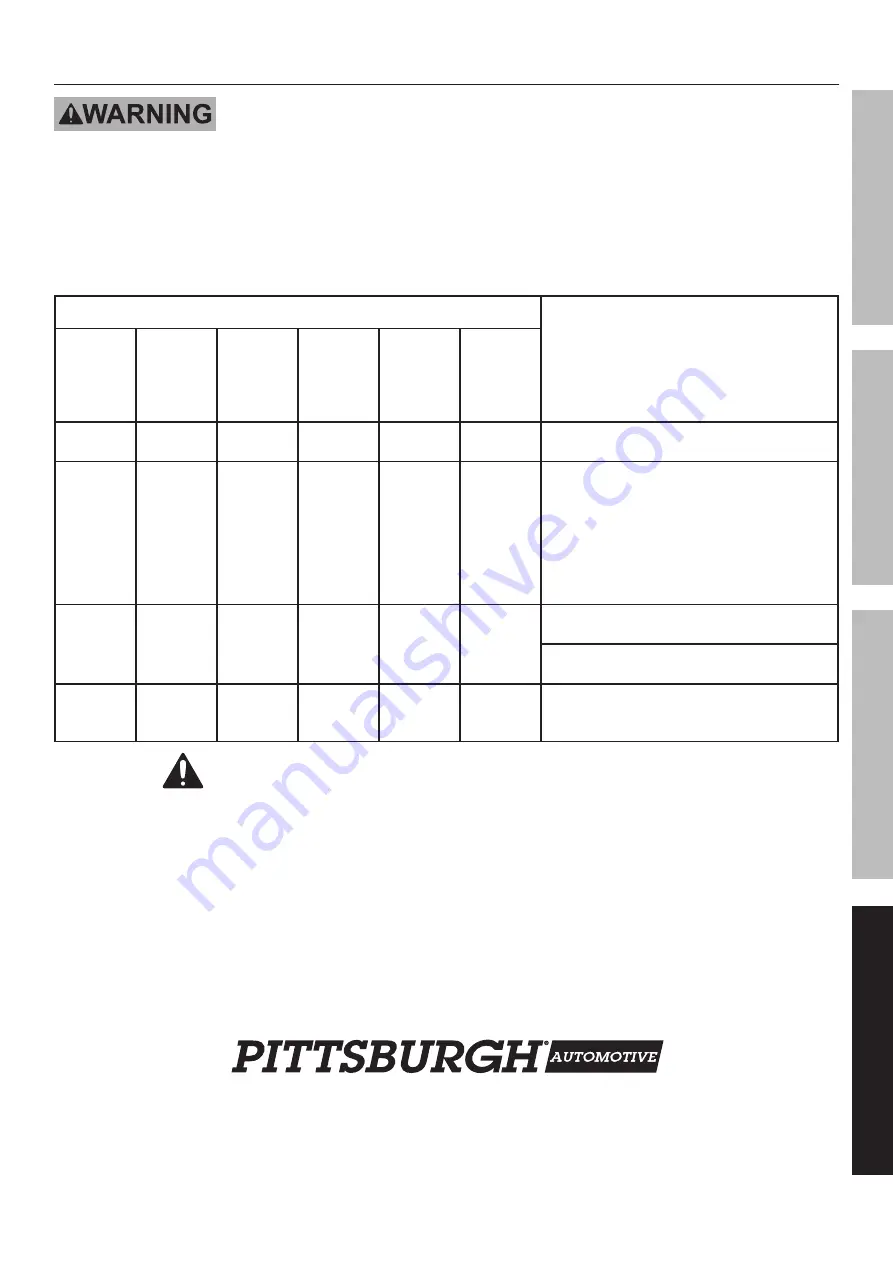
Page 11
For technical questions, please call 1-888-866-5797.
Item 61382
SAFET
y
Op
ERA
TION
M
AINTENAN
c
E
SETU
p
Troubleshooting
TO pREVENT SERIOUS INJURy AND DEATH:
Use caution when troubleshooting a malfunctioning Jack. Stay well clear of the supported load. completely
resolve all problems before use. If the solutions presented in the Troubleshooting guide do not solve the
problem, have a qualified technician inspect and repair the Jack before use.
After the Jack is repaired: Test it carefully without a load by raising and lowering it fully,
checking for proper operation, BEFORE RETURNING THE JAcK TO OpERATION.
DO NOT USE A DAMAGED OR MALFUNcTIONING JAcK!
pOSSIBLE SyMpTOMS
pROBABLE SOLUTION
(Make certain that the jack is not supporting
a load while attempting a solution.)
Jack will
not lift at
its weight
capacity
Saddle
lowers
under
load
Pump
stroke
feels
spongy
Saddle
will not
lift all the
way
Handle
moves up
when jack
is under
load
Fluid
leaking
from fill
plug
X
X
Check that Release Valve is fully closed.
Bleed air from the system.
X
X
X
Valves may be blocked and may not
close fully. To flush the valves:
1. Lower the Saddle and securely
close the Release Valve.
2. Manually lift the Saddle several inches.
3. Open the Release Valve and force the
Saddle down as quickly as possible.
X
X
X
Jack may be low on fluid.
Check the fluid level and refill if needed.
Jack may require bleeding - see Bleeding
Instructions on page 5.
X
Unit may have too much hydraulic
fluid inside, check fluid level
and adjust if needed.
Follow all safety precautions whenever diagnosing or servicing the Jack.
Summary of Contents for 61382
Page 1: ......