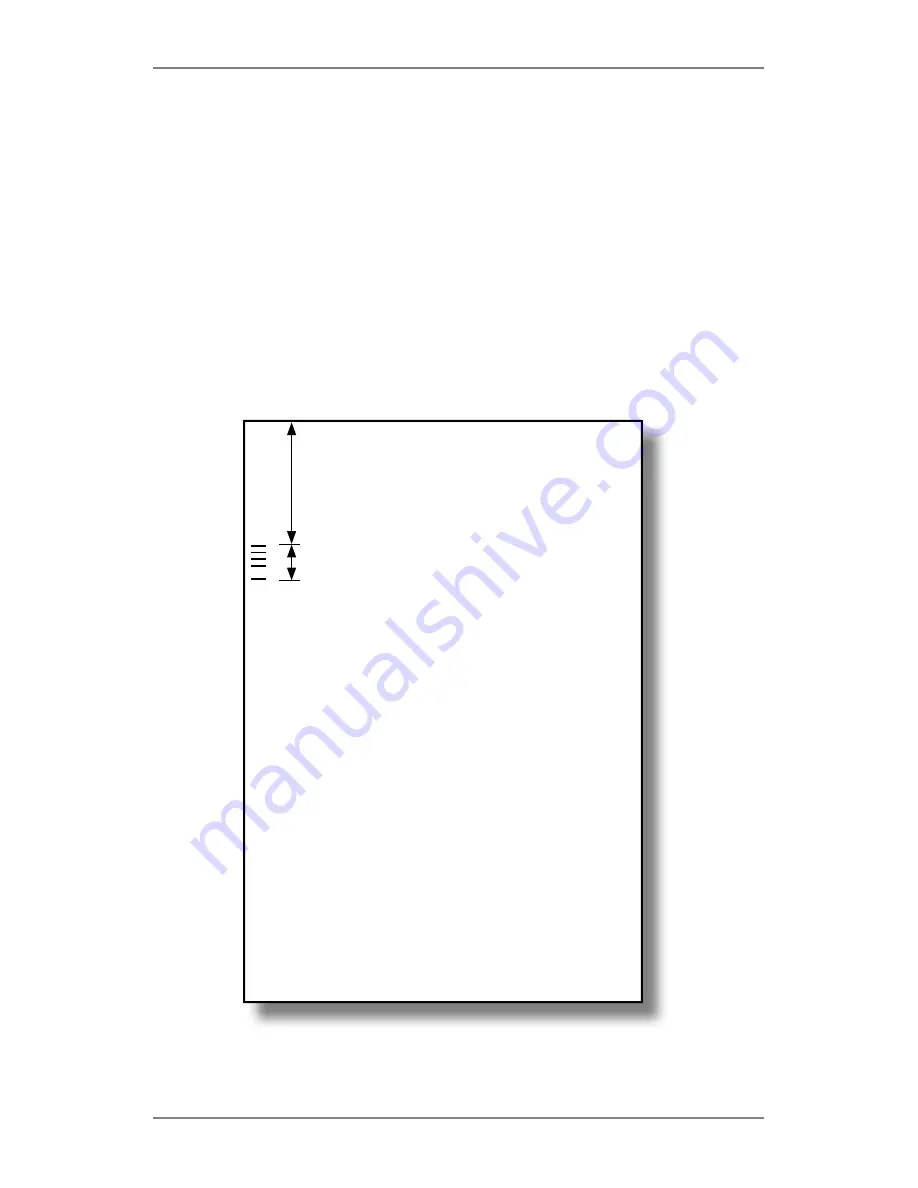
5 • Optical Mark Recognition (OMR)
5-16
SV40221 Rev. A
Defining the first mark position and code length
Take a sheet that
has at least the FIRST and LAST OMR mark
printed on it
.
When requested by the machine, measure and enter the distance
(A) from the top edge of the sheet to the FIRST OMR mark, in
millimetres.
Again, when requested by the machine, measure and enter the
distance (B) from the FIRST OMR mark to the LAST OMR mark, in
millimetres.
A
B
TOP OF SHEET
SV40221 Rev A book.indb 5-16
9/14/2004 5:51:20 PM
Summary of Contents for D1500
Page 1: ...Document Inserting System DI500 DI600 Operator Guide US Canada English Version ...
Page 8: ...vi SV40221 Rev A ...
Page 30: ...2 Using the Menus 2 6 SV40221 Rev A ...
Page 50: ...3 Operator Functions 3 20 SV40221 Rev A ...
Page 80: ...5 Optical Mark Recognition OMR 5 22 SV40221 Rev A ...
Page 96: ...6 Troubleshooting 6 16 SV40221 Rev A ...
Page 116: ...Index I 10 SV40221 Rev A ...
Page 117: ......