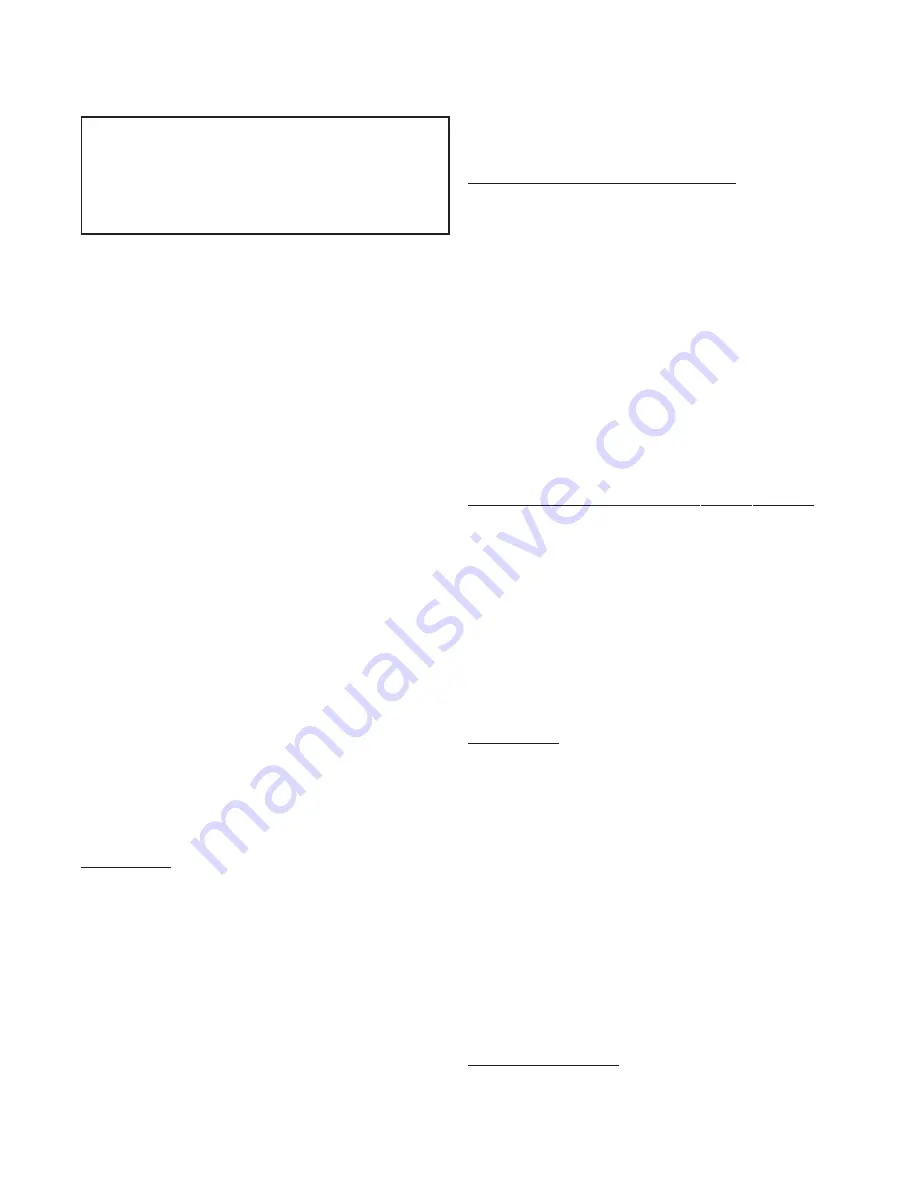
1
INSTALLATION INSTRUCTIONS
CAUTION:
This equipment is manufactured for the use
on a particular type of gas and electrical volt-
age which is specified on the rating plate lo-
cated on the inside of the door.
When your fryers arrive, look them over care-
fully noting any damage on the freight bill. If con-
cealed damage is found after you have accepted
the equipment, report it to the carrier immedi-
ately, as all claims must be filled within 15 days
of the receipt of the shipment. Also, be sure to
keep any packing materials as these will be nec-
essary to make a claim.
Follow these installation instructions carefully.
A proper installation is important for the opera-
tion of the fryers.
In the United States, all installations must con-
form to all local and state codes and well as the
National Fuel Gas Code (ANSI 223.1 1992). In
Canada, installations must be made in accor-
dance to Canadian Standard CAN 1-B149.1 or
.2 “Installation Codes for Gas Burning Appli-
ances & Equipment.”
Electrically operated appliances must be elec-
trically grounded in accordance with local codes;
or in the absence of local codes, with the Na-
tional Electric Code ANSI/NFPA No. 70-1996;
in CANADA, with CSA C22-1 Canadian Electri-
cal Code Part 1.
Ventilation:
A proper ventilation system is also an impor-
tant part of the installation. For information on
the construction and installation of ventilating
hoods, please see “Standard for the Installa-
tion of Equipment for the Removal of Smoke
and Grease Laden Vapors from Commercial
Cooking Equipment”, N.F.P.A. No. 96-1987.
Copies can be obtained by writing to the Na-
tional Fire Protection Association, Battery March
Park, Quincy, MA 02269.
Note:
It is recommended that the ventilation
system be cleaned and maintained on a regu-
lar basis.
Quick Disconnect Gas Connection:
Units equipped with casters must be installed
with connectors that comply with the standards
for connectors for Movable Gas Appliances,
ANSI Z21.69-1987, and Addenda Z21.69A-
1989. (CAN/CGA - 6.16 and CAN/CGA - 6.9.)
This connection should include a quick discon-
nect device that complies with the Standard for
Quick Disconnect Devices for use with Gas Fuel,
ANSI Z21.41-1989. When installing a quick discon-
nect you must also install a means of limiting the
movement of the fryer. This device will prevent the
gas line or quick disconnect from being strained.
Fuel Supply Line Leak and Pressure Testing:
The fuel supply system must be tested before the ma-
chine can be used. If the fuel line is going to be tested
at a pressure greater than (
>
)
1
/
2
PSI (3.45 kPa), make
sure that the unit is disconnected from the fuel line.
If the fuel line is going to be tested at a pressure
equal to or less than (
≤
)
1
/
2
PSI (3.45 kPa), the ma-
chine can be connected to the supply but the gas valve
must be shut.
Clearances:
Minimum clearance of 6" (15cm) must be main-
tained from combustible construction on each
side and the rear of the equipment. This equip-
ment may be installed on combustible floors.
Maintain a minimum of 24" (61cm) clearance in
front of the fryer to provide for proper operation,
maintenance and servicing.
NOTE:
Do not block the area around the bot-
tom or underneath the fryer. The air required to
support the gas combustion is drawn from the
underneath and sides of the fryer.
Leveling the fryers:
Leveling the fryers will help ensure proper opera-
Summary of Contents for AG14S
Page 4: ...ii...
Page 6: ...iv...
Page 10: ...4 Split Vat Fryers LADDER DIAGRAMS Full Vat Fryers...
Page 24: ...18...
Page 25: ...19...
Page 27: ...1 AG14 FRYER PARTS BREAKDOWN...
Page 29: ...3...
Page 31: ...5 1 2 3 4 5 6 7 8 9 10 11 13 13...
Page 33: ...7 SEE DETAIL A SEE DETAIL A 2 3 4 1 5 6 7 8 9 10 11 14 12 13 15...
Page 35: ...9...
Page 37: ...11...
Page 39: ...13 3 7 8 10 12 13 2 4 5 6 9 11 1...
Page 41: ...15...