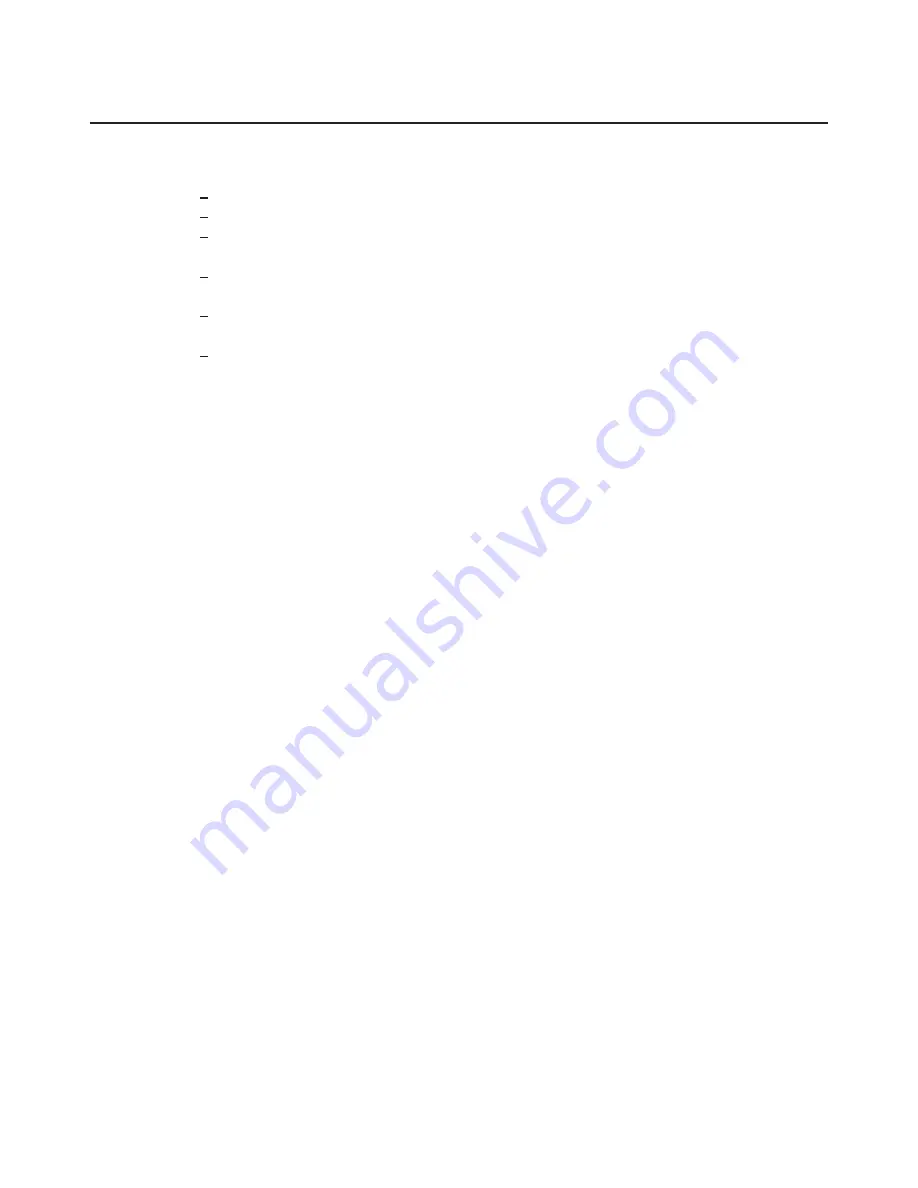
0. FILLING MAIN GEAR OLEO STRUT. (cont.)
(b) Method II.
1 Remove the filler plug from the top of the strut housing.
2 Raise the strut to full compression.
3 Pour fluid from a clean container through the filler opening until it is visible at the top of
the strut chamber.
4 Lower the gear until the wheel touches the ground and then fully compress and extend the
strut three or four times to remove any air from the housing.
5 Raise the strut to full compression and if needed, fill with fluid to the bottom of the filler
plug.
6 Apply thread lubricant (Parker 6PB) to the threads of the filler plug. Reinstall the filler
plug and torque to 45 foot-pounds.
5. With airplane raised, retract and extend gear strut several times to ascertain that the strut actuates
freely. The weight of gear fork and wheel should extend strut.
6. Clean off overflow of fluid and inflate strut as described in Inflating Oleo Struts.
7. Check that fluid is not leaking around the strut piston at the bottom of the housing.
P. INFLATING OLEO STRUTS.
Make certain that oleo strut has sufficient fluid and that torque link is properly connected. Attach a strut
pump to air valve and inflate oleo strut to proper visible piston extension, or a pressure of 250 ± 25 psi (for
the main gear struts) and 225 ± 22.5 psi for the nose gear strut.
When using pressure method pistons must be fully extended by raising aircraft off ground. (Refer to
Chapter 7 Lifting and Shoring) .
When using the extension method, the aircraft should be fully serviced with fuel and engine oil and resting
on its landing gear. Inflate strut until correct inches of piston is exposed. Rock aircraft several times to
ascertain that gear settles back to the correct strut position. If a strut pump is not available, raise aircraft
and use line pressure from a high pressure air system. Lower aircraft and, while rocking it, bring strut
down to proper extension by releasing air from valve.
Check for valve core leakage before capping valve.
Q. BRAKE SYSTEM.
The brake system incorporates a hydraulic fluid reservoir through which the brake system is periodically
serviced. Fluid is drawn from the reservoir by the brake cylinders to maintain the volume of fluid required
for maximum braking efficiency. Spongy brake pedal action is often an indication that the brake fluid
the system, these instructions may be found in Chapter 32.
R. FILLING BRAKE CYLINDER RESERVOIR.
The brake cylinder reservoir is located on the left side of the firewall in the engine compartment. It should
be checked at every 50 hour inspection and replenished as necessary. Fill with MIL-H-5606 fluid to level
marked on reservoir, No brake adjustment of is necessary, though they should be checked periodically per
instructions given in Chapter 32.
PIPER AIRCRAFT
PA-32R-301/301T
MAINTENANCE MANUAL
12-10-00
Page 12-11
Reissued: July 1, 1993
1F14
Summary of Contents for PA-32R-301T SARATOGA S
Page 26: ...CHAPTER 4 AIRWORTHINESS LIMITATIONS 1C1 ...
Page 29: ...CHAPTER 5 TIME LIMITS MAINTENANCE CHECKS 1C4 ...
Page 53: ...CHAPTER 6 DIMENSIONS AND AREAS 1D6 ...
Page 64: ...CHAPTER 7 LIFTING AND SHORING 1D21 ...
Page 68: ...CHAPTER 8 LEVELING AND WEIGHING 1E1 ...
Page 72: ...CHAPTER 9 TOWING AND TAXIING 1E5 ...
Page 76: ...CHAPTER 10 PARKING AND MOORING 1E9 ...
Page 80: ...CHAPTER 11 REQUIRED PLACARDS 1E13 ...
Page 92: ...CHAPTER 12 SERVICING 1F1 ...
Page 126: ...CHAPTER 20 STANDARD PRACTICES AIRFRAME 1G17 ...
Page 127: ...THIS PAGE INTENTIONALLY LEFT BLANK ...
Page 139: ...CHAPTER 21 ENVIRONMENTAL SYSTEMS 1H5 ...
Page 188: ...CHAPTER 22 AUTOFLIGHT 1J7 ...
Page 193: ...CHAPTER 23 COMMUNICATIONS 1J12 ...
Page 203: ...CHAPTER 24 ELECTRICAL POWER 1J22 ...
Page 263: ...CHAPTER 25 EQUIPMENT FURNISHINGS 2A13 ...
Page 269: ...CHAPTER 27 FLIGHT CONTROLS 2A20 ...
Page 332: ...CHAPTER 28 FUEL 2D11 ...
Page 363: ...CHAPTER 29 HYDRAULIC POWER 2E18 ...
Page 404: ...CHAPTER 30 ICE AND RAIN PROTECTION 2G16 ...
Page 470: ...CHAPTER 32 LANDING GEAR 3A13 ...
Page 550: ...CHAPTER 33 LIGHTS 3D24 ...
Page 562: ...CHAPTER 34 NAVIGATION AND PITOT STATIC 3E12 ...
Page 582: ...CHAPTER 35 OXYGEN 3F8 ...
Page 604: ...CHAPTER 37 VACUUM 3G6 ...
Page 616: ...CHAPTER 39 3G18 ELECTRIC ELECTRONIC PANELS MULTIPURPOSE PARTS ...
Page 620: ...CHAPTER 51 STRUCTURES 3G22 ...
Page 636: ...CHAPTER 52 DOORS 3H14 ...
Page 650: ...CHAPTER 55 STABILIZERS 3I4 ...
Page 662: ...CHAPTER 56 WINDOWS 3I16 ...
Page 670: ...CHAPTER 57 WINGS 3I24 ...
Page 688: ...CHAPTER 61 PROPELLER 3J18 ...
Page 704: ...CHAPTER 70 STANDARD PRACTICES ENGINES 3K10 ...
Page 708: ...CHAPTER 71 POWER PLANT 3K14 ...
Page 737: ...CHAPTER 73 ENGINE FUEL SYSTEM 4A13 ...
Page 749: ...CHAPTER 74 IGNITION 4B1 ...
Page 783: ...CHAPTER 77 ENGINE INDICATING 4C11 ...
Page 793: ...CHAPTER 78 EXHAUST 4C21 ...
Page 801: ...CHAPTER 79 OIL 4D5 ...
Page 805: ...CHAPTER 80 STARTING 4D9 ...
Page 819: ...CHAPTER 81 TURBINES 4D23 ...
Page 833: ...CHAPTER 91 CHARTS WIRING DIAGRAMS 4E13 ...