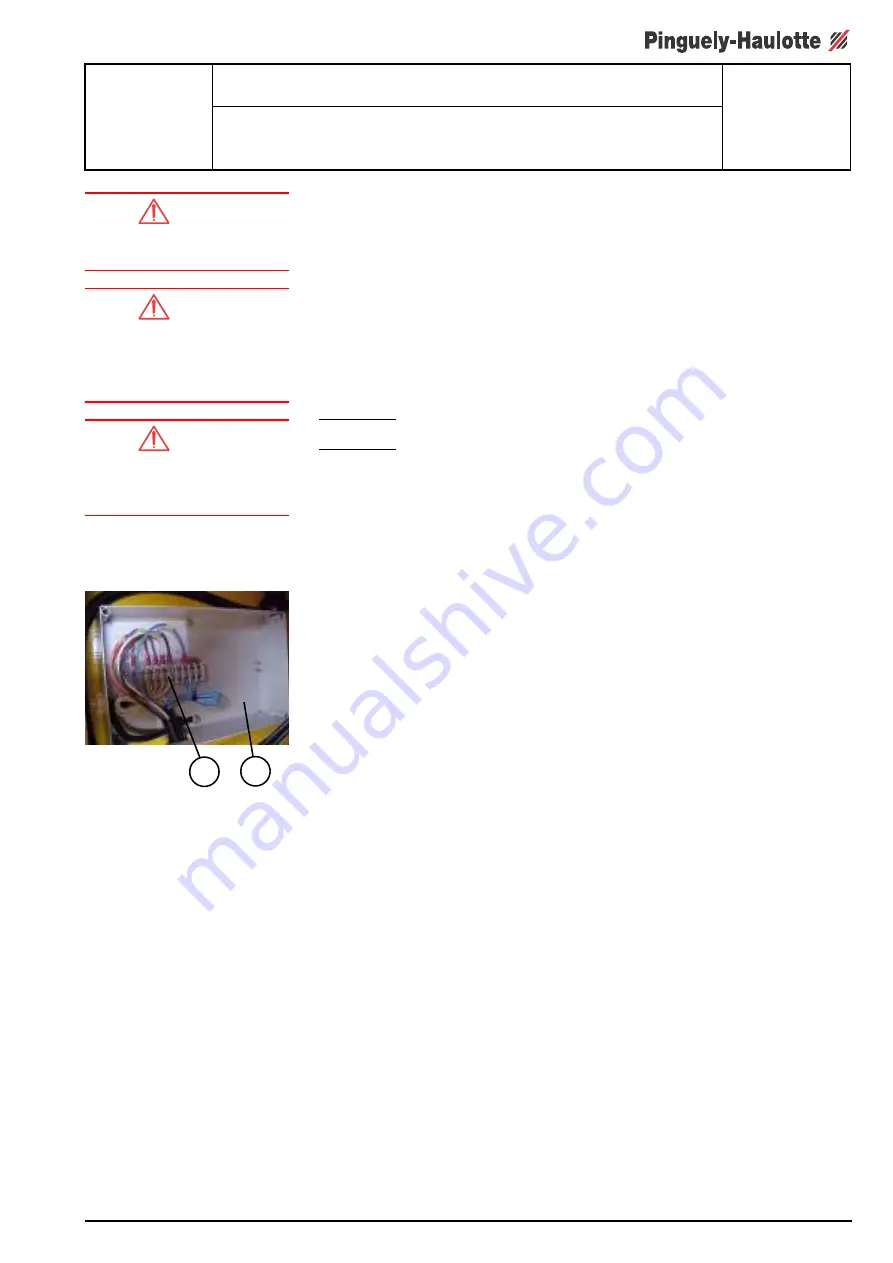
CORRECTIVE MAINTENANCE SHEET
Folio 1/3
CHANGING THE SLEW RING
Sheet C106
Caution!
Ensure that the oil is not too
hot.
Caution!
Ensure that the lifting
equipment is in good
condition and of sufficient
capacity.
Caution!
Use a container to collect oil
to prevent pollution of the
environment.
1
2
1 - Preliminary operations
•
Move the turntable to the locking position.
•
Put the machine in the maintenance configuration (see corresponding
paragraph).
•
Switch off electric power (see corresponding paragraph).
2 - Removing the slew ring
•
Open the chassis box (1), mark and disconnect all electric connectors (2).
•
Free the electric wiring harness (3) of the swing joint (4) after marking its
path.
•
Mark and disconnect the hoses of the swing joint (4) under the chassis
(travel motor oil supply and return).
NB:
Unscrew the hoses slowly to release residual hydraulic pressure.
•
Put caps on the hoses.
•
Remove the swing joint’s rotation stop screw (5).
•
Put the turntable in slings and unlock the turntable rotation blocking pin.
•
Remove the 24 screws (6) and washers fixing the slew ring to the lower
part (7) of the machine.
•
Remove the turntable carefully, avoiding damage to the swing joint (4).
•
Wedge the ring (8), mark its position in relation to the turntable.
•
Remove the 24 screws (9), bolts (10) and washers fixing the slew ring (8)
to the turntable.
•
Free the turntable.
3 - Installing the slew ring
•
Put the slew ring (8) into place on suitable supports in the position marked
during dismantling.
•
Position the turntable on the ring.
•
Fix the ring with the 24 screws (9), bolts (10) and washers without pre-
stressing.
•
Tighten in a star pattern (see figure 2) to a torque of 27 m.daN (199 lb.ft).
•
Place the tur ring assembly on the chassis in the locking position.
•
Fix the ring (8) to the chassis (7) using the 24 screws (6) and washers
without pre-stressing.
•
Tighten in a star pattern (see figure 2) to a torque of 27 m.daN (199 lb.ft).
•
Remove the slings from the turntable.
•
Put back the rotation stop screw (5) of the swing joint (4).
•
Reconnect the hoses of the swing joint (4) according to the marks made
during dismantling.
•
Reconnect the electric connectors (2) of the chassis box (1) according to
the marks made during dismantling.
•
Adjust the position of the reducing gear (11) using the adjusting screws
(12) and (13):
- Turn the reducing gear to position the ring teeth marked with a colour
opposite the reducing gear pinion (this coloured mark corresponds to the
most excentric point of the ring).
- Adjust the gap between the teeth to 300
µ
m with a set of flakes.
- When the gap is set, block the counter-nuts of the adjustment screws
(12) and (13).
4 - Additional operations
•
Put the machine back in the operational configuration.
•
Lubricate the ring.
Summary of Contents for HA20PX
Page 2: ......
Page 4: ...1 Repair manual 2...
Page 10: ...Repair Manual vi 15 CORRECTIVE MAINTENANCE PROCEDURES 177...
Page 26: ...Repair Manual 20...
Page 28: ...Repair Manual 22...
Page 36: ...Repair Manual 30...
Page 46: ...135 Repair manual 40...
Page 47: ...Repair manual 135 41 7 SAFETY LOCATION...
Page 48: ...135 Repair manual 42...
Page 51: ...Repair manual 135 45 8 1 3 Positions of fuses 19 22 26 27 23 25 24 21 20...
Page 64: ...135 Repair manual 58...
Page 66: ...135 Repair manual 60...
Page 74: ...Repair manual 68 12 7 2 Commom orange label 6...
Page 82: ...135 Repair manual 76...
Page 84: ......
Page 86: ...PREVENTIVE MAINTENANCE SHEET...
Page 88: ...PREVENTIVE MAINTENANCE SHEET...
Page 98: ......
Page 100: ......
Page 104: ......
Page 108: ......
Page 110: ......
Page 118: ......
Page 128: ......
Page 134: ......
Page 140: ......
Page 144: ......
Page 152: ......
Page 180: ......
Page 186: ......
Page 188: ......
Page 190: ......
Page 192: ......
Page 194: ......
Page 196: ......
Page 198: ......
Page 200: ......
Page 202: ......
Page 204: ......
Page 206: ......
Page 208: ......
Page 212: ......
Page 214: ......
Page 216: ...CORRECTIVE MAINTENANCE SHEET...
Page 218: ......
Page 220: ......
Page 222: ......
Page 224: ......
Page 226: ......
Page 228: ......
Page 230: ......
Page 234: ......
Page 236: ......
Page 238: ......
Page 240: ......
Page 246: ......
Page 248: ...CORRECTIVE MAINTENANCE SHEET Folio 2 2 CHANGING THE HYDRAULIC PUMP Sheet C091 7 6 3 3 1 2 4 5...
Page 250: ......
Page 252: ......
Page 254: ......
Page 256: ......
Page 258: ......
Page 265: ...CORRECTIVE MAINTENANCE SHEET Folio 3 3 CHANGING THE SLEW RING Sheet C106 12 13 11...
Page 266: ......
Page 268: ......
Page 270: ......
Page 272: ......
Page 274: ...CORRECTIVE MAINTENANCE SHEET Folio 2 2 CHANGING THE JIB CYLINDER Sheet C115 2 4 3 5 1...
Page 278: ......
Page 282: ...CORRECTIVE MAINTENANCE SHEET CHANGING THE COUNTERWEIGHTS Sheet C134...