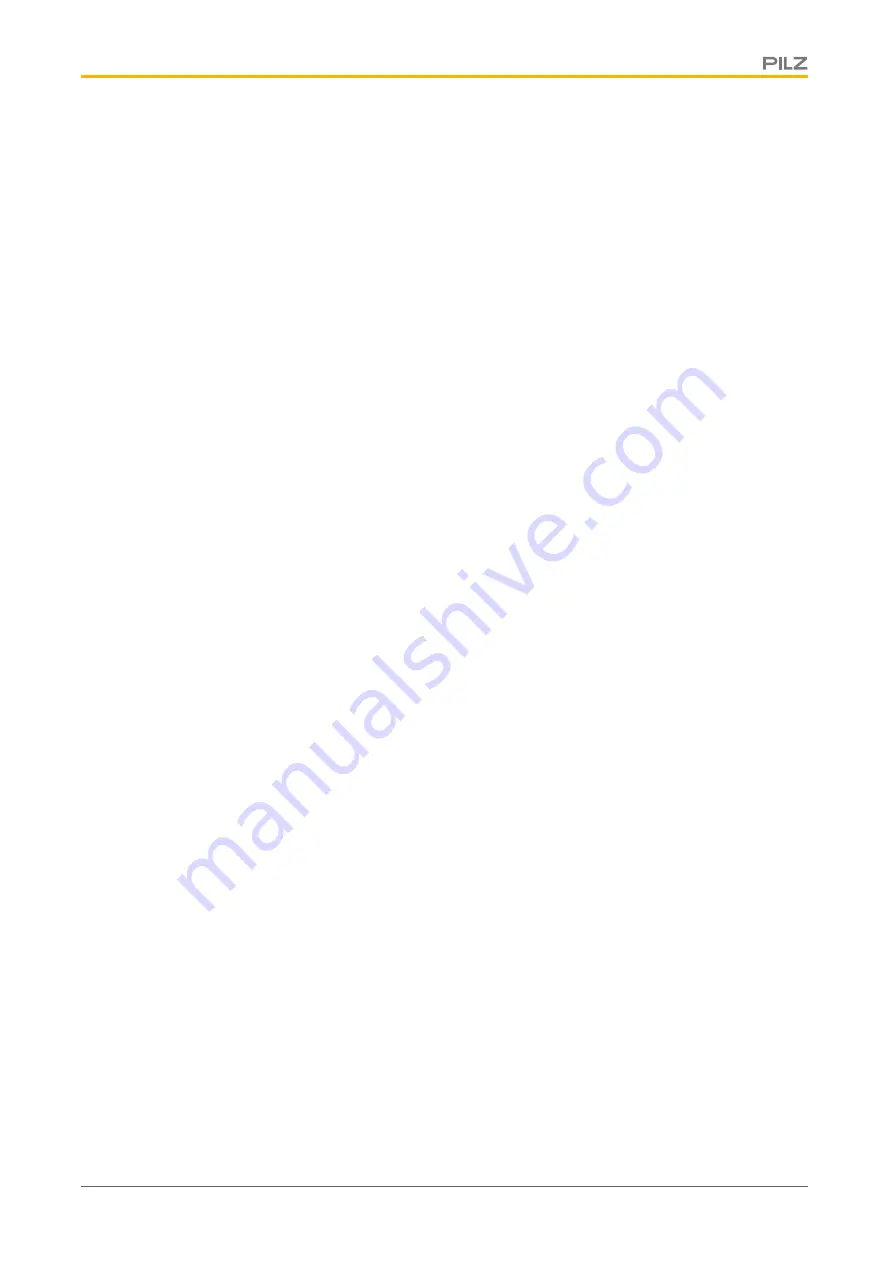
Function description
Operating Manual PSSu E S 2AI I se(-T)
21417-EN-04
13
4.2.2
Integrated protection mechanisms
When the PSSu E F PS1(-T) or PSSu E F PS2(-T)(-R) is used to supply the system, the
module supply is buffered for 20 ms if the supply voltage is interrupted.
The module detects the following errors:
}
Start-up error
}
Configuration error
}
ST communication error
}
Bus termination error
4.3
Configuration
The module can be configured using the system software.