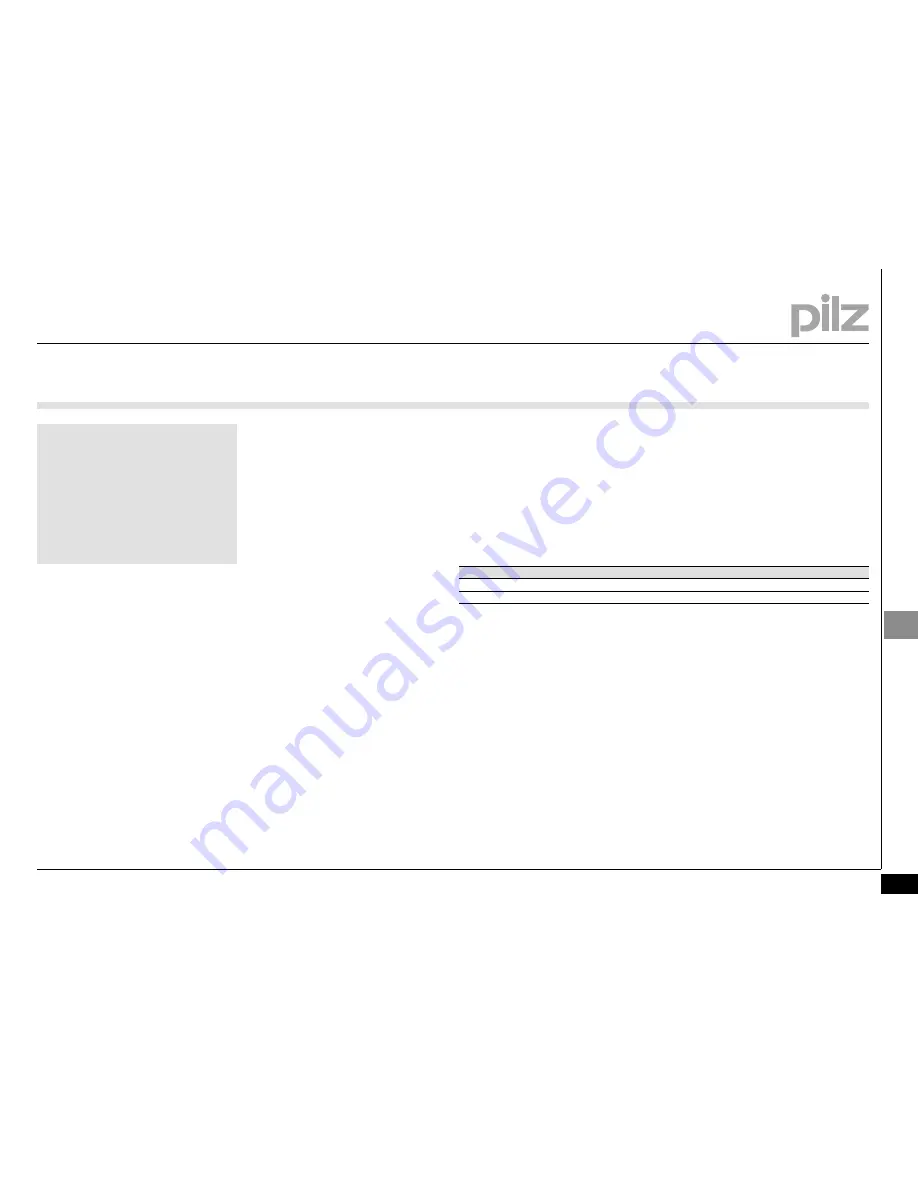
Safety Gate Applications
5.1-
Pilz GmbH & Co. KG, Felix-Wankel-Straße 2, 73760 Ostfildern, Germany, Telephone: +49 711 3409-0, Telefax: +49 711 3409-133, E-Mail: [email protected]
2011-10
2.2-2
2.2
PL e of EN ISO 13849-1, SIL 3 of EN 62061
PNOZ s3 – Dual-channel operation, Safety switch PSEN cs2.1p
Pilz products
Number
Designation
Order number
1
PNOZ s3
750 103
1
PSEN cs2.1p
540 100
Features
Dual-channel operation with detection
of shorts across contacts via safety
switch
Monitored reset with falling edge
Contact expansion through positive-
guided contactors
Feedback loop to monitor contact ex-
pansion
Description
Safety gate function
The opening and closing of a safety gate is
signalled to the safety relay PNOZ s3 (K2)
via the semiconductor outputs on the safety
switch PSEN cs2.1p (S3). The
semiconductor outputs on safety switch S3
are opened as soon as the safety gate is
opened. As a result the input circuit on the
safety relay PNOZ s3 (K2) is interrupted and
the safety contacts on the PNOZ s3 (K2)
open. Contactors K3 and K4 de-energise.
Settings on the unit
The terminator on the PNOZ s3 must be
connected.
The operating mode selector switch
(mode) on the safety relay PNOZ s3 must
be set to “Monitored reset, falling edge
without detection of shorts across
contacts (In2+)“.
Start/reset
The safety relay PNOZ s3 (K2) can be
started by pressing reset button S4 if:
The safety gate is closed and
The semiconductor outputs on the safety
switch S3 are closed and
Contactors K3 and K4 have de-
energised.
Feedback loop
The positive-guided N/C contacts on
contactors K3 and K4 are monitored in the
feedback loop S12-S34 of the safety relay
K2.
Safety assessment
The safety relay K2 and contactors K3
and K4 must be installed in a single
mounting area (control cabinet) in order
to exclude a short across the output.
Earth faults and shorts between contacts
in the input circuit are detected through
the safety switch S3.
A fault on the device does not lead to the
loss of the safety function.
The safety relay PNOZ s3 (K2) can be
started when the input circuit at K2 is
closed first, followed by reset button S4.
This avoids an unwanted reset before the
input circuit is closed or as a result of the
reset button being overridden.
Increased protection against
manipulation is required for hazardous
machinery such as presses. In this case
we recommend using two safety
switches per safety gate.
If the position of the operating mode
selector switch (mode) is changed during
operation, an error message will be
triggered; the safety contacts on K2
open. This fault condition can only be
rectified by switching the supply voltage
on the safety relay K2 off and then on
again.