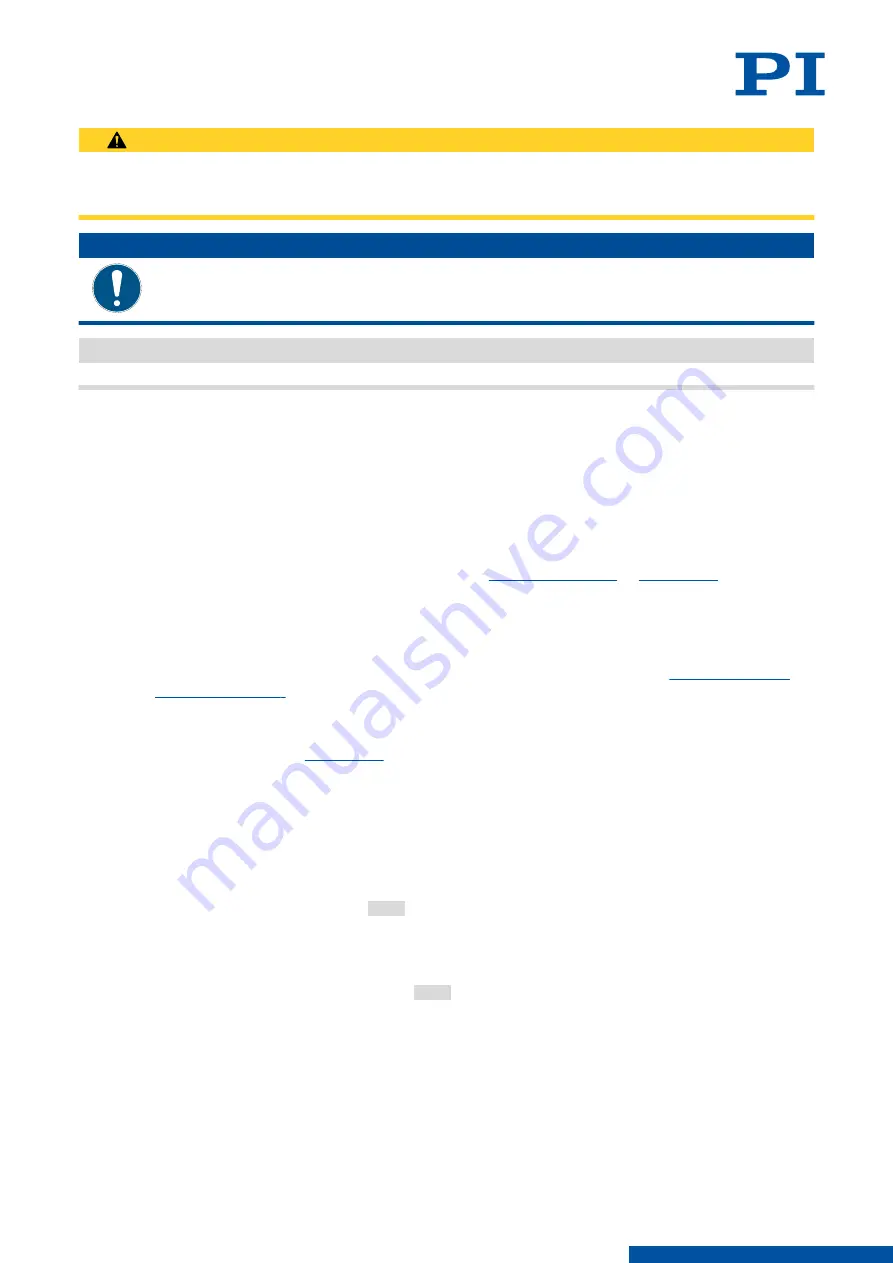
CAUTION
Dangerous situation
Failure to observe can lead to minor injury.
►
Actions to take to avoid the risk.
NOTICE
Dangerous situation
Failure to observe can lead to material damage.
►
Action to take to avoid the risk.
Information
Additional information on the L-417.xx9211E0B that can affect your application.
2.3
Figures
For better understandability, the colors, proportions and degree of detail in illustrations can
deviate from the actual circumstances. Photographic illustrations may also differ and must
not be seen as guaranteed properties.
2.4
Downloading Manuals
The latest versions of the user manuals can be
at
For products that are supplied with software (data storage device in the scope of delivery),
access to the manuals is protected by a password. Protected content is only displayed on the
website after entering the access data. You need the data storage device for the product to
get the access data.
If a manual is missing or problems occur with downloading, contact our
Downloading Manuals
1. Open the website
2. If the product was shipped with a data storage device: Log into the website:
a) Click
Login
.
b) Enter the login data.
The login data is in the
[...]_Releasenews_[...].pdf
on the product's data storage
device (in the main directory or the
Manuals
directory).
If necessary: Follow the link and register yourself to get the login data.
c) Click
Login
or press the Enter key.
3. Search for the product:
a) Click
Search
.
b) Enter the product number up to the period (e.g., L-417) into the search field.
c) Click
Start search
or press the Enter key.
d) If necessary: Click
Load more results
at the bottom of the list.
4. Click the corresponding product in the list of search results.
5. Click the
Downloads
tab.
➔
The manuals are shown under
Documentation
.
6. Click the desired manual and save it.
2 ABOUT THIS DOCUMENT
L417M0015EN
‒
9/10/2019
6
M O T I O N | P O S I T I O N I N G