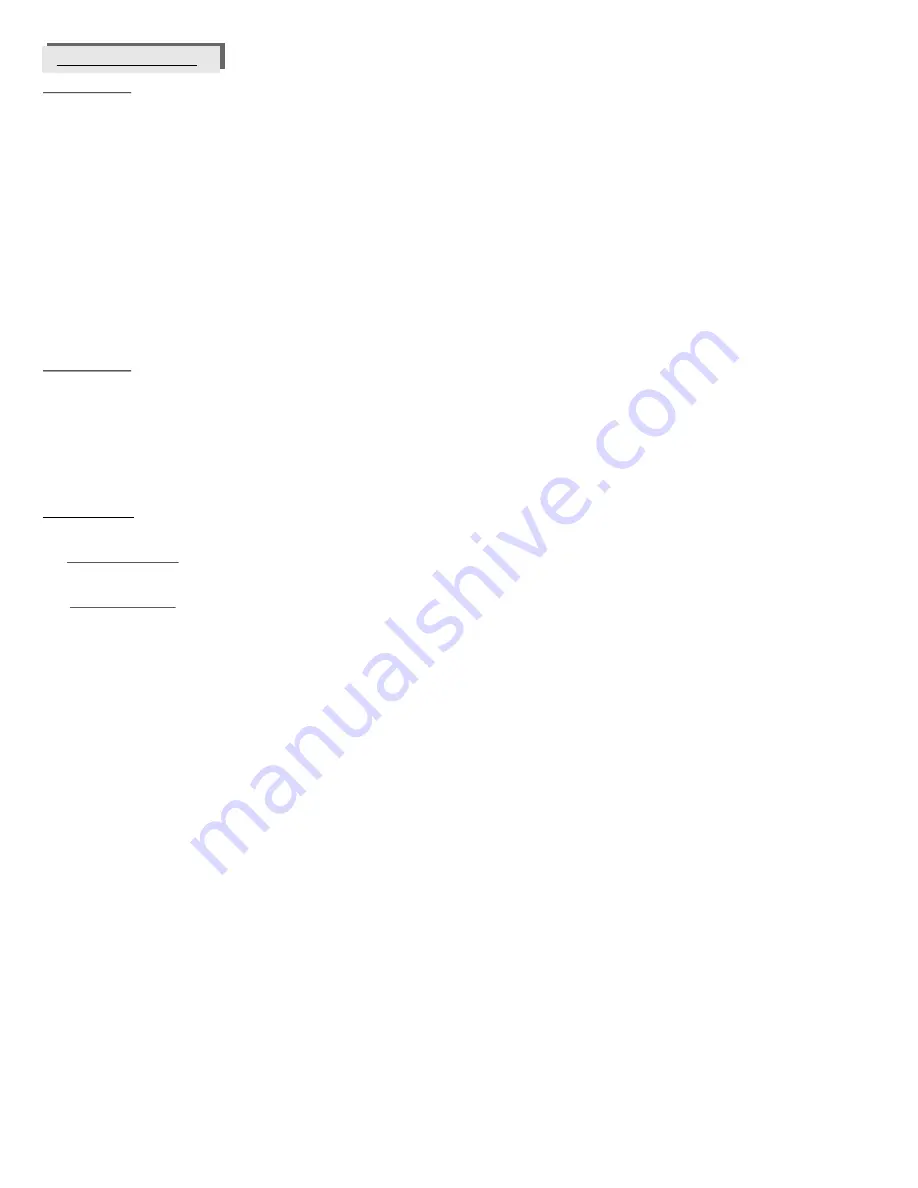
INSTALLATION
CAUTION:
Disconnect all electrical power to the cooler
before attempting to install, open, or service your cooler.
More than one disconnect will be required to de-energize
the equipment for servicing. If the cooler is
thermostatically controlled, the thermostat may not be
used as the power supply disconnect, as it may reset and
start the unit unexpectedly.
Even while routinely inspecting or servicing the inside, the cooler can
be accidentally started. Keep all personnel away from the cooler and
electrical supply when you are working on it. Before servicing or
cleaning unit, switch power off at the service disconnects and lock the
disconnecting means to prevent power from being switched on
accidentally. When the service disconnects cannot be locked,
securely fasten a prominent warning device, such as a tag, to the
service disconnect or panel.
Electric Power Supply Requirements
CAUTION:
All electrical installations must comply with
local and national building & safety codes; all work must
be performed by qualified personnel only.
NOTE
- References in this manual to: National Electric Code
(N.E.C.), local or national codes means that those items must
comply with applicable installation codes as specified by the building
code authority having jurisdiction at the installation location. It is the
installer's duty to comply with all requirements.
IMPORTANT:
This UL Classified Evaporative Air Cooler requires the use of
two separate electrical power supply circuits to the unit:
1. Blower (fan) motor:
!
Single phase - 115, 208, 230 Volt AC / 60 Hz
!
3 phase - 200, 208, 230, 460 Volt AC / 60 Hz
2.
Circulating pump: (depending on model, more than one pump
per unit may be required, see catalog information)
!
Single phase - 115 or 230 Volt AC / 60 Hz. The pump power
supply circuit must be a GFCI protected circuit.
Make sure that the circulating pump and (where used) a single
voltage blower motor (i.e.; 115V, 230V) are connected to the voltage
and frequency (Hz) stamped on each component's specification
plate. Make sure that a multiple voltage blower motor (i.e., 115/208-
230V) has been properly connected internally to match the available
power supply voltage, per the connection diagram on the motor's
specification plate.
NOTE: Improper motor voltage connections will void
motor warranties.
The motor Hp / full load current, voltage, phase, number of motor
speeds and the length of wire from the power supply to the motor are
all factors in determining the gauge of wire used in the circuit.
Safety Disconnect Switches
Each unit must have safety disconnect switches (motor circuit and
pump circuit) compatible with the installation location and installed in
accordance with the National Electric Code (N.E.C.), Article 430
and/or local codes. Each disconnect switch shall be a U.L. Listed
disconnect which breaks all ungrounded conductors that can carry
current to the unit.
Over-current (short circuit) Protection
Each unit must have over-current protection equipment intended to
protect all ungrounded pump and motor branch-circuit conductors,
motor control apparatus, pumps and motors against overcurrent due
to short circuits or ground faults. They shall have minimum enclosure
classifications compatible with the installation location and installed
in accordance with N.E.C., Articles 240 and 430. These devices shall
be U.L. Listed short circuit protection devices, sized and installed in
accordance with specifications as stated in N.E.C., Article 430.
Overload Protection
All pumps and single-phase motors available from Phoenix
Manufacturing, Inc. for use in Industrial/Commercial coolers have
integral thermal running and locked rotor overload protection as
required by the N.E.C.
All 3-phase motors require installation of properly sized and mounted
thermal running / locked rotor overload protection.
Branch circuit protection should be properly sized and installed by a
competent electrician in accordance with local and national code
requirements.
Motor Start Switch / Motor Starter
All motor applications require the use of Start/Stop switches
and/or motor starters of the proper current capacity.
In applications where a switch is deemed adequate to start the motor,
as defined by N.E.C., Article 430, the branch circuit shall be sized in
accordance with N.E.C., Articles 210 and 430. The enclosure for the
switch and its installation location shall comply with N.E.C.
requirements for the installation of the switch.
A motor starter with integral thermal (running and locked rotor)
overload protection is used to start/stop 3-phase motors. Motor
starter shall be sized in accordance with specifications stated in the
N.E.C., Article 430. Starters mounted to the unit shall have a
minimum NEMA 3R (raintight/rainproof) enclosure rating. Starters
mounted remote to the unit shall have a minimum enclosure
classification compatible with the location and installed in
accordance with N.E.C., Article 430.
Pump Power Supply Circuit
The pump supply circuit shall be a GFCI protected circuit with
overcurrent (short circuit) protection of 15 AMP and have a minimum
of #14 AWG copper wire to the pump receptacles in the junction box
assembly. Conduit to the junction box shall be rain-tight or liquid-
tight, flexible metal conduit with a separate ground wire, installed per
N.E.C., Article 351.
Electrical Ground
For maximum safety, make sure cooler cabinet, blower motor and
pump(s) are properly grounded to a suitable ground connection as
required by all local and national codes.
Motor Installation
!
Mount blower motor to the motor mount using the four carriage
bolts and nuts provided in the parts bag. Tighten nuts enough to
hold motor in place until belt(s) have been installed, aligned
and properly tensioned.
!
Connect motor to electrical power supply, as required, making
sure motor is wired for proper rotation (some single phase and
all 3 phase motors are bi-directional). See arrow on blower
housing.
!
Adjust motor sheave for expected blower RPM requirement
(refer to cooler design/capacity selection tables and RPM
information available in the catalog
!
Insert motor sheave onto the motor shaft, align by vertically
centering motor pulley inline with blower pulley, tighten
setscrew to 95 in-lbs.
!
Install belt(s) from motor sheave to the blower pulley and adjust
belt tension (see “Belt Adjustment”).
!
Rotate blower wheel by hand to see that it moves freely without
rubbing against housing.
!
After motor and belt(s) are installed, complete the motor
mounting process by insuring all screws, nuts and bolts are
tightened down properly.
UL Classified Industrial / Commercial Evaporative Cooler Use and Care Manual 3