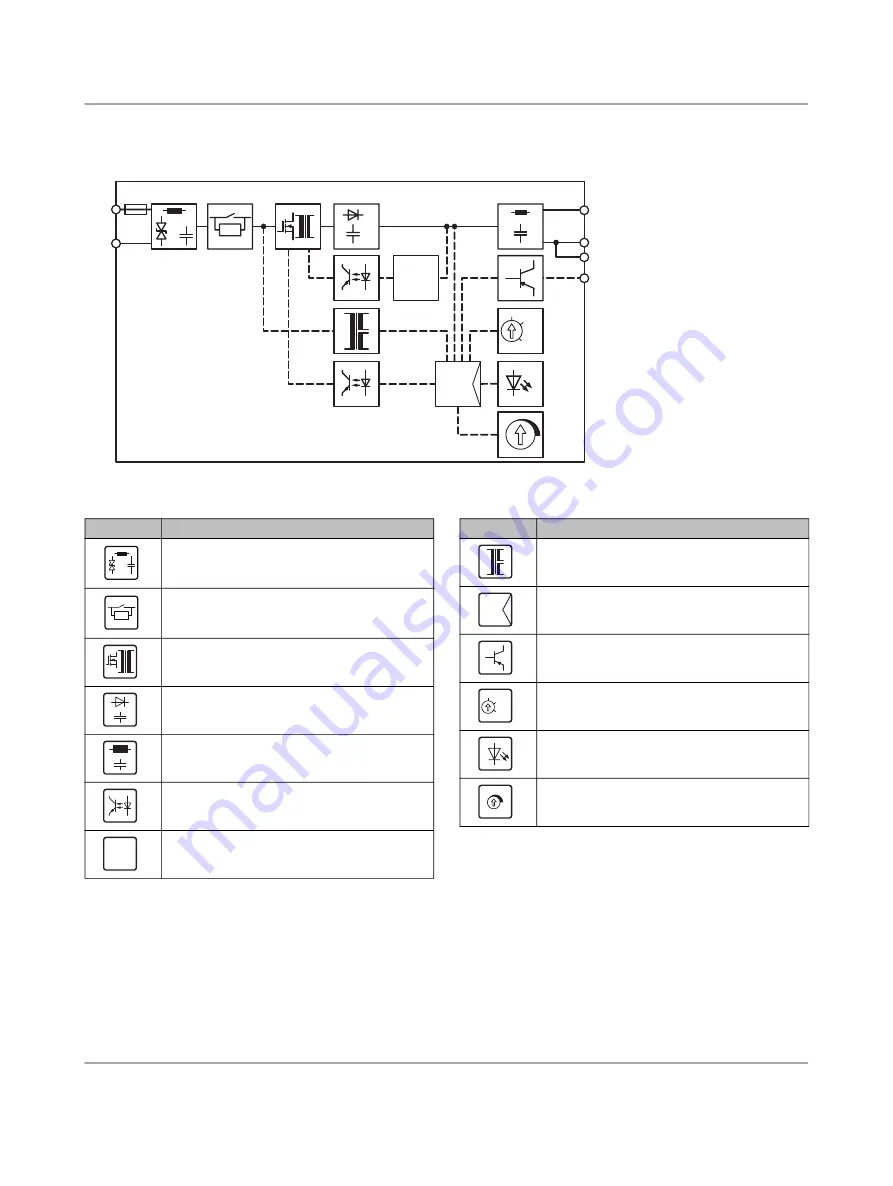
QUINT4-PS/12-24DC/5-15DC/2.5/PT
110260_en_00
PHOENIX CONTACT
17/30
7.4
Block diagram
Figure 6
Block diagram
Key
OVP
SIG
Ď
C
3.1
SIG
2.2
2.3
-
2.1
+
1.1
+
1.2
-
-
Symbol
Designation
Surge protection (diode) with filter
Inrush current limitation
Switching transistor and main transmitter
(electrically isolating)
Secondary rectification and smoothing
Filter
Optocoupler (electrically isolating)
Additional regulatory protection against
surge voltage
OVP
Symbol
Designation
Auxiliary converter (electrically isolating)
Microcontroller
PNP transistor switch output
Rotary selector switch
Signal/display LEDs
Potentiometer output voltage
C
SIG